Westfalia AS/RS installed at Hershey Creamery Company
公司规模
Large Corporate
地区
- America
国家
- United States
产品
- Savanna.NET WMS
- Westfalia Satellite®
- Right Angle Transfer (RAT) conveyor
技术栈
- Warehouse Management Software (WMS)
- Automated Storage and Retrieval System (AS/RS)
- Pick-to-light system
实施规模
- Enterprise-wide Deployment
影响指标
- Productivity Improvements
- Cost Savings
- Employee Satisfaction
技术
- 功能应用 - 仓库管理系统 (WMS)
- 自动化与控制 - 自动化与过程控制系统
- 网络与连接 - 射频识别
适用行业
- 食品与饮料
- 零售
适用功能
- 仓库和库存管理
- 物流运输
用例
- 仓库自动化
- 库存管理
- 预测性维护
服务
- 系统集成
- 软件设计与工程服务
关于客户
Since 1894, family founded and owned Hershey Creamery Company has specialized in bulk ice cream novelties. The company distributes to more than 22,000 retail outlets such as grocery and convenience stores, but focuses mainly on direct-store delivery. In 1997, in order to optimize material flow, reduce logistics costs and labor requirements, Hershey Creamery sought Westfalia Technologies, Inc. to design and build a warehousing system for their new ice cream distribution center located in Middletown, PA. The distribution center was needed to handle the volume of smaller direct-store deliveries and larger orders for Hershey’s regional warehouses, while maintaining selectivity for numerous stock keeping units.
挑战
Westfalia initially designed and built a 5,000 pallet position, eight storage level automated warehouse system incorporating pick tunnel operations. The 2 aisle system has a combination of seven- and five-deep storage lanes. Each aisle contains one S/RM capable of handling approximately 70 pallets per hour. All pallets are triple supported within the rack structure, thus eliminating pallet damage.\n\nAbout 5 years later, due to their growing demand, the system was expanded—aisle lengths were increased 50% and a 3rd level of pick lanes were added within the rack structure. At that time Westfalia’s Warehouse Management Software (WMS), Savanna.NET was installed too. With these additions Hershey Creamery has been able to deliver its products faster and more efficiently with higher throughput capabilities. Parameters were established for Westfalia’s AS/RS design, including the fact FIFO inventory management must be maintained. One SKU is stored in each storage lane, and the fastest moving SKU’s are placed in storage lanes as close to the input / output conveyors as possible. By storing the pallets in two different lane depths, the warehouse is able to meet the throughputs of the fast moving “A” products in the longer lanes, and the slower moving “B” products in the shorter lanes. This mix of lane depth increases rack utilization. Hershey Creamery’s picking operations require both full pallet and case picking.
解决方案
After pallets have a print & apply label attached to their side, they enter the automated system from forklift trucks via a Right Angle Transfer (RAT) conveyor. Each pallet—Hershey uses two types GMA and a smaller one—is conveyed to a squaring station where it is centered on the conveyor, profile-checked, and scanned for identification. At the profile check, the sensors detect if the height, shape or weight of the pallet fits the unit load envelope. If a pallet fails the profiles check, it is rejected and moved to the reject lane. Rejected pallets stay in this palletizing area for correction by an operator.\n\nApproved pallets are then assigned a storage position by the Warehouse Management System (WMS) and conveyed to the infeed of either S/RM, in either aisle. Westfalia’s Satellite® rack entry vehicle smoothly and quickly places the pallet off the S/RM and in the storage lane where it belongs. The -40F degree deep-freeze environment hardens the ice cream for 24 hours before shipping. All pallets are tracked throughout the system by Westfalia’s WMS. When selected for shipping, it directs the movement of the pallet either into the pick tunnel or the shipping dock via the Satellite® and S/RM, and onto conveyors. Order selection is performed outside the control of the WMS. Cases of ice cream novelties are order-picked within the rack’s second and third levels. Using a pick-to-light system employees pick the number of cases required and place them onto a belt conveyor, leading down to the palletizing area for outbound shipping.
运营影响
数量效益
Case Study missing?
Start adding your own!
Register with your work email and create a new case study profile for your business.
相关案例.

