Virgin Orbit Takes Off on Production: An iBASEt MES/Quality Customer Success Story
公司规模
Large Corporate
地区
- America
国家
- United States
产品
- Solumina
- LauncherOne
- Cosmic Girl
技术栈
- Oracle ERP
- Teamcenter PLM
实施规模
- Enterprise-wide Deployment
影响指标
- Productivity Improvements
- Digital Expertise
- Customer Satisfaction
技术
- 功能应用 - 制造执行系统 (MES)
- 功能应用 - 产品生命周期管理系统 (PLM)
- 功能应用 - 企业资源规划系统 (ERP)
适用行业
- 航天
适用功能
- 离散制造
- 质量保证
- 商业运营
用例
- 自动化制造系统
- 过程控制与优化
- 数字线程
- 远程控制
服务
- 系统集成
- 培训
- 软件设计与工程服务
关于客户
Virgin Galactic may be the best known of the Virgin Group’s aerospace ventures, having captured the imagination of both the public and media for its development of commercial spacecraft, particularly its goal of providing suborbital spaceflights to tourists. For the business world, what may be the most interesting part of the Virgin Group portfolio of companies may be the newest: Virgin Orbit, a Long Beach, California-based organization focused on launching satellites for commercial, research, and governmental projects. In a recent issue of The Verge, Dan Hart, CEO of Virgin Orbit, stated, “To me, the Virgin brand is about making life on Earth better, and we are going to fulfill that purpose by accessing Low Earth Orbit to connect billions of people and enabling valuable applications of data from space through Virgin Orbit’s flexible, affordable, and reliable launch service.” The first iteration of this vision is Virgin Orbit’s LauncherOne program, an initiative that will launch small satellites from under the wing of a 747 airplane. The program is comprised of two vehicles: The LauncherOne rocket and The Cosmic Girl 747-400 plane.
挑战
The challenges of a discrete complex manufacturing operation like the one at Virgin Orbit are significant. The processing of engineer to order, and multiple bill-of-material levels can go very deep. Work-in-process units incorporate engineering changes as the process progresses, and engineering must be involved in material review processes, dispositions, and rework instructions every step of the way. As-designed equals as-built validation is required, as is traceability of changes, deviations, and approvals. It’s a complicated business that requires a complete solution. The LauncherOne team at Virgin Orbit selected iBASEt’s MES Solution, powered by Solumina, to address a host of needs, including: Paperless work instructions, Real-time visibility, Synchronization and control of production operations, Quality management and corrective actions, Shop floor change management, Data collection, buy off, and certifications, Execution of real-time, physical processes, Work order completion management, Integration, coordination, and execution of work orders with Virgin Orbit’s ERP (Oracle) and PLM (Teamcenter) systems.
解决方案
To achieve these objectives, iBASEt’s MES Solution was deployed, including Process Planning, Shop Floor Execution, and Shop Floor Quality functionality were deployed with no configurations. “We had been working in a paper-based environment that was both labor- and time-intensive,” says Darren Buonaguidi, project manager for the LauncherOne team. “A technician on the shop floor would have to read the work instructions, and often supplemental information, and then go to different places on the floor to get everything they needed. There were usually many steps, involved; often the accessed information was in Excel spreadsheets or other paper forms. Solumina provides the work instructions in one place, an easy-to-access and understand screen. Then it not only collects and presents all the relevant information, but automatically incorporates engineering changes and manages exceptions. In a complex environment like ours, the speed of reaction to exceptions is critical; Solumina enables quick response.” To speed understanding and adoption of this solution, iBASEt gave targeted implementation workshops to LauncherOne’s core implementation team on each of the functional areas that included the basics of each area with best practices coaching, as well as a framework for business process transformation and execution/utilization for LauncherOne manufacturing. “This knowledge was passed on very successfully to the team at large,” reports Andrzej Goryca, enterprise application manager at Virgin Orbit. “Communication with the entire team was essential to the ramp up, as was making sure everyone knew they were an important part of the team. The commitment we had from our top-level leadership also helped us get up to speed fast.” Buonaguidi adds that the application itself helps with training the staff. “Solumina is well thought out, so when team members have questions, the answers are at hand in the OOB Solumina,” he says. “Its capabilities are really complete.” Virgin Orbit team has done a great job managing business requirements and asking the “why” question each time a customization was being requested.
