公司规模
Large Corporate
地区
- Europe
国家
- Germany
产品
- Mirantis OpenStack Cloud
- Intel x86 based servers
- Cloud Foundry open source PaaS
技术栈
- OpenStack
- Cloud Foundry
- Intel x86
实施规模
- Enterprise-wide Deployment
影响指标
- Cost Savings
- Productivity Improvements
- Innovation Output
技术
- 基础设施即服务 (IaaS) - 云计算
- 平台即服务 (PaaS) - 应用开发平台
适用行业
- 汽车
适用功能
- 离散制造
- 产品研发
用例
- 预测性维护
- 自动化制造系统
服务
- 云规划/设计/实施服务
- 系统集成
关于客户
Volkswagen Group is a global leader in manufacturing and innovation. The German company’s brands are sold in 153 countries and include Audi, Bentley, Bugatti, Ducati and many more. In 2015, the Volkswagen Group spent over €11.8 billion in R&D and its €213.3 billion in revenue also included trucks, testing systems, financing, leasing, and fleet management. Volkswagen Group was founded in 1937 to produce what would become a consumer icon, the Beetle, and has transformed the industry ever since. Today, its 610,000 employees across the globe are addressing new market disruptors with the same diligence and innovation; in energy efficiency, autonomous driving, and the connected car.
挑战
Volkswagen Group, the world’s second largest automaker, was facing a challenge with its IT environment which had become decentralized and heterogonous due to its recent growth. Brands, divisions, and advanced initiatives operate on different IT platforms which requires costly investment in hundreds of technologies and development tools. The company's heterogeneous IT platforms included specialized hardware, often with long procurement cycles, and required significant manual work to provision new resources. Furthermore, expensive storage solutions were being consumed by applications that doubled in their capacity requirements every two years. The company needed to unify and automate work streams and platforms across the entire Volkswagen Group. New standardized infrastructure would need to replace existing developer systems yet still connect to legacy applications that maintain important data.
解决方案
Volkswagen Group selected OpenStack as their global, standardized IT platform and next generation cloud – the Group IT Cloud. The company evaluated companies that distributed and supported OpenStack software and narrowed the field to two. Group IT then brought Mirantis and one other vendor to their headquarters where the companies demonstrated the capabilities of their respective OpenStack distributions across 64 different use cases. Mirantis OpenStack emerged on top with an execution rate of 98 percent and proved to be the most stable and fastest to implement. In October 2015, Volkswagen began its implementation of Mirantis OpenStack as its standardized cloud platform for all brands and divisions; from global corporate initiatives to emerging research labs in Beijing, Berlin, and San Francisco that embody the startup culture. The new cloud would reach employees, suppliers, dealers, and customers.
运营影响
数量效益
Case Study missing?
Start adding your own!
Register with your work email and create a new case study profile for your business.
相关案例.
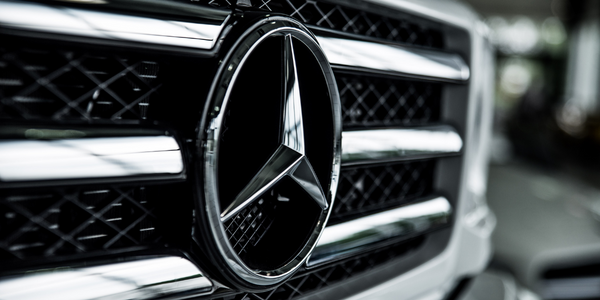
Case Study
Integral Plant Maintenance
Mercedes-Benz and his partner GAZ chose Siemens to be its maintenance partner at a new engine plant in Yaroslavl, Russia. The new plant offers a capacity to manufacture diesel engines for the Russian market, for locally produced Sprinter Classic. In addition to engines for the local market, the Yaroslavl plant will also produce spare parts. Mercedes-Benz Russia and his partner needed a service partner in order to ensure the operation of these lines in a maintenance partnership arrangement. The challenges included coordinating the entire maintenance management operation, in particular inspections, corrective and predictive maintenance activities, and the optimizing spare parts management. Siemens developed a customized maintenance solution that includes all electronic and mechanical maintenance activities (Integral Plant Maintenance).
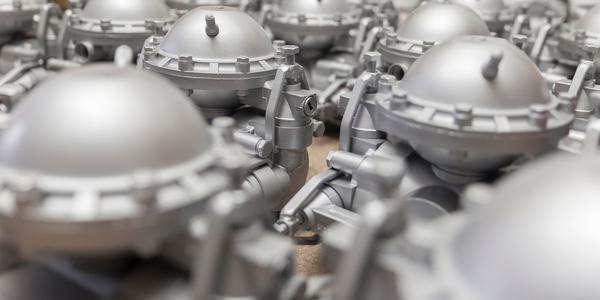
Case Study
Monitoring of Pressure Pumps in Automotive Industry
A large German/American producer of auto parts uses high-pressure pumps to deburr machined parts as a part of its production and quality check process. They decided to monitor these pumps to make sure they work properly and that they can see any indications leading to a potential failure before it affects their process.