Semiconductor Manufacturer Reduces Product Defects and Lost Profits through Consistent Risk Assessment
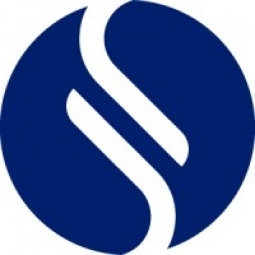
公司规模
Large Corporate
地区
- America
- Asia
- Europe
国家
- Singapore
- United States
产品
- Quality Risk Management
- Failure Modes and Effect Analysis (FMEA)
- Global Context Matrix
技术栈
- Risk Assessment Software
- Centralized System
实施规模
- Enterprise-wide Deployment
影响指标
- Cost Savings
- Productivity Improvements
- Waste Reduction
技术
- 分析与建模 - 预测分析
适用行业
- 半导体
- 电子产品
适用功能
- 质量保证
- 产品研发
用例
- 质量预测分析
- 制造过程模拟
服务
- 系统集成
- 数据科学服务
关于客户
The customer is one of the world’s leading semiconductor manufacturing companies, with nearly 300 worldwide customers and 20,000 employees. The company manufactures microchips that are used in a wide variety of electronic devices, from automobiles to smartphones. The impact of a defective product can be extremely costly, ranging up to $1 billion. Therefore, the ability to identify, analyze and mitigate risks involved in product manufacturing is of the utmost importance. The company had a goal of zero defects and was in search of a better process to mitigate risks and deliver quality products to its customers.
挑战
The semiconductor manufacturer, with several business units spanning three continents, lacked a consistent process for managing risk related to the thousands of products it produces. Each business entity had its own homegrown solution, leading to inconsistency in information across the enterprise. The semiconductor business is complex due to the variety of products and the many risk analyses performed at various levels. An unmitigated risk at the smallest level could have a huge impact on something at a much higher level. The company needed a centralized operational risk management solution.
解决方案
The company partnered with Sphera to provide a consolidated operational risk management solution. Through a series of design sessions, Sphera was able to identify the nine interrelated factors involved in risk assessment analyses and map them into a global context matrix. The centralized system and context matrix solved the issue of information in silos. Now, the company can see the impact of the risk created by local process changes at any one of their manufacturing locations on a global level. The centralized process has helped the company dramatically reduce the number of risk analyses it undertakes, while improving the quality. The company now has a much stronger process for assessing risk and identifying defects before they become even more costly.
运营影响
数量效益
Case Study missing?
Start adding your own!
Register with your work email and create a new case study profile for your business.
相关案例.

Case Study
Remote Temperature Monitoring of Perishable Goods Saves Money
RMONI was facing temperature monitoring challenges in a cold chain business. A cold chain must be established and maintained to ensure goods have been properly refrigerated during every step of the process, making temperature monitoring a critical business function. Manual registration practice can be very costly, labor intensive and prone to mistakes.
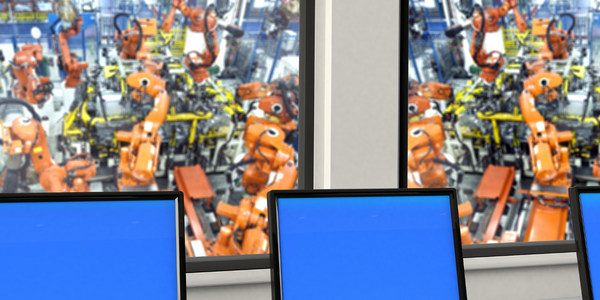
Case Study
KINESYS Semiconductor Factory Automation Software
KINESYS Software provides both Integrated Device Manufacturer (IDM) and Original Equipment Manufacturer (OEM) customers world-class software products and solutions for advanced wafer and device traceability and process management. KINESYS offers state of the art database technology with a core focus on SEMI standards. KINESYS’ challenge was to make back-end processing failure-free and easy to use for clients while supporting licensing models more adaptable to changing industry needs.
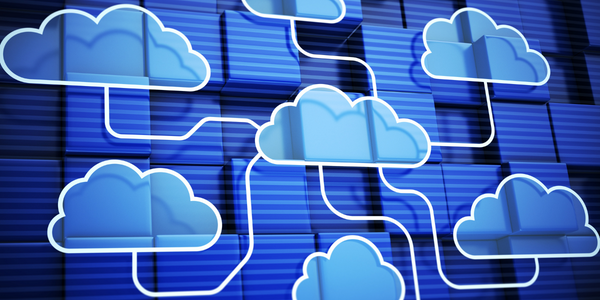
Case Study
Cloud Solution for Energy Management Platform-Schneider Electric
Schneider Electric required a cloud solution for its energy management platform to manage high computational operations, which were essential for catering to client requirements. As the business involves storage and analysis of huge amounts of data, the company also needed a convenient and scalable storage solution to facilitate operations efficiently.
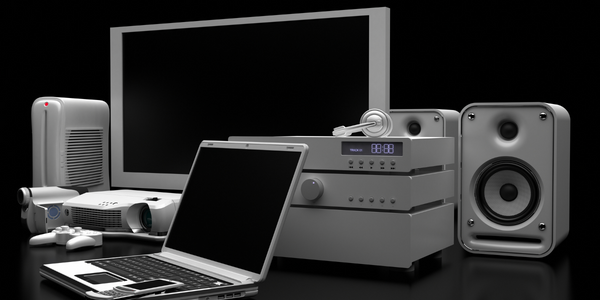
Case Study
Leveraging the IoT to Gain a Competitive Edge in International Competition
Many large manufacturers in and outside Japan are competing for larger market share in the same space, expecting a growing demand for projectors in the areas of entertainment, which requires glamor and strong visual performance as well as digital signage that can attract people’s attention. “It is becoming more and more difficult to differentiate ourselves with stand-alone hardware products,” says Kazuyuki Kitagawa, Director of Service & Support at Panasonic AVC Networks. “In order for Panasonic to grow market share and overall business, it is essential for us to develop solutions that deliver significant added value.” Panasonic believes projection failure and quality deterioration should never happen. This is what and has driven them to make their projectors IoT-enabled. More specifically, Panasonic has developed a system that collects data from projectors, visualizes detailed operational statuses, and predicts issues and address them before failure occurs. Their projectors are embedded with a variety of sensors that measure power supply, voltage, video input/ output signals, intake/exhaust air temperatures, cooling fan operations, and light bulb operating time. These sensors have been used to make the projector more intelligent, automatically suspending operation when the temperature rises excessively, and automatically switching light bulbs. Although this was a great first step, Panasonic projectors were still not equipped with any capability to send the data over a network.