Airgas Breathes Easy with Ruan Partnership
公司规模
Large Corporate
地区
- America
国家
- United States
产品
- Ruan Transportation Management System
- Airgas Merchant Gases
技术栈
- Fleet Management Software
- Driver Recruitment and Retention Tools
实施规模
- Enterprise-wide Deployment
影响指标
- Customer Satisfaction
- Productivity Improvements
- Employee Satisfaction
技术
- 功能应用 - 车队管理系统 (FMS)
- 功能应用 - 远程监控系统
适用行业
- 化学品
- 医疗保健和医院
- 食品与饮料
适用功能
- 物流运输
- 维护
用例
- 车队管理
- 预测性维护
- 远程资产管理
服务
- 系统集成
- 培训
- 硬件设计与工程服务
关于客户
Airgas Merchant Gases, a division of Airgas, is a leading supplier of industrial, medical, and specialty gases, as well as related equipment. The company serves a wide range of industries, including healthcare, water treatment, metal fabrication, and food processing. Airgas Merchant Gases is committed to safety and customer satisfaction, striving to exceed customer expectations through reliable and efficient service. The company has a long-standing partnership with Ruan, a transportation management company, to handle the logistics of delivering their products. This partnership has allowed Airgas to focus on its core competencies while ensuring the safe and timely delivery of their gases and equipment.
挑战
Airgas Merchant Gases faced significant challenges in managing the transportation of their industrial, medical, and specialty gases. The company needed a reliable partner to handle the logistics of delivering these gases safely and on time to various industries, including hospitals, water plants, metal fabrication companies, and food-freezing facilities. Additionally, Airgas was expanding its operations in Bethlehem, Pennsylvania, and Chester, Virginia, which required seamless integration and efficient management of transportation resources. The company also struggled with recruiting and retaining staff at certain locations, such as Waukesha, Wisconsin, which further complicated their operations.
解决方案
Ruan provided a comprehensive transportation management solution for Airgas, handling every aspect of product transportation from equipment to driver recruitment and retention. With a fleet of 47 tractors and 59 trailers, Ruan's professional drivers covered nearly 7.3 million miles annually, delivering liquid oxygen, nitrogen, and argon to various industries. Ruan's existing infrastructure, including maintenance facilities and management teams, facilitated Airgas' expansion in Bethlehem, Pennsylvania, and Chester, Virginia, without service interruptions. Additionally, Ruan's flexibility and innovative approach helped Airgas overcome staffing challenges at their Waukesha, Wisconsin facility by recruiting and retaining the necessary employees within weeks. The partnership also included shared maintenance facilities and management with another industrial gas provider, Linde, at the Bethlehem location, further optimizing resources and operations.
运营影响
数量效益
Case Study missing?
Start adding your own!
Register with your work email and create a new case study profile for your business.
相关案例.

