Leading Automotive Supplier Accelerates Lean Operations
公司规模
Mid-size Company
地区
- America
国家
- United States
产品
- EnterpriseIQ
- RealTime Production Monitoring
- Quality Management
技术栈
- Oracle database
- Windows-based PCs
实施规模
- Enterprise-wide Deployment
影响指标
- Cost Savings
- Productivity Improvements
- Customer Satisfaction
技术
- 功能应用 - 企业资源规划系统 (ERP)
- 分析与建模 - 实时分析
适用行业
- 汽车
适用功能
- 离散制造
- 质量保证
用例
- 预测性维护
- 供应链可见性(SCV)
服务
- 系统集成
- 软件设计与工程服务
关于客户
Nissen Chemitec America, a leading plastic injection molding company, supplies quality plastic parts to leading automobile manufacturers such as Honda Motor Company of America Inc.™, as well as to a diverse range of other leading manufacturers around the world. Founded in 1988 by Nissen Chemitec Corporation of Niihama, Japan and Ohio based steel company Worthington Industries, Nissen Chemitec America is now owned and operated solely by Nissen Chemitec Corporation. With over 250 employees at its London, Ohio plant, Nissen Chemitec America is ISO certified and provides a full range of quality solutions, including: research and development; design services; mold building; injection and insert molding; finishing; assembly; and just-in-time (JIT) delivery.
挑战
Nissen Chemitec America, a leading manufacturer serving automakers, was managing enterprise operations with an AS/400-based system, which was eventually replaced with an ERP software that promoted its design for automotive manufacturers. However, the latter system, while conforming to automotive customers’ stringent requirements, hindered Nissen Chemitec America’s ability to advance lean manufacturing principles. The company was looking for a more tailored ERP solution— one built specifically for contract manufacturers serving the automotive industry. The previous system was cumbersome, required heavy data entry, and blocked the company's lean efforts due to the maintenance required. The company needed a fully automated system that not only adhered to the automotive compliance requirements like electronic data interchange (EDI), Labeling, and quality functions, but was also robust as well as scalable.
解决方案
Nissen Chemitec America found the best solution to be EnterpriseIQ from IQMS. With specific functionality designed to meet the challenges auto suppliers face day to day, EnterpriseIQ helps manufacturers like Nissen Chemitec America stay flexible and lean within the distinctive confines of industry compliance and ever changing customer demands. EnterpriseIQ from IQMS fully supports Nissen Chemitec America’s lean initiatives, unlike the company’s previous ERP system, which impeded lean progress in a number of ways. For example, their previous system was built upon multiple databases that required repetitive data entry across various modules and functions. Additionally, the previous package was not automated and had limited bar code scanning capabilities. Scheduling was done manually using spreadsheets and production data had to be keyed in separately for reporting. The IQMS EDI module is seamlessly embedded within the EnterpriseIQ system, which operates entirely within a single database, so Nissen Chemitec America has no cumbersome third party hardware interfaces to manage. Incoming EDI files are automatically translated into the ERP system, instantly updating all pertinent records. Outgoing files are automatically transferred back to customers and suppliers. And there’s never a need for manual data entry, so Nissen Chemitec America benefits from accurate, automatic and timely communication across its entire supply chain.
运营影响
数量效益
Case Study missing?
Start adding your own!
Register with your work email and create a new case study profile for your business.
相关案例.
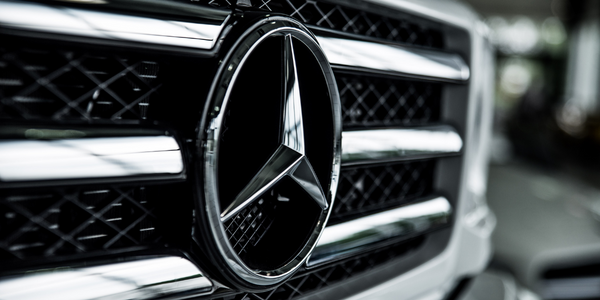
Case Study
Integral Plant Maintenance
Mercedes-Benz and his partner GAZ chose Siemens to be its maintenance partner at a new engine plant in Yaroslavl, Russia. The new plant offers a capacity to manufacture diesel engines for the Russian market, for locally produced Sprinter Classic. In addition to engines for the local market, the Yaroslavl plant will also produce spare parts. Mercedes-Benz Russia and his partner needed a service partner in order to ensure the operation of these lines in a maintenance partnership arrangement. The challenges included coordinating the entire maintenance management operation, in particular inspections, corrective and predictive maintenance activities, and the optimizing spare parts management. Siemens developed a customized maintenance solution that includes all electronic and mechanical maintenance activities (Integral Plant Maintenance).
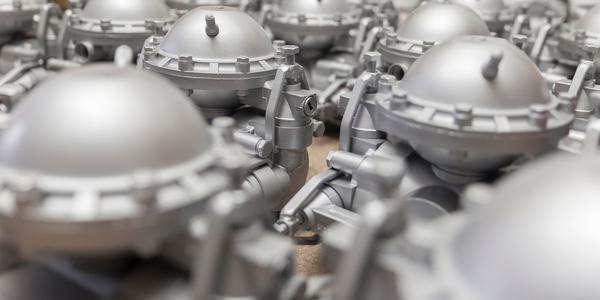
Case Study
Monitoring of Pressure Pumps in Automotive Industry
A large German/American producer of auto parts uses high-pressure pumps to deburr machined parts as a part of its production and quality check process. They decided to monitor these pumps to make sure they work properly and that they can see any indications leading to a potential failure before it affects their process.