Global Contract Manufacturer Empowers Customers to Optimize Their Businesses
公司规模
Large Corporate
地区
- America
- Asia
- Europe
国家
- United States
产品
- MPO Platform
- Order-Centric TMS
技术栈
- Cloud Platform
- Predictive Analytics
实施规模
- Enterprise-wide Deployment
影响指标
- Customer Satisfaction
- Productivity Improvements
- Environmental Impact Reduction
技术
- 平台即服务 (PaaS) - 连接平台
- 分析与建模 - 预测分析
- 功能应用 - 运输管理系统 (TMS)
适用行业
- 汽车
- 医疗保健和医院
- 消费品
适用功能
- 物流运输
- 仓库和库存管理
- 商业运营
用例
- 供应链可见性(SCV)
服务
- 系统集成
- 云规划/设计/实施服务
- 数据科学服务
关于客户
Flex Ltd. is a global contract manufacturer with 160,000 employees in over 30 countries. The company serves customers in various segments, including automotive, communications, energy, healthcare, and industrial. Flex manages design, manufacturing, and distribution, and is committed to environmental sustainability through repair, mid-life, and end-of-life activities. The company is known for its technology leadership and extensive network of 16,000 suppliers, manufacturing 12,500 unique end products.
挑战
Flex Ltd., a global contract manufacturer, faced challenges in managing its complex supply chains across different regions. The company was using different transportation management approaches in each region, leading to reactionary decisions and poor collaboration across geographically dispersed teams. Flex needed a more modern transport order management approach to support its global operations and improve collaboration.
解决方案
Flex selected MPO's global cloud platform for supply chain and transport orchestration to address its challenges. The MPO platform offers capabilities for control tower, supply chain visibility, order management, e-fulfillment, transportation management, returns management, and supplier collaboration. The platform enables Flex to optimize all activities from order receipt to final delivery, providing real-time, continuous control over supply chain activities. The MPO platform's flexibility allows it to handle complex business rules and automate processes, such as separating and shipping dangerous goods components.
运营影响
数量效益
Case Study missing?
Start adding your own!
Register with your work email and create a new case study profile for your business.
相关案例.
.png)
Case Study
Improving Vending Machine Profitability with the Internet of Things (IoT)
The vending industry is undergoing a sea change, taking advantage of new technologies to go beyond just delivering snacks to creating a new retail location. Intelligent vending machines can be found in many public locations as well as company facilities, selling different types of goods and services, including even computer accessories, gold bars, tickets, and office supplies. With increasing sophistication, they may also provide time- and location-based data pertaining to sales, inventory, and customer preferences. But at the end of the day, vending machine operators know greater profitability is driven by higher sales and lower operating costs.
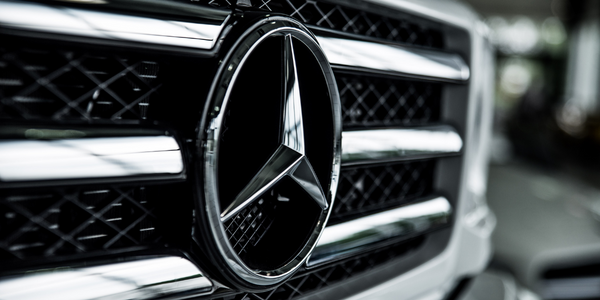
Case Study
Integral Plant Maintenance
Mercedes-Benz and his partner GAZ chose Siemens to be its maintenance partner at a new engine plant in Yaroslavl, Russia. The new plant offers a capacity to manufacture diesel engines for the Russian market, for locally produced Sprinter Classic. In addition to engines for the local market, the Yaroslavl plant will also produce spare parts. Mercedes-Benz Russia and his partner needed a service partner in order to ensure the operation of these lines in a maintenance partnership arrangement. The challenges included coordinating the entire maintenance management operation, in particular inspections, corrective and predictive maintenance activities, and the optimizing spare parts management. Siemens developed a customized maintenance solution that includes all electronic and mechanical maintenance activities (Integral Plant Maintenance).
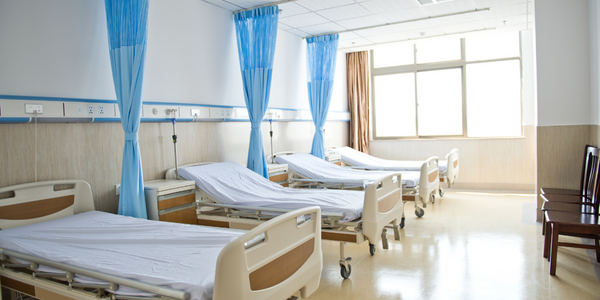
Case Study
Hospital Inventory Management
The hospital supply chain team is responsible for ensuring that the right medical supplies are readily available to clinicians when and where needed, and to do so in the most efficient manner possible. However, many of the systems and processes in use at the cancer center for supply chain management were not best suited to support these goals. Barcoding technology, a commonly used method for inventory management of medical supplies, is labor intensive, time consuming, does not provide real-time visibility into inventory levels and can be prone to error. Consequently, the lack of accurate and real-time visibility into inventory levels across multiple supply rooms in multiple hospital facilities creates additional inefficiency in the system causing over-ordering, hoarding, and wasted supplies. Other sources of waste and cost were also identified as candidates for improvement. Existing systems and processes did not provide adequate security for high-cost inventory within the hospital, which was another driver of cost. A lack of visibility into expiration dates for supplies resulted in supplies being wasted due to past expiry dates. Storage of supplies was also a key consideration given the location of the cancer center’s facilities in a dense urban setting, where space is always at a premium. In order to address the challenges outlined above, the hospital sought a solution that would provide real-time inventory information with high levels of accuracy, reduce the level of manual effort required and enable data driven decision making to ensure that the right supplies were readily available to clinicians in the right location at the right time.