RB at Celosphere 2020
公司规模
1,000+
国家
- Canada
- United States
产品
- Celonis
- SAP
- RPA
技术栈
- Process Mining
- ERP
- Data Analytics
实施规模
- Enterprise-wide Deployment
影响指标
- Cost Savings
- Customer Satisfaction
- Productivity Improvements
技术
- 分析与建模 - 过程分析
- 自动化与控制 - 自动化与过程控制系统
- 功能应用 - 企业资源规划系统 (ERP)
适用行业
- 消费品
- 食品与饮料
- 医疗保健和医院
适用功能
- 商业运营
- 采购
- 质量保证
用例
- 预测性维护
- 过程控制与优化
- 供应链可见性(SCV)
服务
- 数据科学服务
- 系统集成
- 培训
关于客户
RB, a global consumer goods company with over 40,000 employees and a 200+ year heritage, operates in three business units: Hygiene, Health, and Nutrition. The company sells over 20 million products daily across 190+ countries and has a revenue of £12.85 billion. RB is committed to protecting, healing, and nurturing in the relentless pursuit of a cleaner, healthier world. The company aims to make access to high-quality hygiene, wellness, and nourishment a right, not a privilege. RB has been a member of the FTSE4Good Index for 15 consecutive years and has saved 61k tonnes of CO2e from the purchase and generation of renewable electricity.
挑战
RB faced the challenge of harmonizing and optimizing multiple processes across its global operations. The company needed to improve process transparency, root cause analysis, and end-user experience. Additionally, RB aimed to enhance its process and control environment through real-time continuous monitoring and to simplify and automate processes to focus on value-added activities.
解决方案
RB implemented Celonis, introduced by EY as part of a controls transformation agenda, to support its ERP deployment and digital transformation journey. The solution provided real-time end-to-end process transparency and root cause analysis based on facts and data. RB's journey with Celonis began with a proof of value on P2P in June 2018, followed by a project kick-off and build in September 2019, covering five processes: O2C, AR, PO, AP, and VIM. By January 2020, RB had launched global KPIs with 350 users and 1.4 TB of data across two ERP templates. The company conducted process value workshops in Q2 2020 to drive adoption and usage in five pilot markets.
运营影响
数量效益
Case Study missing?
Start adding your own!
Register with your work email and create a new case study profile for your business.
相关案例.
.png)
Case Study
Improving Vending Machine Profitability with the Internet of Things (IoT)
The vending industry is undergoing a sea change, taking advantage of new technologies to go beyond just delivering snacks to creating a new retail location. Intelligent vending machines can be found in many public locations as well as company facilities, selling different types of goods and services, including even computer accessories, gold bars, tickets, and office supplies. With increasing sophistication, they may also provide time- and location-based data pertaining to sales, inventory, and customer preferences. But at the end of the day, vending machine operators know greater profitability is driven by higher sales and lower operating costs.

Case Study
The Kellogg Company
Kellogg keeps a close eye on its trade spend, analyzing large volumes of data and running complex simulations to predict which promotional activities will be the most effective. Kellogg needed to decrease the trade spend but its traditional relational database on premises could not keep up with the pace of demand.
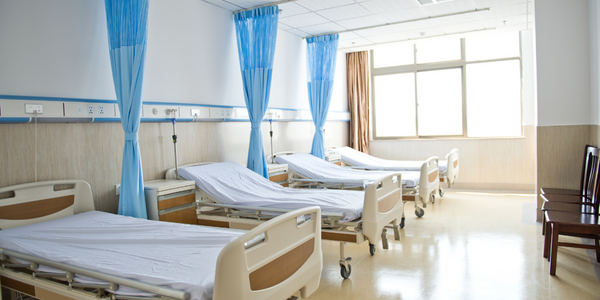
Case Study
Hospital Inventory Management
The hospital supply chain team is responsible for ensuring that the right medical supplies are readily available to clinicians when and where needed, and to do so in the most efficient manner possible. However, many of the systems and processes in use at the cancer center for supply chain management were not best suited to support these goals. Barcoding technology, a commonly used method for inventory management of medical supplies, is labor intensive, time consuming, does not provide real-time visibility into inventory levels and can be prone to error. Consequently, the lack of accurate and real-time visibility into inventory levels across multiple supply rooms in multiple hospital facilities creates additional inefficiency in the system causing over-ordering, hoarding, and wasted supplies. Other sources of waste and cost were also identified as candidates for improvement. Existing systems and processes did not provide adequate security for high-cost inventory within the hospital, which was another driver of cost. A lack of visibility into expiration dates for supplies resulted in supplies being wasted due to past expiry dates. Storage of supplies was also a key consideration given the location of the cancer center’s facilities in a dense urban setting, where space is always at a premium. In order to address the challenges outlined above, the hospital sought a solution that would provide real-time inventory information with high levels of accuracy, reduce the level of manual effort required and enable data driven decision making to ensure that the right supplies were readily available to clinicians in the right location at the right time.

Case Study
HEINEKEN Uses the Cloud to Reach 10.5 Million Consumers
For 2012 campaign, the Bond promotion, it planned to launch the campaign at the same time everywhere on the planet. That created unprecedented challenges for HEINEKEN—nowhere more so than in its technology operation. The primary digital content for the campaign was a 100-megabyte movie that had to play flawlessly for millions of viewers worldwide. After all, Bond never fails. No one was going to tolerate a technology failure that might bruise his brand.Previously, HEINEKEN had supported digital media at its outsourced datacenter. But that datacenter lacked the computing resources HEINEKEN needed, and building them—especially to support peak traffic that would total millions of simultaneous hits—would have been both time-consuming and expensive. Nor would it have provided the geographic reach that HEINEKEN needed to minimize latency worldwide.
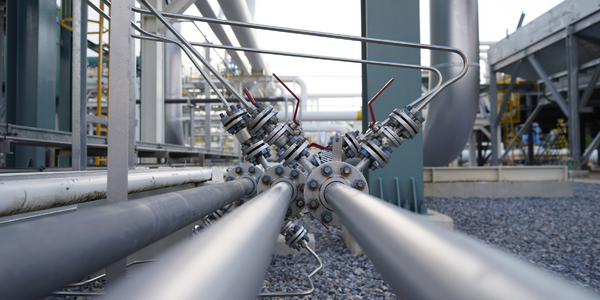
Case Study
Gas Pipeline Monitoring System for Hospitals
This system integrator focuses on providing centralized gas pipeline monitoring systems for hospitals. The service they provide makes it possible for hospitals to reduce both maintenance and labor costs. Since hospitals may not have an existing network suitable for this type of system, GPRS communication provides an easy and ready-to-use solution for remote, distributed monitoring systems System Requirements - GPRS communication - Seamless connection with SCADA software - Simple, front-end control capability - Expandable I/O channels - Combine AI, DI, and DO channels