15% Increase in Productivity for Nekkanti Sea Foods
公司规模
Large Corporate
地区
- Asia
国家
- India
产品
- Quixy
技术栈
- No-code platform
- WhatsApp integration
实施规模
- Enterprise-wide Deployment
影响指标
- Productivity Improvements
- Customer Satisfaction
- Digital Expertise
技术
- 平台即服务 (PaaS) - 应用开发平台
- 应用基础设施与中间件 - 数据交换与集成
适用行业
- 食品与饮料
适用功能
- 流程制造
- 质量保证
用例
- 过程控制与优化
- 库存管理
- 预测性维护
服务
- 系统集成
- 培训
关于客户
Nekkanti Sea Foods Limited (NSFL) is one of the largest exporters of seafood from India and has been in this business for over two decades. From a humble beginning in the seafood industry, the organization integrated backward by venturing into deep-sea trawling and processing seafood. In 1985, they started their operations by taking up a leased processing facility in Kakinada. Later in 1989, Nekkanti set up its processing facility in Visakhapatnam. They have since then never looked back.\n\nNekkanti has been exporting substantial quantities of Fresh Water Shrimps in various product forms, raw, cooked, and blanched, especially PD Tail-on & Off, Butterfly, Easy Peel, Head-on & Head Less in the block and IQF packs to various international markets for the last several years.
挑战
Processing and delivering safe and quality shrimp to its customers is the core focus at Nekkanti. The processing plants produce thousands of tonnes of processed shrimp annually for export in various value-added forms. Naturally, there were numerous workflows associated with the overall food processing and support processes. The organization was facing several challenges with these processes, which included:\n\nPaper-Based Data Processing: At each stage of seafood processing, data was recorded using paper-based forms. The manual recording system led to errors and discrepancies for both data related to the material being processed and the workforce involved in the processing. This form of data recording also led to issues for HR, as the workforce was divided across locations, type, efforts, shift process, etc. They had to depend on the paper-based effort tracker followed by the supervisor, which was quite tedious and time-taking.\n\nInformation Silos Proliferation: As the discrepancies and errors happened across various processing stages, it became challenging to pinpoint the root cause of the issue. During reconciliation, the company found discrepancies when comparing the raw material to the end product. Due to the silos, there was no single source of truth, and rectifying discrepancies became very difficult.\n\nIssues in Performance Measurement: Due to the obliteration of accurate and effective data, it was becoming quite challenging to manage resources effectively and measure the performance of the workforce involved and the various stages involved in the process. Even for quality control, the company had to rely on paper-based data for different processing stages such as grading, soaking, and freezing.
解决方案
Nekkanti identified and set up a core team of citizen developers composed of business users across the departments and trained them on the Quixy platform. The central IT team put together the necessary governance and monitoring structure to ensure that processes automated across different departments seamlessly integrated without any possibility for information silos and data redundancy. Business unit heads took over the ownership and accountability for the digitization efforts within their groups.\n\nThe core team established selection criteria for the high-impact processes to be automated and identified these processes for the first implementation phase. These included Inward Entry, Daily Quantity Reconciliation, Shift Output Reports, Facilitators Commission Processing, Payment Processing to name a few.\n\nAll the selected processes were automated and rolled out for the first processing center within six weeks, including requirements, design, implementation, and testing. The deployment for the remaining centers was thereafter completed within one week. Through this automation, key paper-based processes were eliminated. WhatsApp integration allowed prompt alerts and notifications for all key activities involved starting from the arrival of the raw material, weighment entry, daily quantity reconciliation, shift output report, attendance, payroll processing, to facilitators commission processing.
运营影响
数量效益
Case Study missing?
Start adding your own!
Register with your work email and create a new case study profile for your business.
相关案例.

Case Study
The Kellogg Company
Kellogg keeps a close eye on its trade spend, analyzing large volumes of data and running complex simulations to predict which promotional activities will be the most effective. Kellogg needed to decrease the trade spend but its traditional relational database on premises could not keep up with the pace of demand.

Case Study
HEINEKEN Uses the Cloud to Reach 10.5 Million Consumers
For 2012 campaign, the Bond promotion, it planned to launch the campaign at the same time everywhere on the planet. That created unprecedented challenges for HEINEKEN—nowhere more so than in its technology operation. The primary digital content for the campaign was a 100-megabyte movie that had to play flawlessly for millions of viewers worldwide. After all, Bond never fails. No one was going to tolerate a technology failure that might bruise his brand.Previously, HEINEKEN had supported digital media at its outsourced datacenter. But that datacenter lacked the computing resources HEINEKEN needed, and building them—especially to support peak traffic that would total millions of simultaneous hits—would have been both time-consuming and expensive. Nor would it have provided the geographic reach that HEINEKEN needed to minimize latency worldwide.

Case Study
Energy Management System at Sugar Industry
The company wanted to use the information from the system to claim under the renewable energy certificate scheme. The benefit to the company under the renewable energy certificates is Rs 75 million a year. To enable the above, an end-to-end solution for load monitoring, consumption monitoring, online data monitoring, automatic meter data acquisition which can be exported to SAP and other applications is required.

Case Study
Coca Cola Swaziland Conco Case Study
Coco Cola Swaziland, South Africa would like to find a solution that would enable the following results: - Reduce energy consumption by 20% in one year. - Formulate a series of strategic initiatives that would enlist the commitment of corporate management and create employee awareness while helping meet departmental targets and investing in tools that assist with energy management. - Formulate a series of tactical initiatives that would optimize energy usage on the shop floor. These would include charging forklifts and running cold rooms only during off-peak periods, running the dust extractors only during working hours and basing lights and air-conditioning on someone’s presence. - Increase visibility into the factory and other processes. - Enable limited, non-intrusive control functions for certain processes.

Case Study
Temperature Monitoring for Restaurant Food Storage
When it came to implementing a solution, Mr. Nesbitt had an idea of what functionality that he wanted. Although not mandated by Health Canada, Mr. Nesbitt wanted to ensure quality control issues met the highest possible standards as part of his commitment to top-of-class food services. This wish list included an easy-to use temperature-monitoring system that could provide a visible display of the temperatures of all of his refrigerators and freezers, including historical information so that he could review the performance of his equipment. It also had to provide alert notification (but email alerts and SMS text message alerts) to alert key staff in the event that a cooling system was exceeding pre-set warning limits.
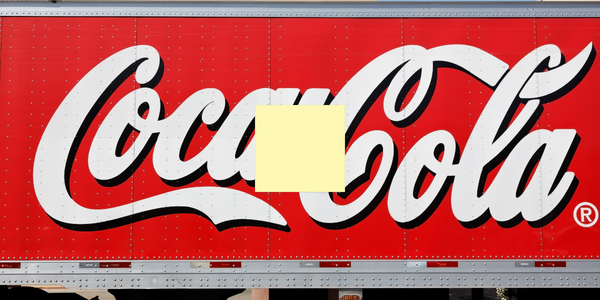
Case Study
Coca-Cola Refreshments, U.S.
Coca-Cola Refreshments owns and manages Coca-Cola branded refrigerators in retail establishments. Legacy systems were used to locate equipment information by logging onto multiple servers which took up to 8 hours to update information on 30-40 units. The company had no overall visibility into equipment status or maintenance history.