公司规模
Large Corporate
地区
- Europe
- Asia
国家
- Czech Republic
产品
- VectorAuto MX9
- VectorAuto iX9
技术栈
- CNC Cutting Equipment
- Eclipse Technology
实施规模
- Enterprise-wide Deployment
影响指标
- Productivity Improvements
- Customer Satisfaction
- Cost Savings
技术
- 功能应用 - 制造执行系统 (MES)
- 自动化与控制 - 自动化与过程控制系统
适用行业
- 汽车
适用功能
- 流程制造
用例
- 自动化制造系统
- 过程控制与优化
- 预测性维护
服务
- 系统集成
- 培训
关于客户
Johnson Controls is a global diversified technology and industrial leader serving customers in more than 150 countries. The company’s 170,000 employees create quality products, services and solutions to optimize energy and operational efficiencies of buildings; lead-acid automotive batteries and advanced batteries for hybrid and electric vehicles; and interior systems for automobiles. Johnson Controls’ commitment to sustainability dates back to its roots in 1885, with the invention of the first electric room thermostat. Through its growth strategies and by increasing market share, Johnson Controls is committed to delivering value to shareholders and making its customers successful.
挑战
For over 80 years, Johnson Controls has led the automotive trim cover industry by providing seating systems that differentiate vehicles and offer customers what they want most—style, comfort, and safety. However, as the trend in automotive interior personalization became more mainstream, the innovative automotive supplier recognized that producing the same volume of car sets as they had in the past while managing the proliferation of options for interiors—different fabrics, styles, and features—would be impossible with the die press system they had been using. Long changeover times, the cost of changing die boards midway through a program, and the inability to change the pattern in a die severely limited Johnson Controls’ production flexibility. In addition, high levels of fabric waste caused by the large buffer between pieces and end loss due to the fixed length of the die board, increased production costs. To improve its competitive position in a changing market and win new business required finding a solution that would allow them to deliver a wider variety of options, meet tight production schedules and reduce fabric costs. Johnson Controls’ executive team decided to undertake a highly strategic project to transform their fabric-cutting value chain by replacing all the die presses in their European plants with automated computer numerical control (CNC) cutting equipment.
解决方案
Johnson Controls evaluated multiple technology providers for the cutting room transformation project but Lectra was the only candidate that combined the leading-edge technology, cutting room expertise, and global support services to effectively deliver a project of this breadth. As early adopters of VectorAuto MX9®, Johnson Controls was already familiar with the performance and productivity of Lectra’s high-ply, automotive fabric cutting equipment. Breakthrough technology integrated into the MX9 enabled the company to cut more plies of material faster and with a consistently high level of quality. Its high-performance cutting head and Eclipse technology, which provides the ability to cut during conveyor advance, guaranteed even higher throughput. Features such as a built-in blade deviation controller, automatic blade path correction, and optimized cutting of tangent pieces ensured precision cutting and repeatability. To meet the goal of obtaining the highest level of performance, Johnson Controls decided to also equip their cutting rooms with VectorAuto iX9®, Lectra’s latest top-of-the-line fabric cutting solution, upon its launch in 2012. The iX9 expands upon the capabilities of the MX9; its high-performance cutting head and the ability to cut during conveyer advance guarantee even higher throughput. Lean-compliant poka yoke and visual management systems, such as automatic drill diameter identification and video-assisted spread position control, further maximize production output and efficiency.
运营影响
数量效益
Case Study missing?
Start adding your own!
Register with your work email and create a new case study profile for your business.
相关案例.
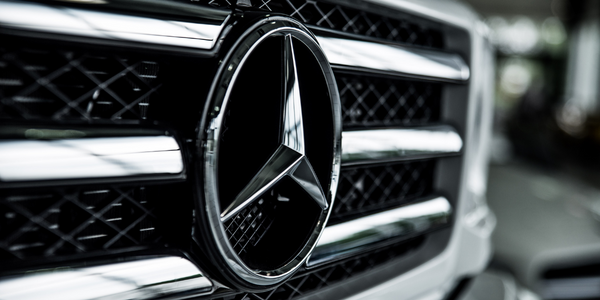
Case Study
Integral Plant Maintenance
Mercedes-Benz and his partner GAZ chose Siemens to be its maintenance partner at a new engine plant in Yaroslavl, Russia. The new plant offers a capacity to manufacture diesel engines for the Russian market, for locally produced Sprinter Classic. In addition to engines for the local market, the Yaroslavl plant will also produce spare parts. Mercedes-Benz Russia and his partner needed a service partner in order to ensure the operation of these lines in a maintenance partnership arrangement. The challenges included coordinating the entire maintenance management operation, in particular inspections, corrective and predictive maintenance activities, and the optimizing spare parts management. Siemens developed a customized maintenance solution that includes all electronic and mechanical maintenance activities (Integral Plant Maintenance).
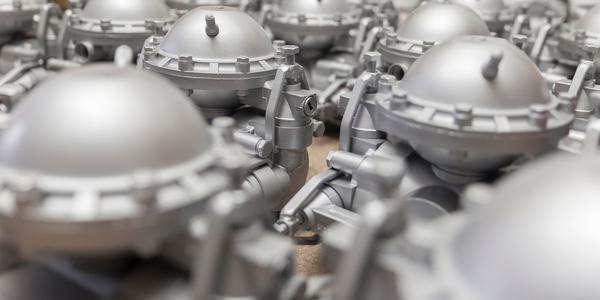
Case Study
Monitoring of Pressure Pumps in Automotive Industry
A large German/American producer of auto parts uses high-pressure pumps to deburr machined parts as a part of its production and quality check process. They decided to monitor these pumps to make sure they work properly and that they can see any indications leading to a potential failure before it affects their process.