Toyota Boshoku America uses Lectra’s VectorAuto automated cutter to accelerate prototyping and increase cutting accuracy

公司规模
Large Corporate
地区
- America
国家
- United States
产品
- VectorAutoFX
- Formaris
- Diamino TechTex
技术栈
- Automated Cutting Systems
- Patternmaking Software
- CAD Systems
实施规模
- Enterprise-wide Deployment
影响指标
- Productivity Improvements
- Customer Satisfaction
- Innovation Output
技术
- 功能应用 - 产品生命周期管理系统 (PLM)
- 功能应用 - 制造执行系统 (MES)
适用行业
- 汽车
适用功能
- 产品研发
- 质量保证
用例
- 预测性维护
- 工厂可见化与智能化
- 自动化制造系统
服务
- 系统集成
- 软件设计与工程服务
关于客户
Toyota Boshoku America is a leading supplier of automotive interior systems and filters. The company produces complete systems that include seats, door trim, ceiling material, and carpeting. The Toyota Boshoku America Research & Development facility in Novi, Michigan develops prototypes for selected Toyota and General Motors vehicles. The company is part of the global Toyota Boshoku Corporation, which is known for its commitment to quality and innovation in the automotive industry. With a focus on developing advanced interior systems, Toyota Boshoku America plays a crucial role in enhancing the comfort, safety, and aesthetics of modern vehicles. The company collaborates closely with major automotive manufacturers to meet the evolving demands of the market, ensuring that their products are at the forefront of technological advancements and design trends.
挑战
As manufacturers seek to meet customers’ demands for quiet, comfortable, stylish interiors, seat systems have become complex and more difficult to manufacture. New features such as adjustable bottom seat cushions, occupant detection systems, seat heating and cooling systems, and advanced entertainment systems are now built into seats. Side-impact air bags are also packaged inside seats, and they must be able to burst through the seat’s trim cover seams at precisely the right time. Product development schedules have also shortened—the time between initial concept and prototype is now approximately four weeks, or about half of what it was just a few years ago. In the past, Toyota Boshoku America engineers developed prototypes by digitizing foam seat shapes and developing patterns, which were then hand-cut from leather, vinyl, or other materials. This approach was time consuming and lacked the accuracy required to meet the automotive industry’s stringent tolerances. Cutting a single trim cover could take two to three hours. As Toyota Boshoku America seeks to continuously improve its development processes, it looked for a cutting solution that would enable engineers to accelerate prototyping and ensure that the patterns developed would work the same in production as they did in prototyping.
解决方案
Toyota Boshoku America chose Lectra’s new-generation VectorAutoFX automated cutter to address their prototyping challenges. The decision was based on their previous positive experience with Lectra cutters. The VectorAutoFX delivers the best accuracy on the market, which is crucial for meeting the stringent tolerances required in the automotive industry. During its prototyping process, Toyota Boshoku America uses Lectra’s Formaris® patternmaking software for digitizing and defining pattern pieces. The model is imported into Lectra’s Diamino® TechTex application, where markers are created and nested. Markers are sent directly to the VectorAuto automated cutting system for optimal material usage and high productivity. The VectorAutoFX cutter allows Toyota Boshoku America to perform tight radius cuts with a smooth, continuous radius, instead of the jagged cuts seen with knife cutters. This results in parts that are well within tolerances and fit better to seat shapes. The improved cutting accuracy reduces the number of design changes required at the production facility due to cutting errors or production difficulties. Production teams can now evaluate trim cover designs during prototyping and know that the parts will be identical in production.
运营影响
数量效益
Case Study missing?
Start adding your own!
Register with your work email and create a new case study profile for your business.
相关案例.
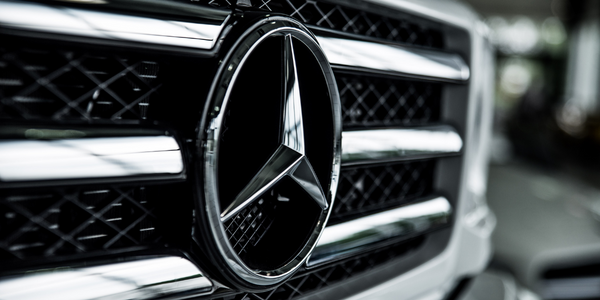
Case Study
Integral Plant Maintenance
Mercedes-Benz and his partner GAZ chose Siemens to be its maintenance partner at a new engine plant in Yaroslavl, Russia. The new plant offers a capacity to manufacture diesel engines for the Russian market, for locally produced Sprinter Classic. In addition to engines for the local market, the Yaroslavl plant will also produce spare parts. Mercedes-Benz Russia and his partner needed a service partner in order to ensure the operation of these lines in a maintenance partnership arrangement. The challenges included coordinating the entire maintenance management operation, in particular inspections, corrective and predictive maintenance activities, and the optimizing spare parts management. Siemens developed a customized maintenance solution that includes all electronic and mechanical maintenance activities (Integral Plant Maintenance).
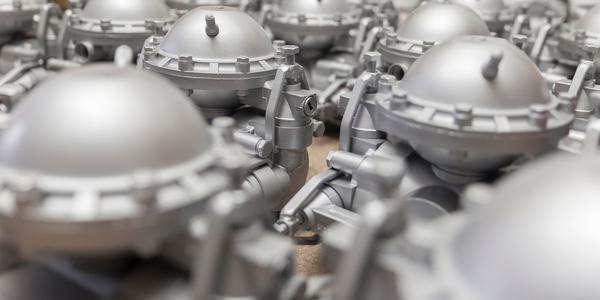
Case Study
Monitoring of Pressure Pumps in Automotive Industry
A large German/American producer of auto parts uses high-pressure pumps to deburr machined parts as a part of its production and quality check process. They decided to monitor these pumps to make sure they work properly and that they can see any indications leading to a potential failure before it affects their process.