Lockheed Martin’s Flight to Perfect Quality: An iBASEt MES/Quality Customer Success Story
Customer Company Size
Large Corporate
Region
- America
Country
- United States
Product
- iBASEt Manufacturing Execution System (MES)
- iBASEt Quality Management System (EQMS)
- iBASEt Digital Operations Suite
Tech Stack
- Real-time Statistical Process Control (SPC)
- Six Sigma
- Root-Cause Analysis and Corrective Action procedures
Implementation Scale
- Enterprise-wide Deployment
Impact Metrics
- Customer Satisfaction
- Productivity Improvements
- Cost Savings
- Innovation Output
Technology Category
- Functional Applications - Manufacturing Execution Systems (MES)
- Functional Applications - Enterprise Resource Planning Systems (ERP)
- Analytics & Modeling - Predictive Analytics
Applicable Industries
- Aerospace
Applicable Functions
- Quality Assurance
Use Cases
- Predictive Maintenance
- Process Control & Optimization
Services
- System Integration
- Software Design & Engineering Services
- Training
About The Customer
Lockheed Martin’s Clearwater facility is part of the company’s Rotary and Mission Systems (RMS) division, headquartered in Bethesda, MD. The division’s products include aeronautics, space systems, information systems, global services, and electronic systems. The Clearwater plant employs over 400 people and works with more than 500 suppliers to produce a low-volume, high-mix of ruggedized, high-reliability electronic data and signal processing equipment. The facility supports over 460 programs for U.S. military and international customers, including the U.S. Navy, Air Force, Army, Marine Corps, Coast Guard, and the Department of Homeland Security.
The Challenge
Lockheed Martin’s Clearwater plant faced the challenge of maintaining high-quality standards while producing a low-volume, high-mix of ruggedized, high-reliability electronic data and signal processing equipment. The plant needed to comply with stringent specifications, regulatory requirements, and fluctuating schedules for over 30 different programs and more than 20 customers. The management team recognized the need for continuous improvement to stay competitive and achieve quality beyond market demands. A slowdown in demand during the 1990s prompted the management to focus on performance improvement, leading to the development of a culture of quality excellence and continuous improvement.
The Solution
Lockheed Martin’s Clearwater facility implemented iBASEt’s Manufacturing Execution System (MES) with an embedded Quality Management System (EQMS) to integrate production and quality assurance across operations. The MES collects data in real-time during inspection and test operations, immediately alerting on out-of-control conditions. The system also monitors metrics like defects per million opportunities (DPMO) and yield, which are used to establish process improvement goals. The MES facilitates a closed-loop system of continuous improvement by standardizing process improvements in manufacturing instructions. Additionally, the facility uses advanced technologies such as clean manufacturing cells, high-quality inspection systems, and automated solder robots to enhance quality control.
Operational Impact
Quantitative Benefit
Case Study missing?
Start adding your own!
Register with your work email and create a new case study profile for your business.
Related Case Studies.
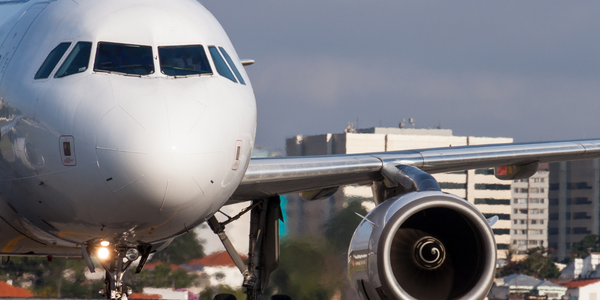
Case Study
Airbus Soars with Wearable Technology
Building an Airbus aircraft involves complex manufacturing processes consisting of thousands of moving parts. Speed and accuracy are critical to business and competitive advantage. Improvements in both would have high impact on Airbus’ bottom line. Airbus wanted to help operators reduce the complexity of assembling cabin seats and decrease the time required to complete this task.
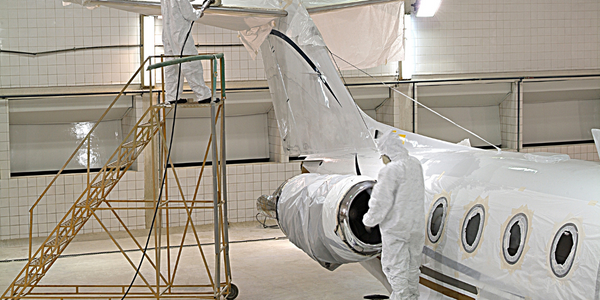
Case Study
Aircraft Predictive Maintenance and Workflow Optimization
First, aircraft manufacturer have trouble monitoring the health of aircraft systems with health prognostics and deliver predictive maintenance insights. Second, aircraft manufacturer wants a solution that can provide an in-context advisory and align job assignments to match technician experience and expertise.
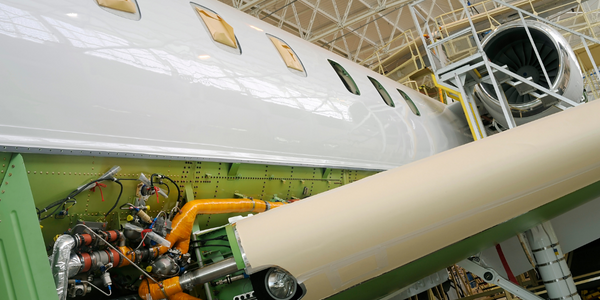
Case Study
Aerospace & Defense Case Study Airbus
For the development of its new wide-body aircraft, Airbus needed to ensure quality and consistency across all internal and external stakeholders. Airbus had many challenges including a very aggressive development schedule and the need to ramp up production quickly to satisfy their delivery commitments. The lack of communication extended design time and introduced errors that drove up costs.