运营影响
数量效益
Case Study missing?
Start adding your own!
Register with your work email and create a new case study profile for your business.
相关案例.
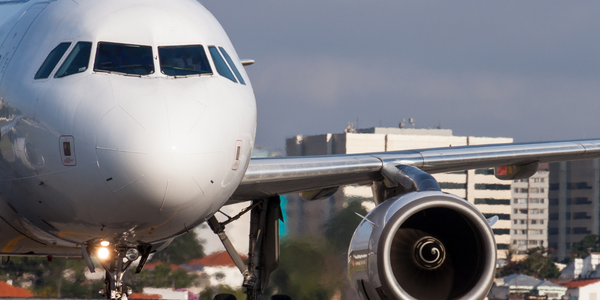
Case Study
Airbus Soars with Wearable Technology
Building an Airbus aircraft involves complex manufacturing processes consisting of thousands of moving parts. Speed and accuracy are critical to business and competitive advantage. Improvements in both would have high impact on Airbus’ bottom line. Airbus wanted to help operators reduce the complexity of assembling cabin seats and decrease the time required to complete this task.
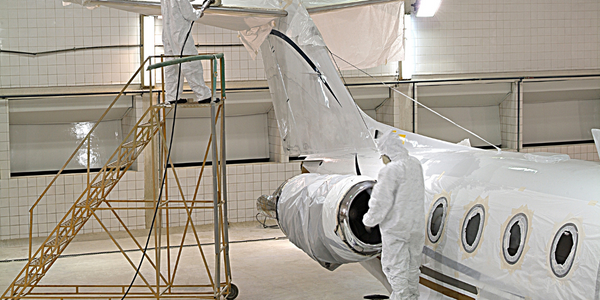
Case Study
Aircraft Predictive Maintenance and Workflow Optimization
First, aircraft manufacturer have trouble monitoring the health of aircraft systems with health prognostics and deliver predictive maintenance insights. Second, aircraft manufacturer wants a solution that can provide an in-context advisory and align job assignments to match technician experience and expertise.
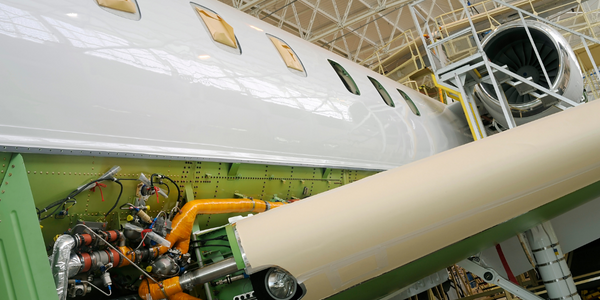
Case Study
Aerospace & Defense Case Study Airbus
For the development of its new wide-body aircraft, Airbus needed to ensure quality and consistency across all internal and external stakeholders. Airbus had many challenges including a very aggressive development schedule and the need to ramp up production quickly to satisfy their delivery commitments. The lack of communication extended design time and introduced errors that drove up costs.
