Volvo Sees Significant Cost Savings and Visibility with e2open®
公司规模
1,000+
地区
- America
- Asia
- Europe
国家
- Belgium
- China
- Sweden
- United States
产品
- e2open Transportation Management
技术栈
- Cloud-based Architecture
- SaaS Model
- EDI Integration
实施规模
- Enterprise-wide Deployment
影响指标
- Cost Savings
- Customer Satisfaction
- Productivity Improvements
技术
- 功能应用 - 运输管理系统 (TMS)
- 平台即服务 (PaaS) - 连接平台
适用行业
- 汽车
适用功能
- 物流运输
用例
- 车队管理
- 供应链可见性(SCV)
- 资产跟踪
服务
- 云规划/设计/实施服务
- 系统集成
关于客户
Headquartered in Göteborg, Sweden, and under the ownership of the Zhejiang Geely Holding (Geely Holding) of China since 2010, Volvo Cars is one of the most respected car brands in the world. The company was founded in 1927 and has approximately 29,000 employees worldwide. In 2015, Volvo sold more than half a million vehicles in 100 different countries.
挑战
Volvo needed to improve visibility and business efficiencies across global operations. The company looked to design and deploy a new transportation management system (TMS) that could serve as the backbone of its vehicle distribution network by planning, optimizing, and tracking shipments of all finished vehicles from its four global factories to 2,300 dealerships worldwide. Volvo recently expanded its footprint to include a new factory in the U.S., which will also use the technology, including rail capabilities. Volvo established a list of goals for a TMS: bring consistency and efficiency to time-consuming, costly business processes, increase visibility across global operations, and improve agility and the ability to respond quickly to changing business dynamics.
解决方案
Volvo approached eight companies seeking a sophisticated global TMS that could be ready to go in 150 days. After a competitive RFP process, Volvo chose e2open to tackle the challenge of setting up a TMS that could integrate with 26 existing IT systems and handle 35,000 routes to market, 120 new EDI messages, and 30 existing carriers. The cloud-based architecture of e2open Transportation Management allowed Volvo to meet its aggressive timeline and have a new TMS fully deployed within five months without experiencing any disruption to its supply chain. With a traditional system, months would need to be spent just on discussing the architectural guidelines. Most of those types of challenges during a new software implementation are covered by the SaaS model. No other system could have gone live in less than five months.
运营影响
数量效益
Case Study missing?
Start adding your own!
Register with your work email and create a new case study profile for your business.
相关案例.
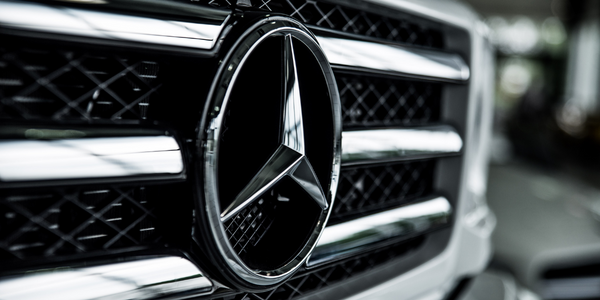
Case Study
Integral Plant Maintenance
Mercedes-Benz and his partner GAZ chose Siemens to be its maintenance partner at a new engine plant in Yaroslavl, Russia. The new plant offers a capacity to manufacture diesel engines for the Russian market, for locally produced Sprinter Classic. In addition to engines for the local market, the Yaroslavl plant will also produce spare parts. Mercedes-Benz Russia and his partner needed a service partner in order to ensure the operation of these lines in a maintenance partnership arrangement. The challenges included coordinating the entire maintenance management operation, in particular inspections, corrective and predictive maintenance activities, and the optimizing spare parts management. Siemens developed a customized maintenance solution that includes all electronic and mechanical maintenance activities (Integral Plant Maintenance).
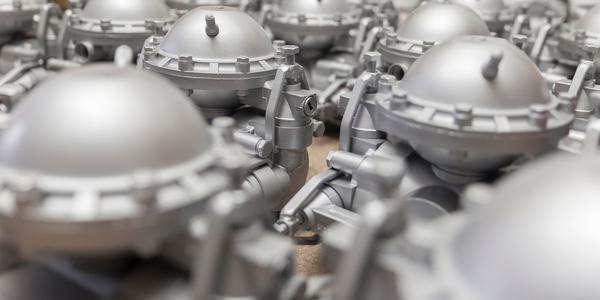
Case Study
Monitoring of Pressure Pumps in Automotive Industry
A large German/American producer of auto parts uses high-pressure pumps to deburr machined parts as a part of its production and quality check process. They decided to monitor these pumps to make sure they work properly and that they can see any indications leading to a potential failure before it affects their process.