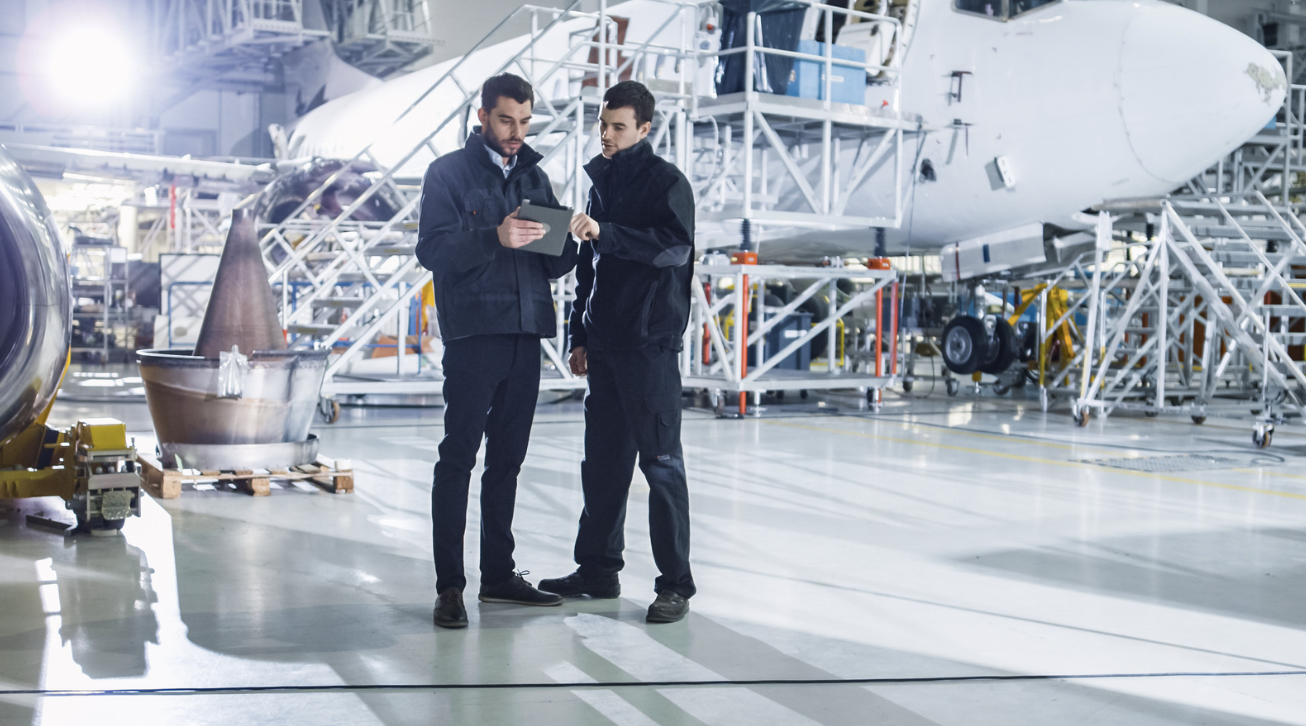
Case Study
Developing Smart Tools for the Airbus Factory
Manufacturing and assembly of aircraft, which involves tens of thousands of steps that must be followed by the operators, and a single mistake in the process could cost hundreds of thousands of dollars to fix, makes the room for error very small.
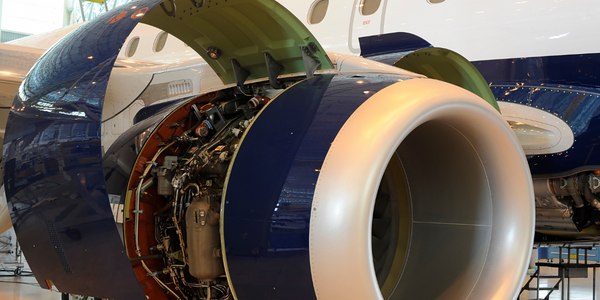
Case Study
Accelerate Production for Spirit AeroSystems
The manufacture and assembly of massive fuselage assemblies and other large structures generates a river of data. In fact, the bill of materials for a single fuselage alone can be millions of rows of data. In-house production processes and testing, as well as other manufacturers and customers created data flows that overwhelmed previous processes and information systems. Spirit’s customer base had grown substantially since their 2005 divestiture from Boeing, resulting in a $41 billion backlog of orders to fill. To address this backlog, meet increased customer demands and minimize additional capital investment, the company needed a way to improve throughput in the existing operational footprint. Spirit had a requirement from customers to increase fuselage production by 30%. To accomplish this goal, Spirit needed real-time information on its value chain and workflow. However, the two terabytes of data being pulled from their SAP ECC was unmanageable and overloaded their business warehouse. It had become time-consuming and difficult to pull aggregate data, disaggregate it for the needed information and then reassemble to create a report. During the 6-8 hours it took to build a report, another work shift (they run three per day) would have already taken place, thus the report content was out-of-date before it was ever delivered. As a result, supervisors often had to rely on manual efforts to provide charts, reports and analysis.