Case Study
The Kellogg Company
Kellogg keeps a close eye on its trade spend, analyzing large volumes of data and running complex simulations to predict which promotional activities will be the most effective. Kellogg needed to decrease the trade spend but its traditional relational database on premises could not keep up with the pace of demand.
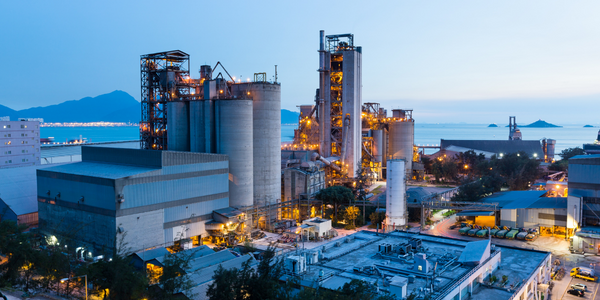
Case Study
Honeywell - Tata Chemicals Improves Data Accessibility with OneWireless
Tata was facing data accessibility challenges in the cement plant control room tapping signals from remote process control areas and other distant locations, including the gas scrubber. Tata needed a wireless solution to extend its control network securely to remote locations that would also provide seamless communication with existing control applications.
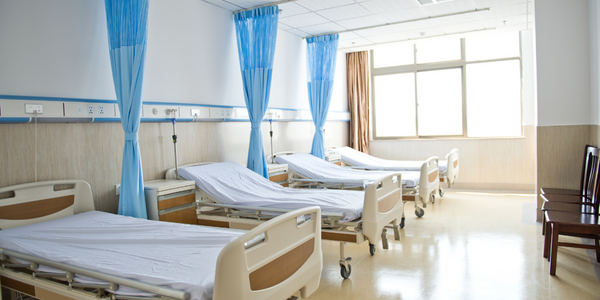
Case Study
Hospital Inventory Management
The hospital supply chain team is responsible for ensuring that the right medical supplies are readily available to clinicians when and where needed, and to do so in the most efficient manner possible. However, many of the systems and processes in use at the cancer center for supply chain management were not best suited to support these goals. Barcoding technology, a commonly used method for inventory management of medical supplies, is labor intensive, time consuming, does not provide real-time visibility into inventory levels and can be prone to error. Consequently, the lack of accurate and real-time visibility into inventory levels across multiple supply rooms in multiple hospital facilities creates additional inefficiency in the system causing over-ordering, hoarding, and wasted supplies. Other sources of waste and cost were also identified as candidates for improvement. Existing systems and processes did not provide adequate security for high-cost inventory within the hospital, which was another driver of cost. A lack of visibility into expiration dates for supplies resulted in supplies being wasted due to past expiry dates. Storage of supplies was also a key consideration given the location of the cancer center’s facilities in a dense urban setting, where space is always at a premium. In order to address the challenges outlined above, the hospital sought a solution that would provide real-time inventory information with high levels of accuracy, reduce the level of manual effort required and enable data driven decision making to ensure that the right supplies were readily available to clinicians in the right location at the right time.

Case Study
HEINEKEN Uses the Cloud to Reach 10.5 Million Consumers
For 2012 campaign, the Bond promotion, it planned to launch the campaign at the same time everywhere on the planet. That created unprecedented challenges for HEINEKEN—nowhere more so than in its technology operation. The primary digital content for the campaign was a 100-megabyte movie that had to play flawlessly for millions of viewers worldwide. After all, Bond never fails. No one was going to tolerate a technology failure that might bruise his brand.Previously, HEINEKEN had supported digital media at its outsourced datacenter. But that datacenter lacked the computing resources HEINEKEN needed, and building them—especially to support peak traffic that would total millions of simultaneous hits—would have been both time-consuming and expensive. Nor would it have provided the geographic reach that HEINEKEN needed to minimize latency worldwide.

Case Study
Advanced Elastomer Systems Upgrades Production
In order to maintain its share of the international market for thermoplastic elastomers AES recently expanded its Florida plant by adding a new production line. While the existing lines were operating satisfactorily using a PROVOX distributed control system with traditional analog I/O, AES wanted advanced technology on the new line for greater economy, efficiency, and reliability. AES officials were anxious to get this line into production to meet incoming orders, but two hurricanes slowed construction.
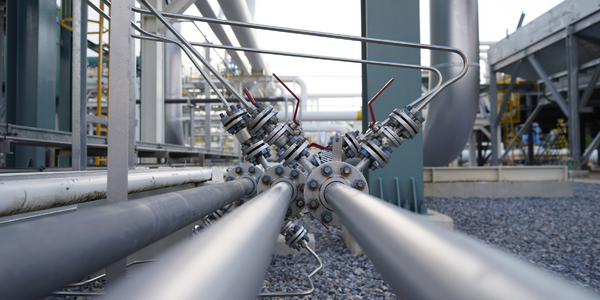
Case Study
Gas Pipeline Monitoring System for Hospitals
This system integrator focuses on providing centralized gas pipeline monitoring systems for hospitals. The service they provide makes it possible for hospitals to reduce both maintenance and labor costs. Since hospitals may not have an existing network suitable for this type of system, GPRS communication provides an easy and ready-to-use solution for remote, distributed monitoring systems System Requirements - GPRS communication - Seamless connection with SCADA software - Simple, front-end control capability - Expandable I/O channels - Combine AI, DI, and DO channels