Case Study
The Kellogg Company
Kellogg keeps a close eye on its trade spend, analyzing large volumes of data and running complex simulations to predict which promotional activities will be the most effective. Kellogg needed to decrease the trade spend but its traditional relational database on premises could not keep up with the pace of demand.

Case Study
HEINEKEN Uses the Cloud to Reach 10.5 Million Consumers
For 2012 campaign, the Bond promotion, it planned to launch the campaign at the same time everywhere on the planet. That created unprecedented challenges for HEINEKEN—nowhere more so than in its technology operation. The primary digital content for the campaign was a 100-megabyte movie that had to play flawlessly for millions of viewers worldwide. After all, Bond never fails. No one was going to tolerate a technology failure that might bruise his brand.Previously, HEINEKEN had supported digital media at its outsourced datacenter. But that datacenter lacked the computing resources HEINEKEN needed, and building them—especially to support peak traffic that would total millions of simultaneous hits—would have been both time-consuming and expensive. Nor would it have provided the geographic reach that HEINEKEN needed to minimize latency worldwide.
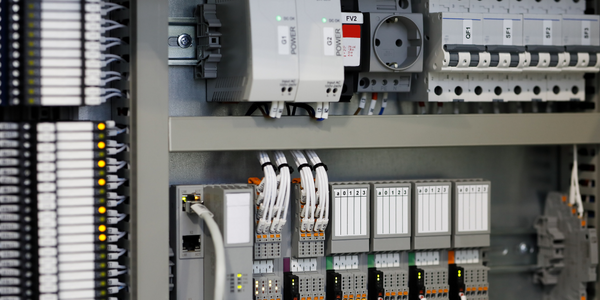
Case Study
Improving Production Line Efficiency with Ethernet Micro RTU Controller
Moxa was asked to provide a connectivity solution for one of the world's leading cosmetics companies. This multinational corporation, with retail presence in 130 countries, 23 global braches, and over 66,000 employees, sought to improve the efficiency of their production process by migrating from manual monitoring to an automatic productivity monitoring system. The production line was being monitored by ABB Real-TPI, a factory information system that offers data collection and analysis to improve plant efficiency. Due to software limitations, the customer needed an OPC server and a corresponding I/O solution to collect data from additional sensor devices for the Real-TPI system. The goal is to enable the factory information system to more thoroughly collect data from every corner of the production line. This will improve its ability to measure Overall Equipment Effectiveness (OEE) and translate into increased production efficiencies. System Requirements • Instant status updates while still consuming minimal bandwidth to relieve strain on limited factory networks • Interoperable with ABB Real-TPI • Small form factor appropriate for deployment where space is scarce • Remote software management and configuration to simplify operations

Case Study
Energy Management System at Sugar Industry
The company wanted to use the information from the system to claim under the renewable energy certificate scheme. The benefit to the company under the renewable energy certificates is Rs 75 million a year. To enable the above, an end-to-end solution for load monitoring, consumption monitoring, online data monitoring, automatic meter data acquisition which can be exported to SAP and other applications is required.
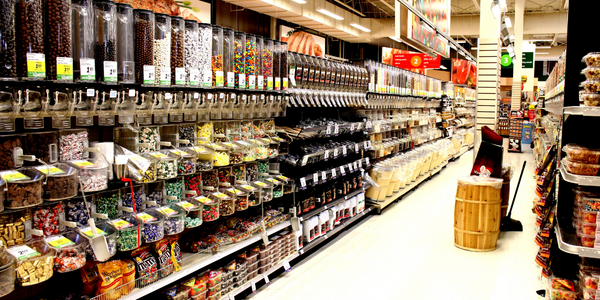
Case Study
How Sirqul’s IoT Platform is Crafting Carrefour’s New In-Store Experiences
Carrefour Taiwan’s goal is to be completely digital by end of 2018. Out-dated manual methods for analysis and assumptions limited Carrefour’s ability to change the customer experience and were void of real-time decision-making capabilities. Rather than relying solely on sales data, assumptions, and disparate systems, Carrefour Taiwan’s CEO led an initiative to find a connected IoT solution that could give the team the ability to make real-time changes and more informed decisions. Prior to implementing, Carrefour struggled to address their conversion rates and did not have the proper insights into the customer decision-making process nor how to make an immediate impact without losing customer confidence.