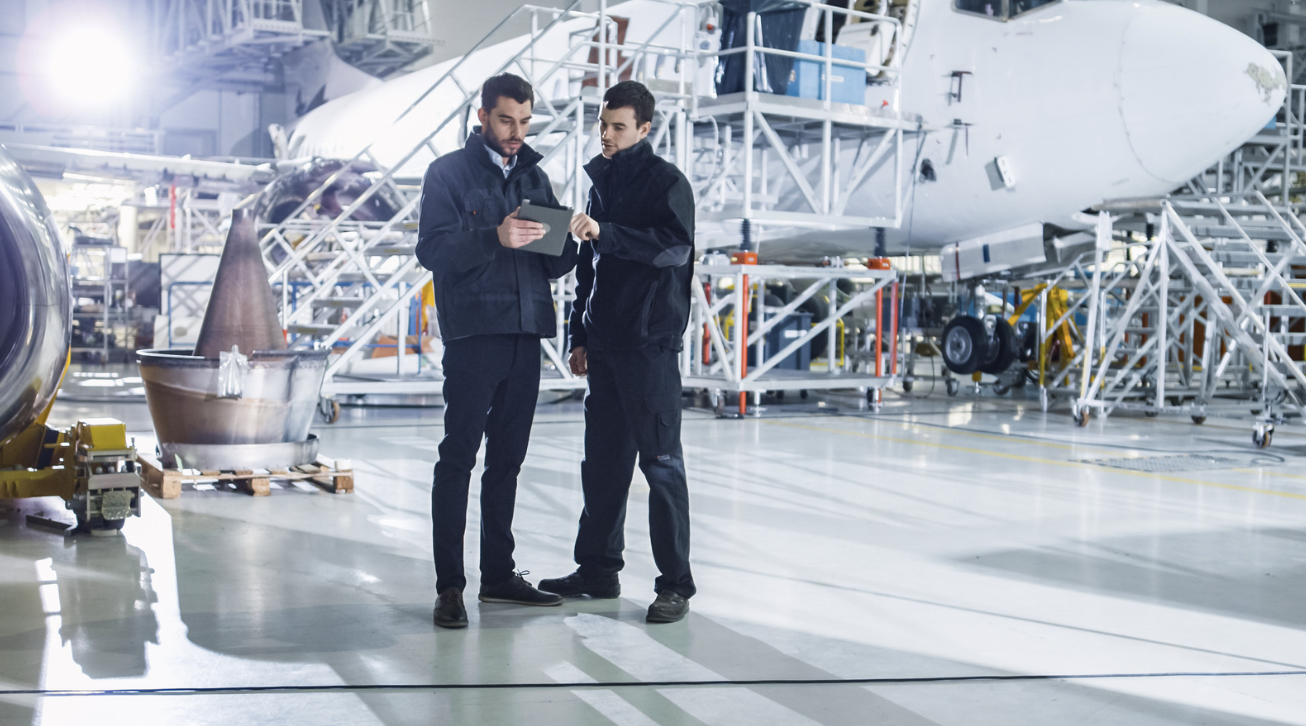
Case Study
Developing Smart Tools for the Airbus Factory
Manufacturing and assembly of aircraft, which involves tens of thousands of steps that must be followed by the operators, and a single mistake in the process could cost hundreds of thousands of dollars to fix, makes the room for error very small.
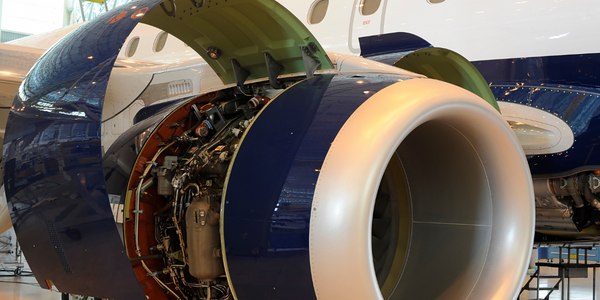
Case Study
Accelerate Production for Spirit AeroSystems
The manufacture and assembly of massive fuselage assemblies and other large structures generates a river of data. In fact, the bill of materials for a single fuselage alone can be millions of rows of data. In-house production processes and testing, as well as other manufacturers and customers created data flows that overwhelmed previous processes and information systems. Spirit’s customer base had grown substantially since their 2005 divestiture from Boeing, resulting in a $41 billion backlog of orders to fill. To address this backlog, meet increased customer demands and minimize additional capital investment, the company needed a way to improve throughput in the existing operational footprint. Spirit had a requirement from customers to increase fuselage production by 30%. To accomplish this goal, Spirit needed real-time information on its value chain and workflow. However, the two terabytes of data being pulled from their SAP ECC was unmanageable and overloaded their business warehouse. It had become time-consuming and difficult to pull aggregate data, disaggregate it for the needed information and then reassemble to create a report. During the 6-8 hours it took to build a report, another work shift (they run three per day) would have already taken place, thus the report content was out-of-date before it was ever delivered. As a result, supervisors often had to rely on manual efforts to provide charts, reports and analysis.