Outsourcing Captures More Nonprofit Donations
公司规模
Large Corporate
地区
- America
国家
- United States
产品
- C.H. Robinson's Inbound Logistics Program
- C.H. Robinson's Transportation Program
技术栈
- LTL Consolidation
- Rail and Truck Transportation
- Warehousing
实施规模
- Enterprise-wide Deployment
影响指标
- Cost Savings
- Customer Satisfaction
- Waste Reduction
技术
- 功能应用 - 仓库管理系统 (WMS)
- 网络与连接 - 低功耗广域网
适用功能
- 物流运输
- 仓库和库存管理
用例
- 车队管理
- 供应链可见性(SCV)
- 仓库自动化
服务
- 系统集成
关于客户
Harvest Time International (Harvest Time Int’l) is a nonprofit organization that distributes food, clothing, household goods, and medical supplies to over 500 local, national, and international ministries and nonprofit organizations. Since its inception in 1991, Harvest Time Int’l has served more than 20 million people and has received the “Best in America” seal from the Independent Charities of America. The organization’s mission is to increase donations and serve more people through an expanded distribution program. Harvest Time Int’l’s donors are located around the country and value relationships with organizations that can pick up donations quickly and efficiently.
挑战
Harvest Time Int’l’s goal to increase donations and serve more people could not be accomplished without an expanded distribution program. The organization needed to optimize donations by contracting with individual transportation providers and geographically favorable warehouse space, which was often time-consuming and expensive. Load flexibility was also crucial, as donors had varying quantities of products to donate. To satisfy donors’ demands for load flexibility and quick response times, Harvest Time Int’l needed a strategy for collecting LTLs within hours of being notified, requiring cost-efficient warehousing and transportation.
解决方案
C.H. Robinson developed an outsource solution for Harvest Time Int’l that includes inbound logistics and customized pickup plans for donations, as well as LTL consolidation, rail and truck transportation, warehousing, and scheduling of donated product shipments. The transportation program quickly improved Harvest Time Int’l’s response time and increased product donations from existing and new donors. C.H. Robinson oversees a matrix of local transportation and warehouse operators near several donor reclamation and distribution centers, providing daily less than truckload (LTL) pickup and storage. As LTL loads are aggregated into more economical full truckloads, they are either shipped to Harvest Time Int’l by C.H. Robinson or rerouted by Harvest Time Int’l directly to other ministries or nonprofits. The program accommodates donors who have neither storage space for donations nor yard equipment by arranging for a drop trailer to be placed at the dock door. When the trailer is full, C.H. Robinson picks it up and drops off another empty trailer to be filled.
运营影响
数量效益
Case Study missing?
Start adding your own!
Register with your work email and create a new case study profile for your business.
相关案例.

Case Study
Remote Temperature Monitoring of Perishable Goods Saves Money
RMONI was facing temperature monitoring challenges in a cold chain business. A cold chain must be established and maintained to ensure goods have been properly refrigerated during every step of the process, making temperature monitoring a critical business function. Manual registration practice can be very costly, labor intensive and prone to mistakes.
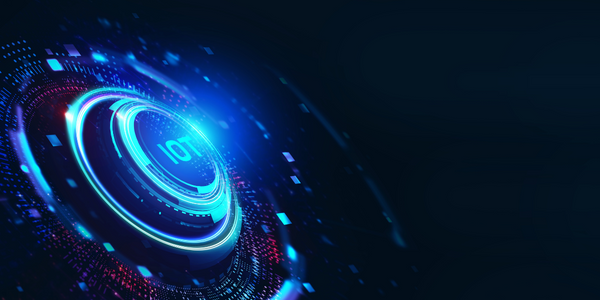
Case Study
IoT Solution for Cold Chain
Most of the customer's warehouses run on utility and generator power. Since these warehouses are in remote locations, power outages are a very common scenario. Diesel fuel, thereby, becomes a significant cost for these warehouses. Energy consumption was also very high due to the lack of a consistent temperature throughout the facility. This lack of a consistent temperature in all areas and no way to control it, resulted in the customer losing a significant amount of their temperature sensitive goods due to spoilage.
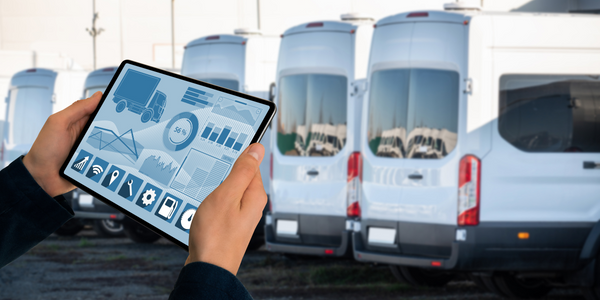
Case Study
IoT-based Fleet Intelligence Innovation
Speed to market is precious for DRVR, a rapidly growing start-up company. With a business model dependent on reliable mobile data, managers were spending their lives trying to negotiate data roaming deals with mobile network operators in different countries. And, even then, service quality was a constant concern.
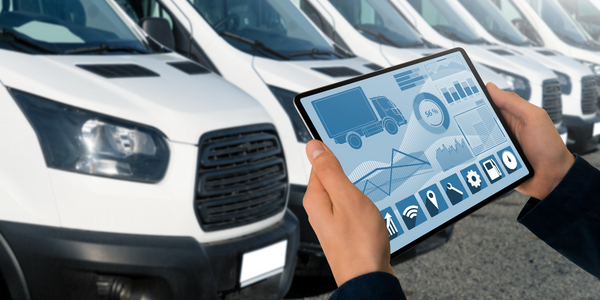
Case Study
Vehicle Fleet Analytics
Organizations frequently implement a maintenance strategy for their fleets of vehicles using a combination of time and usage based maintenance schedules. While effective as a whole, time and usage based schedules do not take into account driving patterns, environmental factors, and sensors currently deployed within the vehicle measuring crank voltage, ignition voltage, and acceleration, all of which have a significant influence on the overall health of the vehicle.In a typical fleet, a large percentage of road calls are related to electrical failure, with battery failure being a common cause. Battery failures result in unmet service agreement levels and costly re-adjustment of scheduled to provide replacement vehicles. To reduce the impact of unplanned maintenance, the transportation logistics company was interested in a trial of C3 Vehicle Fleet Analytics.
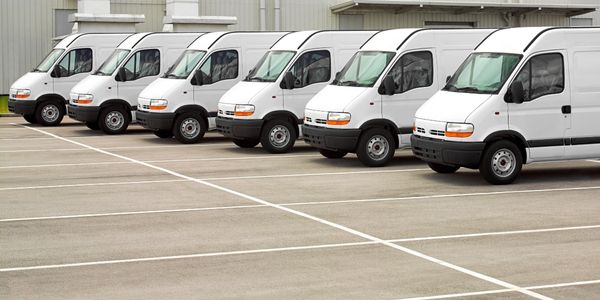
Case Study
Zonar Takes the Wheel with a M2M Solution
Zonar’s fleet management solutions collect, report and analyze data before, during and after a vehicle’s trip. The company needed Machine-to-Machine (M2M) connectivity to enable communication between in-vehicle devices and back-end systems. To deliver high volumes of potentially sensitive information from and to moving vehicles – and keep pace with its rapid business growth – Zonar wanted a highly secure solution that it could easily manage and that had the required national and global reach.