Pepsi Hungary uses an SPC system based on STATISTICA Enterprise
公司规模
1,000+
地区
- Europe
国家
- Hungary
产品
- STATISTICA Enterprise
技术栈
- SQL Database
实施规模
- Enterprise-wide Deployment
影响指标
- Customer Satisfaction
- Environmental Impact Reduction
- Productivity Improvements
- Waste Reduction
技术
- 分析与建模 - 预测分析
适用行业
- 食品与饮料
适用功能
- 质量保证
用例
- 质量预测分析
- 过程控制与优化
服务
- 系统集成
- 培训
关于客户
Pepsi Hungary, a subsidiary of PepsiCo, produces various brands of carbonated beverages, including Pepsi, 7Up, and Mirinda. The company is wholly owned by PepsiCo following the merger of PAS, PBG, and PepsiCo. Pepsi Hungary is committed to maintaining high-quality standards in its production processes and ensuring sustainability by reducing waste and carbon footprint. The company sought to implement a new SPC system to enhance its quality monitoring and control capabilities, following successful implementations at other Pepsi plants in Poland and the Czech Republic.
挑战
Mr. József Sinkó, quality assurance & regulatory manager at Pepsi Hungary, highlighted the need for an effective SPC system to ensure strict quality requirements in production processes. The previous SPC system was cumbersome and time-consuming, lacking the necessary tools for efficient data analysis over extended periods or multiple parameters. Pepsi Hungary required a system that could monitor and control product quality parameters, recognize trends, and identify error sources. Additionally, the company aimed to monitor machine capability, eliminate waste, and reduce the plant's carbon footprint.
解决方案
Pepsi Hungary implemented a customized SPC system based on STATISTICA Enterprise, tailored to meet local specific requirements. Unlike the systems at the Polish and Czech Pepsi plants, the Hungarian implementation connected the STATISTICA Enterprise SPC system to a third-party data collection system that had been in use for many years. The new system performs statistical analyses and generates analysis reports from data stored in the SQL database of the third-party system. The SPC system measures various quality parameters during production, such as sugar concentration, carbon dioxide concentration, acidity, volume, and bottle cap tightness. These parameters are calculated using different specifications for different products. The system provides up-to-date, detailed reports that make quality assurance more effective and allows for easy calculation of process capability indices for any selected period.
运营影响
数量效益
Case Study missing?
Start adding your own!
Register with your work email and create a new case study profile for your business.
相关案例.

Case Study
The Kellogg Company
Kellogg keeps a close eye on its trade spend, analyzing large volumes of data and running complex simulations to predict which promotional activities will be the most effective. Kellogg needed to decrease the trade spend but its traditional relational database on premises could not keep up with the pace of demand.

Case Study
HEINEKEN Uses the Cloud to Reach 10.5 Million Consumers
For 2012 campaign, the Bond promotion, it planned to launch the campaign at the same time everywhere on the planet. That created unprecedented challenges for HEINEKEN—nowhere more so than in its technology operation. The primary digital content for the campaign was a 100-megabyte movie that had to play flawlessly for millions of viewers worldwide. After all, Bond never fails. No one was going to tolerate a technology failure that might bruise his brand.Previously, HEINEKEN had supported digital media at its outsourced datacenter. But that datacenter lacked the computing resources HEINEKEN needed, and building them—especially to support peak traffic that would total millions of simultaneous hits—would have been both time-consuming and expensive. Nor would it have provided the geographic reach that HEINEKEN needed to minimize latency worldwide.

Case Study
Energy Management System at Sugar Industry
The company wanted to use the information from the system to claim under the renewable energy certificate scheme. The benefit to the company under the renewable energy certificates is Rs 75 million a year. To enable the above, an end-to-end solution for load monitoring, consumption monitoring, online data monitoring, automatic meter data acquisition which can be exported to SAP and other applications is required.

Case Study
Coca Cola Swaziland Conco Case Study
Coco Cola Swaziland, South Africa would like to find a solution that would enable the following results: - Reduce energy consumption by 20% in one year. - Formulate a series of strategic initiatives that would enlist the commitment of corporate management and create employee awareness while helping meet departmental targets and investing in tools that assist with energy management. - Formulate a series of tactical initiatives that would optimize energy usage on the shop floor. These would include charging forklifts and running cold rooms only during off-peak periods, running the dust extractors only during working hours and basing lights and air-conditioning on someone’s presence. - Increase visibility into the factory and other processes. - Enable limited, non-intrusive control functions for certain processes.

Case Study
Temperature Monitoring for Restaurant Food Storage
When it came to implementing a solution, Mr. Nesbitt had an idea of what functionality that he wanted. Although not mandated by Health Canada, Mr. Nesbitt wanted to ensure quality control issues met the highest possible standards as part of his commitment to top-of-class food services. This wish list included an easy-to use temperature-monitoring system that could provide a visible display of the temperatures of all of his refrigerators and freezers, including historical information so that he could review the performance of his equipment. It also had to provide alert notification (but email alerts and SMS text message alerts) to alert key staff in the event that a cooling system was exceeding pre-set warning limits.
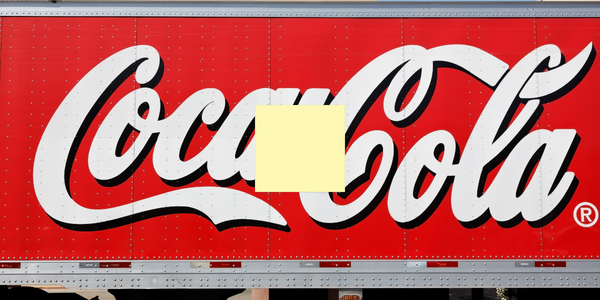
Case Study
Coca-Cola Refreshments, U.S.
Coca-Cola Refreshments owns and manages Coca-Cola branded refrigerators in retail establishments. Legacy systems were used to locate equipment information by logging onto multiple servers which took up to 8 hours to update information on 30-40 units. The company had no overall visibility into equipment status or maintenance history.