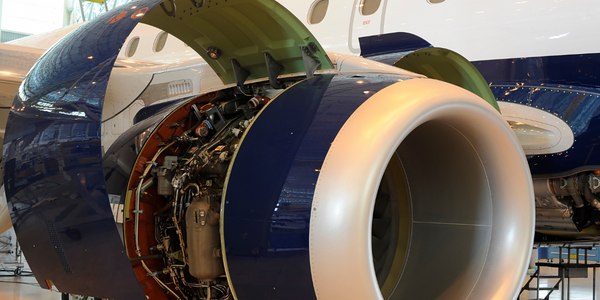
- Functional Applications - Enterprise Resource Planning Systems (ERP)
- Aerospace
- Discrete Manufacturing
- Factory Operations Visibility & Intelligence
The manufacture and assembly of massive fuselage assemblies and other large structures generates a river of data. In fact, the bill of materials for a single fuselage alone can be millions of rows of data. In-house production processes and testing, as well as other manufacturers and customers created data flows that overwhelmed previous processes and information systems. Spirit’s customer base had grown substantially since their 2005 divestiture from Boeing, resulting in a $41 billion backlog of orders to fill. To address this backlog, meet increased customer demands and minimize additional capital investment, the company needed a way to improve throughput in the existing operational footprint. Spirit had a requirement from customers to increase fuselage production by 30%. To accomplish this goal, Spirit needed real-time information on its value chain and workflow. However, the two terabytes of data being pulled from their SAP ECC was unmanageable and overloaded their business warehouse. It had become time-consuming and difficult to pull aggregate data, disaggregate it for the needed information and then reassemble to create a report. During the 6-8 hours it took to build a report, another work shift (they run three per day) would have already taken place, thus the report content was out-of-date before it was ever delivered. As a result, supervisors often had to rely on manual efforts to provide charts, reports and analysis.
