公司规模
Large Corporate
地区
- Africa
国家
- South Africa
产品
- Wonderware InTouch HMI
- Wonderware System Platform
- Wonderware MES Performance
- Wonderware Historian
技术栈
- Automation Software
- Real-time Database
- HMI Screens
实施规模
- Enterprise-wide Deployment
影响指标
- Productivity Improvements
- Cost Savings
技术
- 功能应用 - 远程监控系统
适用行业
- 食品与饮料
适用功能
- 离散制造
- 质量保证
用例
- 预测性维护
- 实时定位系统 (RTLS)
服务
- 系统集成
- 培训
关于客户
Amalgamated Beverage Industries is a division of South African Breweries (SAB), one of the largest brewing and bottling companies in the world. The company is based in Pretoria, South Africa. Amalgamated's main business goal was to accelerate production of its packaging line which included tracking machine performance parameters, reducing manual data capture, improving the accuracy of measurements and establishing reference points to better evaluate the reports from OEMs regarding performance of its machinery. Amalgamated’s machine OEM suppliers are responsible for managing the performance and commissioning of their equipment until final implementation of the manufacturing facility. Another important objective specified that the project was to serve as a ”proof of concept” for the effective implementation of PackML (Packaging Machinery Language) standards, which are an open system of guidelines used in the design of automation machinery.
挑战
Amalgamated Beverage Industries, a division of South African Breweries (SAB), was faced with the challenge of improving the overall production performance and accelerating the commissioning of a new packaging line to effectively address the annual summer demand for soft drinks. The facility needed to conform to Pack ML standards to ensure efficient operation of facility manufacturing equipment. The automation system had to work with existing SAP process order applications and daily production reporting facilities. The company wanted to capture all downtime data using the OMAC model of open control technologies for manufacturing applications. Another challenge was that the software project was being implemented at the same packaging line it was to monitor while it was being commissioned. During commissioning of a new factory line, all focus and effort is centered on this process. However, Amalgamated was challenged to implement both the hardware component and the software simultaneously.
解决方案
To successfully achieve the company’s objectives for leveraging existing SAP processes, conforming to the PackML standard and capturing downtime data, Amalgamated selected an Manufacturing Operations Management solution using Wonderware software. The company implemented Wonderware MES Performance, Wonderware System Platform, Wonderware InTouch HMI and Wonderware Historian. The combination of these powerful software tools enabled Amalgamated to achieve its objective of accelerating the production of its soft drink manufacturing line during peak demand cycles. The foundation of the Amalgamated system is the Wonderware MES Performance software built on the Wonderware System Platform. The performance software collects, tracks and communicates key performance indicators in real-time. This information is then delivered to operators who can take immediate action to correct a problem on the line. Built on Wonderware System Platform, the performance software is highly scalable for all SCADA, supervisory HMI and MES applications.
运营影响
Case Study missing?
Start adding your own!
Register with your work email and create a new case study profile for your business.
相关案例.

Case Study
The Kellogg Company
Kellogg keeps a close eye on its trade spend, analyzing large volumes of data and running complex simulations to predict which promotional activities will be the most effective. Kellogg needed to decrease the trade spend but its traditional relational database on premises could not keep up with the pace of demand.

Case Study
HEINEKEN Uses the Cloud to Reach 10.5 Million Consumers
For 2012 campaign, the Bond promotion, it planned to launch the campaign at the same time everywhere on the planet. That created unprecedented challenges for HEINEKEN—nowhere more so than in its technology operation. The primary digital content for the campaign was a 100-megabyte movie that had to play flawlessly for millions of viewers worldwide. After all, Bond never fails. No one was going to tolerate a technology failure that might bruise his brand.Previously, HEINEKEN had supported digital media at its outsourced datacenter. But that datacenter lacked the computing resources HEINEKEN needed, and building them—especially to support peak traffic that would total millions of simultaneous hits—would have been both time-consuming and expensive. Nor would it have provided the geographic reach that HEINEKEN needed to minimize latency worldwide.

Case Study
Energy Management System at Sugar Industry
The company wanted to use the information from the system to claim under the renewable energy certificate scheme. The benefit to the company under the renewable energy certificates is Rs 75 million a year. To enable the above, an end-to-end solution for load monitoring, consumption monitoring, online data monitoring, automatic meter data acquisition which can be exported to SAP and other applications is required.

Case Study
Coca Cola Swaziland Conco Case Study
Coco Cola Swaziland, South Africa would like to find a solution that would enable the following results: - Reduce energy consumption by 20% in one year. - Formulate a series of strategic initiatives that would enlist the commitment of corporate management and create employee awareness while helping meet departmental targets and investing in tools that assist with energy management. - Formulate a series of tactical initiatives that would optimize energy usage on the shop floor. These would include charging forklifts and running cold rooms only during off-peak periods, running the dust extractors only during working hours and basing lights and air-conditioning on someone’s presence. - Increase visibility into the factory and other processes. - Enable limited, non-intrusive control functions for certain processes.

Case Study
Temperature Monitoring for Restaurant Food Storage
When it came to implementing a solution, Mr. Nesbitt had an idea of what functionality that he wanted. Although not mandated by Health Canada, Mr. Nesbitt wanted to ensure quality control issues met the highest possible standards as part of his commitment to top-of-class food services. This wish list included an easy-to use temperature-monitoring system that could provide a visible display of the temperatures of all of his refrigerators and freezers, including historical information so that he could review the performance of his equipment. It also had to provide alert notification (but email alerts and SMS text message alerts) to alert key staff in the event that a cooling system was exceeding pre-set warning limits.
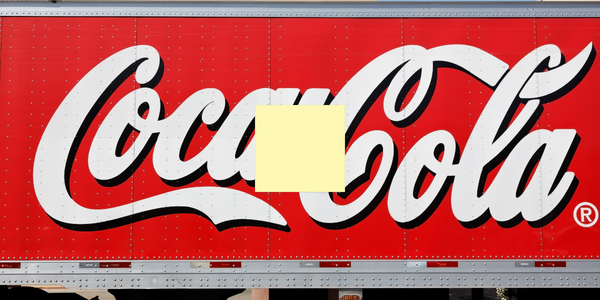
Case Study
Coca-Cola Refreshments, U.S.
Coca-Cola Refreshments owns and manages Coca-Cola branded refrigerators in retail establishments. Legacy systems were used to locate equipment information by logging onto multiple servers which took up to 8 hours to update information on 30-40 units. The company had no overall visibility into equipment status or maintenance history.