Tillamook County Creamery Association, Oregon invests in $23million expansion
公司规模
Large Corporate
地区
- America
国家
- United States
产品
- Westfalia AS/RS
- Westfalia WMS
- Allen-Bradley ControlLogix
- SEW Eurodrive
- SICK laser positioning system
技术栈
- Programmable Logic Controllers (PLC)
- Wireless LAN
- Barcode Tracking
- VPN
实施规模
- Enterprise-wide Deployment
影响指标
- Productivity Improvements
- Customer Satisfaction
- Digital Expertise
技术
- 功能应用 - 仓库管理系统 (WMS)
- 自动化与控制 - 可编程逻辑控制器 (PLC)
适用行业
- 食品与饮料
适用功能
- 仓库和库存管理
用例
- 仓库自动化
- 库存管理
- 预测性维护
服务
- 系统集成
- 培训
关于客户
Tillamook County Creamery Association (TCCA) is a renowned dairy cooperative based in Oregon, USA. Established in 1909, TCCA has grown to become one of the leading producers of dairy products in the United States, known for its high-quality cheese, ice cream, and other dairy products. The cooperative is owned by nearly 80 farming families, who are dedicated to sustainable farming practices and producing the best possible dairy products. TCCA operates a state-of-the-art production facility that includes an automated warehouse system to manage its extensive inventory of dairy products. The cooperative has a strong commitment to innovation and continuous improvement, which has helped it maintain its competitive edge in the market. With a focus on customer satisfaction and product quality, TCCA has built a loyal customer base and a strong brand reputation over the years.
挑战
Operating since April 2000, the Automated Storage and Retrieval System (AS/RS) was upgraded in 2007 by Westfalia, to keep up with advances in technology. The improvements included upgrades to the facility’s Storage/ Retrieval Machine (S/RM), programmable logic code (PLC) and new drive and positioning technology. While the existing AS/RS performed as required, Tillamook’s sales growth was placing increasing demands on their system. Once they became aware that advances in technology could improve the AS/ RS operations, Tillamook decided to upgrade their automated warehouse. Upgrading the S/RM controls would make it work faster, and smoother. Updating the WMS would improve the speed, accuracy and reliability of the warehouse product flows. Tillamook’s automated warehouse is 12-levels, 66 ft. high and holds 15,040 pallet positions to hold 35 million lbs. of block cheese and finished products. A wall divides the facility into two sections, with 40 lbs. blocks stored on the north side, and finished products stored on the south side.
解决方案
As part of the AS/RS upgrades, the controls on the S/RM were replaced with an Allen-Bradley ControlLogix solution, which can be accessed remotely via VPN for easier troubleshooting by Westfalia’s Service Department. Horizontal and vertical drive systems were upgraded to SEW Eurodrive, while mechanical encoder positioning devices were replaced with a SICK laser positioning system on the horizontal and vertical axis. Westfalia’s Warehouse Management System (WMS) controls and optimizes the product flows throughout the facility. Products are tracked by bar code for easy identification and pallet storage. This results in a controlled, paperless environment that coordinates order picking and processing with the host computer. Westfalia’s WMS at Tillamook, a predecessor of our recent Savanna.NET® WMS, has proven its ease of use, reducing training time, and resulting in faster more efficient product flows. Westfalia updated the communication infrastructure between the S/RM, Warehouse Management System (WMS) and Conveyor System, replacing an infrared and a second hardwired interface with a Wireless LAN, thereby eliminating electrical interference issues due to mechanical wear. In addition, all conveyor PLC and WMS communication interfaces have been brought up to the most recent Westfalia standard.
运营影响
数量效益
Case Study missing?
Start adding your own!
Register with your work email and create a new case study profile for your business.
相关案例.

Case Study
The Kellogg Company
Kellogg keeps a close eye on its trade spend, analyzing large volumes of data and running complex simulations to predict which promotional activities will be the most effective. Kellogg needed to decrease the trade spend but its traditional relational database on premises could not keep up with the pace of demand.

Case Study
HEINEKEN Uses the Cloud to Reach 10.5 Million Consumers
For 2012 campaign, the Bond promotion, it planned to launch the campaign at the same time everywhere on the planet. That created unprecedented challenges for HEINEKEN—nowhere more so than in its technology operation. The primary digital content for the campaign was a 100-megabyte movie that had to play flawlessly for millions of viewers worldwide. After all, Bond never fails. No one was going to tolerate a technology failure that might bruise his brand.Previously, HEINEKEN had supported digital media at its outsourced datacenter. But that datacenter lacked the computing resources HEINEKEN needed, and building them—especially to support peak traffic that would total millions of simultaneous hits—would have been both time-consuming and expensive. Nor would it have provided the geographic reach that HEINEKEN needed to minimize latency worldwide.

Case Study
Energy Management System at Sugar Industry
The company wanted to use the information from the system to claim under the renewable energy certificate scheme. The benefit to the company under the renewable energy certificates is Rs 75 million a year. To enable the above, an end-to-end solution for load monitoring, consumption monitoring, online data monitoring, automatic meter data acquisition which can be exported to SAP and other applications is required.

Case Study
Coca Cola Swaziland Conco Case Study
Coco Cola Swaziland, South Africa would like to find a solution that would enable the following results: - Reduce energy consumption by 20% in one year. - Formulate a series of strategic initiatives that would enlist the commitment of corporate management and create employee awareness while helping meet departmental targets and investing in tools that assist with energy management. - Formulate a series of tactical initiatives that would optimize energy usage on the shop floor. These would include charging forklifts and running cold rooms only during off-peak periods, running the dust extractors only during working hours and basing lights and air-conditioning on someone’s presence. - Increase visibility into the factory and other processes. - Enable limited, non-intrusive control functions for certain processes.

Case Study
Temperature Monitoring for Restaurant Food Storage
When it came to implementing a solution, Mr. Nesbitt had an idea of what functionality that he wanted. Although not mandated by Health Canada, Mr. Nesbitt wanted to ensure quality control issues met the highest possible standards as part of his commitment to top-of-class food services. This wish list included an easy-to use temperature-monitoring system that could provide a visible display of the temperatures of all of his refrigerators and freezers, including historical information so that he could review the performance of his equipment. It also had to provide alert notification (but email alerts and SMS text message alerts) to alert key staff in the event that a cooling system was exceeding pre-set warning limits.
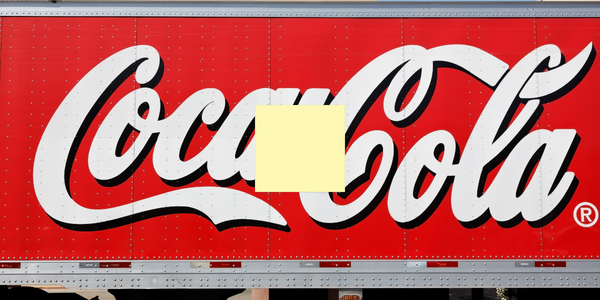
Case Study
Coca-Cola Refreshments, U.S.
Coca-Cola Refreshments owns and manages Coca-Cola branded refrigerators in retail establishments. Legacy systems were used to locate equipment information by logging onto multiple servers which took up to 8 hours to update information on 30-40 units. The company had no overall visibility into equipment status or maintenance history.