That’s when Spirit’s Executive Leadership Team, and Vice President and Chief Information Officer Jim Cocca set an objective to “lean out” operations from a total-cost perspective and leverage IT solutions. The first step was implementing SAP HANA to address the data logjam, speeding up processes and enabling reporting at a more granular level—and with greater frequency. Before a full-scale implementation, Spirit first tested SAP HANA on its quarterly financial audit reports. Reports that had taken 37 hours to run now completed in only 14 seconds. Cocca then collaborated with Operations leaders to leverage this new technology to achieve their expanded production requirements. This led to the creation of the Fuselage Shop Floor Optimization initiative, which was designed to streamline capacity analysis, assembly operations and manufacturing planning. The initiative also sought to pinpoint sources of process delays using SAP HANA’s in-memory database and Business Objects analytics tools to create real-time production dashboards.
Case Study missing?
Start adding your own!
Register with your work email and create a new case study profile for your business.
Related Case Studies.
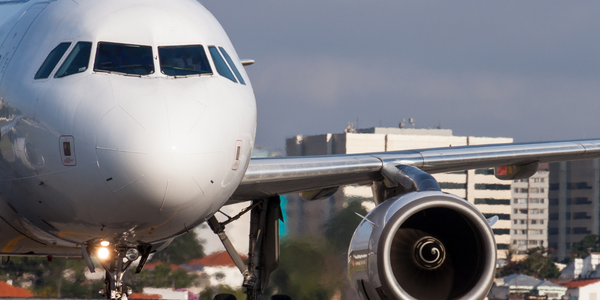
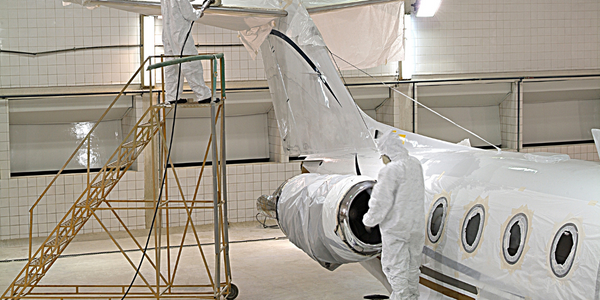
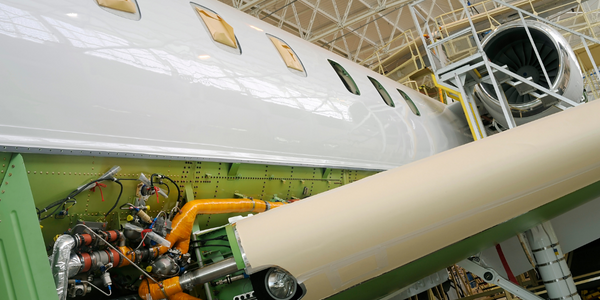
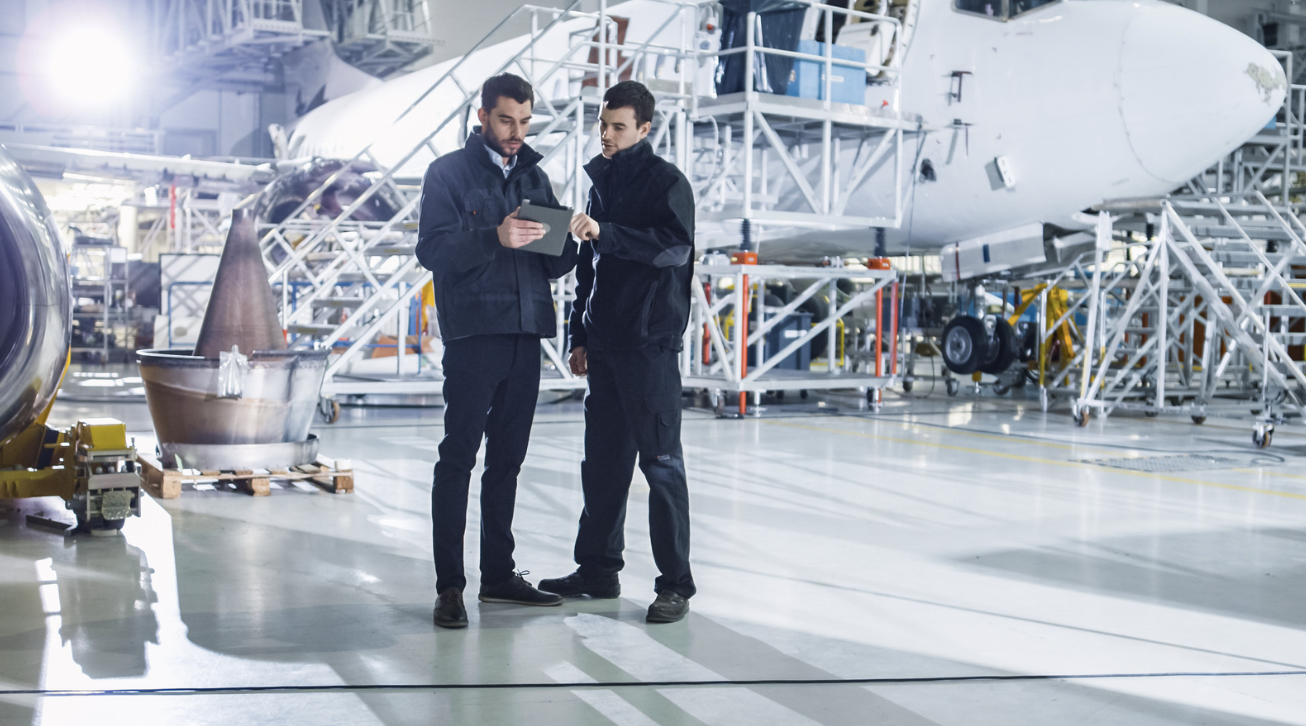
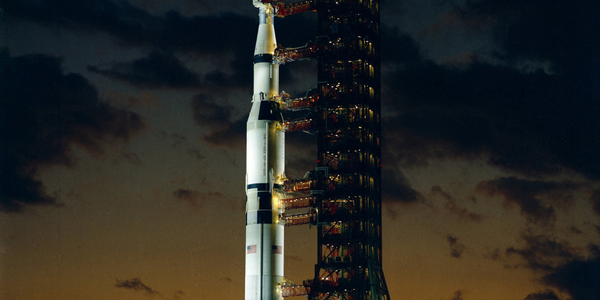