公司规模
Large Corporate
地区
- Asia
国家
- Pakistan
产品
- SimSci DYNSIM
- SimSci SIM4ME Common Modeling Environment
- SimSci FSIM Plus
- SimSci TRISIM Plus
技术栈
- Distributed Control System (DCS)
- Operator Training Simulator (OTS)
实施规模
- Enterprise-wide Deployment
影响指标
- Productivity Improvements
- Employee Satisfaction
技术
- 功能应用 - 远程监控系统
适用行业
- 化学品
适用功能
- 离散制造
- 维护
用例
- 预测性维护
- 虚拟培训
服务
- 培训
- 系统集成
关于客户
Fauji Fertilizer Company (FFC) is a leading fertilizer manufacturing company based in Goth Machhi, Pakistan. Since 1982, FFC has been providing premium quality fertilizer products to their commercial customers. As one of the largest manufacturers in the country, the operation produces 551,000 metric tons of urea and 445,500 metric tons of diammonium phosphate (DAP) annually. The company operates three production facilities. The FFC vision is to achieve excellence in every aspect of plant operation, which is tied to benchmarks of safety, reliability, efficiency and environmental sensitivity.
挑战
Fauji Fertilizer Company (FFC) was facing a challenge of training their personnel on the newly-commissioned Distributed Control System (DCS) to reduce operational incidents, increase uptime and equip operators to respond to emergencies. The company also wanted to maintain a high level of performance for experienced operators and new hires alike. Another challenge was to quickly and effectively prepare new plant operators to work in actual control room and field environments. The company was also facing manpower challenges due to upcoming retirements and anticipated higher attrition rate. The company needed a solution that could expose new hires to critical and emergency scenarios that happen only infrequently.
解决方案
FFC decided to implement an Operator Training Simulator (OTS) system to train their personnel on the newly-commissioned DCS. The OTS was expected to decrease the risk of major operational incidents, reduce startup and downtime, increase the plant’s on stream factor and improve efficient handling of emergencies. The company selected Schneider Electric's OTS implementation because it offered a direct-connect system with no requirement for translation, emulation or recompilation of the system configuration, a technically superior process and system model, high fidelity with an accuracy level of +2% PFD value, and strong technical and engineering expertise with long-term maintenance support. The OTS was designed and deployed in conjunction with the installation of the new DCS. The company also adopted a 'train the trainer' approach where two lead engineers were trained first who then conducted 130 training sessions in the first year.
运营影响
数量效益
Case Study missing?
Start adding your own!
Register with your work email and create a new case study profile for your business.
相关案例.
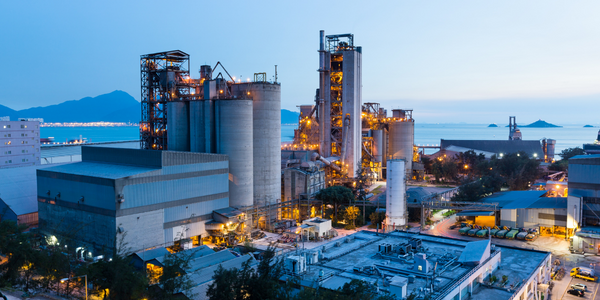
Case Study
Honeywell - Tata Chemicals Improves Data Accessibility with OneWireless
Tata was facing data accessibility challenges in the cement plant control room tapping signals from remote process control areas and other distant locations, including the gas scrubber. Tata needed a wireless solution to extend its control network securely to remote locations that would also provide seamless communication with existing control applications.

Case Study
Advanced Elastomer Systems Upgrades Production
In order to maintain its share of the international market for thermoplastic elastomers AES recently expanded its Florida plant by adding a new production line. While the existing lines were operating satisfactorily using a PROVOX distributed control system with traditional analog I/O, AES wanted advanced technology on the new line for greater economy, efficiency, and reliability. AES officials were anxious to get this line into production to meet incoming orders, but two hurricanes slowed construction.
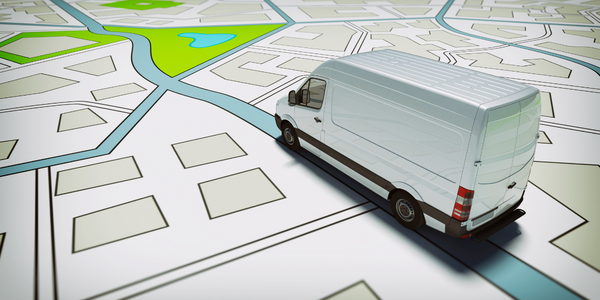
Case Study
Wireless GPS Tracking & Security Monitoring
Enhancing the security of hazardous freight and ensuring compliance with Homeland Security’s Transportation Security Administration mandate that all trains carrying chemicals capable of creating a toxic inhalation condition are equipped with on-board safety monitoring systems.
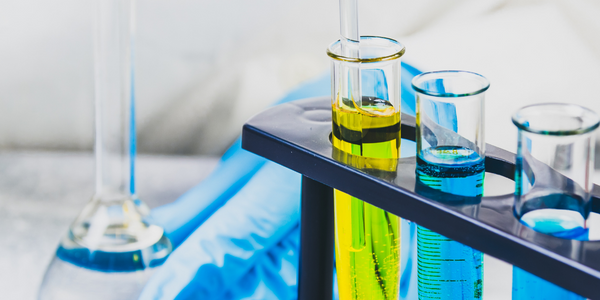
Case Study
Field Device Asset Management For Chemical Company in China
Chinese chemical subsidiary of multinational corporation serves customers throughout the world. Sales offices and research and technology centers are strategically located to provide rapid response to customer requests. Just two workers were assigned to maintain thousands of intelligent instruments in three production units, so they could do little more than react to device issues as they appeared. This costly maintenance method inevitably led to unexpected downtime when a critical instrument failed. Plant management recognized the need to change from reactive to predictive maintenance for all assets, including instruments and control valves, but help was needed in implementing such a technology-based initiative.
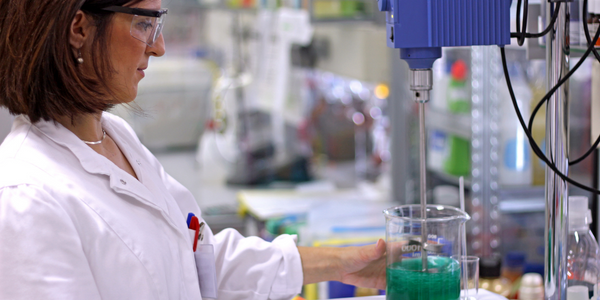
Case Study
Industrial Workforce Mobility for Improved Safety & Operations
Huntsman Corporation, a global manufacturer and marketer of differentiated chemicals, undertook an aggressive program to eliminate injuries, product defects, and environmental releases at their Port Neches facility. Termed “Project Zero”, this program required a completely mobile solution to empower operations and maintenance personnel to capture defects, track work progress and make process and safety related decisions in real-time.