Giant Eagle Reduces Costs and Increases Customer Value with Manhattan Solutions
公司规模
1,000+
地区
- America
国家
- United States
产品
- Manhattan Transportation Planning & Execution
- Manhattan Warehouse Management
- Manhattan Labor Management
- Manhattan Extended Enterprise Management
- Vocollect Voice
技术栈
- RF Technology
- Voice Technology
实施规模
- Enterprise-wide Deployment
影响指标
- Cost Savings
- Customer Satisfaction
- Productivity Improvements
技术
- 功能应用 - 运输管理系统 (TMS)
- 功能应用 - 仓库管理系统 (WMS)
适用行业
- 食品与饮料
- 零售
适用功能
- 物流运输
- 仓库和库存管理
用例
- 车队管理
- 库存管理
- 预测性维护
- 仓库自动化
服务
- 软件设计与工程服务
- 系统集成
关于客户
Giant Eagle is a prominent food retailer and distributor in the United States, headquartered in Pittsburgh, PA. The company operates 221 supermarkets and 140 fuel and convenience stores across Pennsylvania, Ohio, West Virginia, and Maryland. Each store offers between 20,000 and 60,000 items, including over 7,000 products under the company's own brands program. Giant Eagle also manages five distribution centers, ranging from 90,000 to 800,000 square feet, to support its extensive retail operations. Known for its commitment to customer value and operational efficiency, Giant Eagle employs the Toyota Production System methodology to enhance overall efficiencies by considering customers, quality, and people. The company sought to modernize its supply chain operations to reduce costs and improve its customer value proposition.
挑战
Giant Eagle, one of the largest food retailers and distributors in the U.S., was facing significant challenges due to outdated batch technology and multiple systems spread across various locations. The company needed to reduce costs and improve its customer value proposition. With 221 supermarkets and 140 fuel and convenience stores, Giant Eagle's operations were complex, involving five distribution centers ranging from 90,000 to 800,000 square feet. The existing systems had reached their maximum efficiency, and the company sought a single vendor to meet all its supply chain requirements, including advanced functionalities like flow-through order processing, put-to-store picking, and expanded RF and voice functions. Giant Eagle interviewed over 10 companies and shortlisted four vendors for detailed demonstrations. The company needed a partner with a solid understanding of the grocery industry and the capability to develop grocery-specific functionalities.
解决方案
Giant Eagle chose Manhattan's suite of solutions, including Transportation Planning & Execution, Warehouse Management, Labor Management, and Extended Enterprise Management, to overhaul its supply chain operations. The implementation strategy focused on deploying Warehouse Management and Labor Management at the most complex facilities first, followed by a rollout to other facilities. A dedicated team from Giant Eagle and Manhattan co-developed advanced grocery-specific capabilities such as enhanced code dating, advanced directed putaway options, real-time tasking, and put-to-store functionality. These solutions enabled real-time replenishment priority bumping, ensuring products were at the pick slot at the right time, thereby reducing skipped picks and order shorts. Labor Management was integrated into every facility, leveraging existing labor standards to improve productivity. The Manhattan solutions also enhanced the capabilities of Giant Eagle's Vocollect Voice system, streamlining operations across all five distribution centers. The solutions covered various functions, including RF receiving, directed putaway, directed replenishment, voice selection, RF loading, put-to-store, trading partner management, labor management, and advanced reporting.
运营影响
数量效益
Case Study missing?
Start adding your own!
Register with your work email and create a new case study profile for your business.
相关案例.

Case Study
The Kellogg Company
Kellogg keeps a close eye on its trade spend, analyzing large volumes of data and running complex simulations to predict which promotional activities will be the most effective. Kellogg needed to decrease the trade spend but its traditional relational database on premises could not keep up with the pace of demand.

