SPDM and JobBoss
公司规模
SME
地区
- America
国家
- United States
产品
- JobBOSS
技术栈
- ERP System
实施规模
- Enterprise-wide Deployment
影响指标
- Productivity Improvements
- Customer Satisfaction
技术
- 功能应用 - 企业资源规划系统 (ERP)
适用行业
- 设备与机械
- 航天
- 医疗保健和医院
适用功能
- 离散制造
- 质量保证
用例
- 自动化制造系统
- 预测性维护
服务
- 系统集成
- 培训
关于客户
San Diego Precision Machining (SDPM) is a 45-person company founded in 1971. They originally started as a prototype shop for the San Diego region, but over time, they expanded into longer production runs and more materials. Today, they are well known for their high-quality product and attention to customer needs. They are ISO 9100:2009 and AS 9100 Rev C certified. The company’s commitment to quality, delivery, and fair prices makes them a leader in the industry. SDPM specializes in close tolerance CNC machining for both small volume prototypes and high volume production quantity runs. Its customers are in industries ranging from medical devices to aerospace and military – all industries where tight tolerances are required. The company works with a wide variety of materials including aluminum, stainless, titanium, and even PVC and other plastics.
挑战
San Diego Precision Machining (SDPM) was experiencing rapid growth and found that its legacy ERP system could not keep up. The company's owner, Jason Matteson, had plans for further expansion but realized that their existing ERP system wouldn't support this growth. The existing vendor's focus was on traditional MRP rather than ERP for job shops, and despite releasing several new versions, there was no new functionality. Furthermore, the support offered by the vendor was poor. Matteson knew he had to look for a new solution or abandon his growth plans. Despite the previous vendor's efforts to accommodate their needs, SDPM found JobBOSS was a premier solution that could continue to evolve with them.
解决方案
SDPM selected JobBOSS because of its excellent functional fit and reputation for superior support. The implementation of the system was less strenuous and cumbersome than expected, thanks to the outstanding training and support provided by JobBOSS. All users were up and running in less than a month. They ran in parallel for two weeks before going live. The system’s intuitive design made it easy to learn and implement rapidly. SDPM went live using the Quoting, Order processing, Invoicing, Purchasing, Shop Floor Control, Production Scheduling, and Data Collection modules of JobBOSS, and are currently transitioning from their prior accounting system to JobBOSS Financials. One big advantage they noticed right away was the system’s consistency. All the forms – quotations, order acknowledgements, and invoices – have a consistent look and feel, which is important for customers and for the company’s brand.
运营影响
数量效益
Case Study missing?
Start adding your own!
Register with your work email and create a new case study profile for your business.
相关案例.

Case Study
Smart Water Filtration Systems
Before working with Ayla Networks, Ozner was already using cloud connectivity to identify and solve water-filtration system malfunctions as well as to monitor filter cartridges for replacements.But, in June 2015, Ozner executives talked with Ayla about how the company might further improve its water systems with IoT technology. They liked what they heard from Ayla, but the executives needed to be sure that Ayla’s Agile IoT Platform provided the security and reliability Ozner required.

Case Study
IoT enabled Fleet Management with MindSphere
In view of growing competition, Gämmerler had a strong need to remain competitive via process optimization, reliability and gentle handling of printed products, even at highest press speeds. In addition, a digitalization initiative also included developing a key differentiation via data-driven services offers.
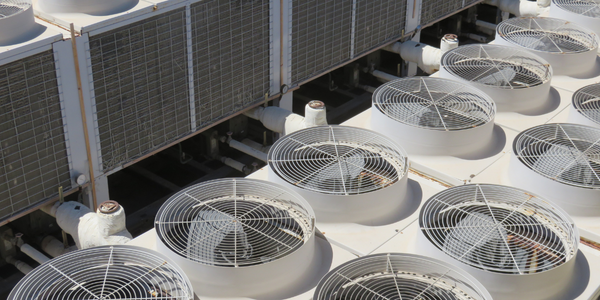
Case Study
Predictive Maintenance for Industrial Chillers
For global leaders in the industrial chiller manufacturing, reliability of the entire production process is of the utmost importance. Chillers are refrigeration systems that produce ice water to provide cooling for a process or industrial application. One of those leaders sought a way to respond to asset performance issues, even before they occur. The intelligence to guarantee maximum reliability of cooling devices is embedded (pre-alarming). A pre-alarming phase means that the cooling device still works, but symptoms may appear, telling manufacturers that a failure is likely to occur in the near future. Chillers who are not internet connected at that moment, provide little insight in this pre-alarming phase.

Case Study
Premium Appliance Producer Innovates with Internet of Everything
Sub-Zero faced the largest product launch in the company’s history:It wanted to launch 60 new products as scheduled while simultaneously opening a new “greenfield” production facility, yet still adhering to stringent quality requirements and manage issues from new supply-chain partners. A the same time, it wanted to increase staff productivity time and collaboration while reducing travel and costs.

Case Study
Integration of PLC with IoT for Bosch Rexroth
The application arises from the need to monitor and anticipate the problems of one or more machines managed by a PLC. These problems, often resulting from the accumulation over time of small discrepancies, require, when they occur, ex post technical operations maintenance.
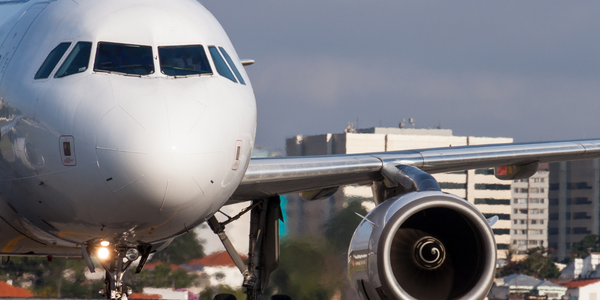
Case Study
Airbus Soars with Wearable Technology
Building an Airbus aircraft involves complex manufacturing processes consisting of thousands of moving parts. Speed and accuracy are critical to business and competitive advantage. Improvements in both would have high impact on Airbus’ bottom line. Airbus wanted to help operators reduce the complexity of assembling cabin seats and decrease the time required to complete this task.