Case Study
HEINEKEN Uses the Cloud to Reach 10.5 Million Consumers
For 2012 campaign, the Bond promotion, it planned to launch the campaign at the same time everywhere on the planet. That created unprecedented challenges for HEINEKEN—nowhere more so than in its technology operation. The primary digital content for the campaign was a 100-megabyte movie that had to play flawlessly for millions of viewers worldwide. After all, Bond never fails. No one was going to tolerate a technology failure that might bruise his brand.Previously, HEINEKEN had supported digital media at its outsourced datacenter. But that datacenter lacked the computing resources HEINEKEN needed, and building them—especially to support peak traffic that would total millions of simultaneous hits—would have been both time-consuming and expensive. Nor would it have provided the geographic reach that HEINEKEN needed to minimize latency worldwide.
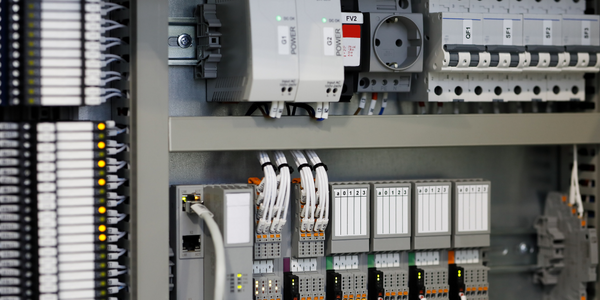
Case Study
Improving Production Line Efficiency with Ethernet Micro RTU Controller
Moxa was asked to provide a connectivity solution for one of the world's leading cosmetics companies. This multinational corporation, with retail presence in 130 countries, 23 global braches, and over 66,000 employees, sought to improve the efficiency of their production process by migrating from manual monitoring to an automatic productivity monitoring system. The production line was being monitored by ABB Real-TPI, a factory information system that offers data collection and analysis to improve plant efficiency. Due to software limitations, the customer needed an OPC server and a corresponding I/O solution to collect data from additional sensor devices for the Real-TPI system. The goal is to enable the factory information system to more thoroughly collect data from every corner of the production line. This will improve its ability to measure Overall Equipment Effectiveness (OEE) and translate into increased production efficiencies. System Requirements • Instant status updates while still consuming minimal bandwidth to relieve strain on limited factory networks • Interoperable with ABB Real-TPI • Small form factor appropriate for deployment where space is scarce • Remote software management and configuration to simplify operations

Case Study
Energy Management System at Sugar Industry
The company wanted to use the information from the system to claim under the renewable energy certificate scheme. The benefit to the company under the renewable energy certificates is Rs 75 million a year. To enable the above, an end-to-end solution for load monitoring, consumption monitoring, online data monitoring, automatic meter data acquisition which can be exported to SAP and other applications is required.
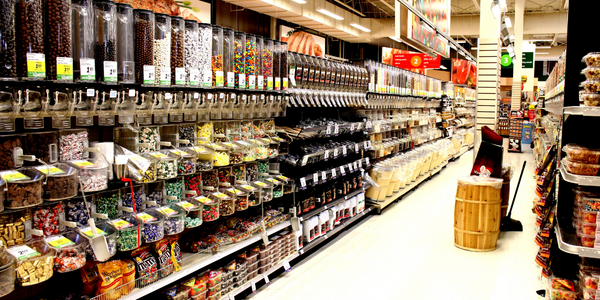
Case Study
How Sirqul’s IoT Platform is Crafting Carrefour’s New In-Store Experiences
Carrefour Taiwan’s goal is to be completely digital by end of 2018. Out-dated manual methods for analysis and assumptions limited Carrefour’s ability to change the customer experience and were void of real-time decision-making capabilities. Rather than relying solely on sales data, assumptions, and disparate systems, Carrefour Taiwan’s CEO led an initiative to find a connected IoT solution that could give the team the ability to make real-time changes and more informed decisions. Prior to implementing, Carrefour struggled to address their conversion rates and did not have the proper insights into the customer decision-making process nor how to make an immediate impact without losing customer confidence.