Enhancing Quality and Compliance Processes With a Global, Unified System
公司规模
200-1,000
地区
- America
- Asia
- Europe
国家
- China
- United Kingdom
- United States
产品
- Arena PLM
技术栈
- Cloud-based PLM
- Application Programming Interface (API)
实施规模
- Enterprise-wide Deployment
影响指标
- Customer Satisfaction
- Digital Expertise
- Productivity Improvements
技术
- 应用基础设施与中间件 - API 集成与管理
- 功能应用 - 产品生命周期管理系统 (PLM)
适用行业
- 航天
- 国家安全与国防
- 电信
适用功能
- 商业运营
- 产品研发
- 质量保证
用例
- 监管合规监控
- 远程协作
服务
- 云规划/设计/实施服务
- 系统集成
关于客户
Filtronic is a leading designer and manufacturer of radio frequency (RF), microwave, and mmWave technologies that transmit, receive, and condition radio signals for a range of challenging applications including telecommunications infrastructure, aerospace and defense, space, test and measurement, and critical communications. In the specialized field of RF technology, a leader and problem-solver like Filtronic must constantly look beyond the horizon and push boundaries to get their clients to market faster. Meeting challenging technological needs by developing repeatable, reliable, and compliant components and subsystems is critical to maintain their competitive edge.
挑战
As a global company with operations in the U.K. and U.S., Filtronic struggled with an internally developed product development tool. Tracking, maintaining, and releasing products was slow and inefficient. Filtronic had design, manufacturing, and quality silos that made it difficult for teams to see the interconnectedness of products, procedures, and documents. Managing compliance, audit actions, and corrective actions required cumbersome manual processes and constant human intervention. In Filtronic’s fast-paced development environment, there was zero tolerance for engineering design roadblocks, part issues, or regulatory compliance delays. In addition to solving these challenges, Filtronic wanted to focus on what they do best by eliminating their reliance on internal IT and engineering resources that were required to keep their homegrown tool afloat.
解决方案
Arena enables Filtronic’s dispersed teams to design, produce, and deliver innovative products quickly while tracking compliance. To be a truly global, one-stop manufacturing shop, Filtronic needed to reduce complexity and better control product design and supporting documentation in a single, unified platform. They selected Arena’s cloud-based PLM solution to streamline their complex product development processes and speed time to market in a highly competitive industry. Arena enables Filtronic to control the complete product record and make it accessible anytime and anywhere. Speed is critical and Rushton said, “if you’re slow—you’re already too late when you sell in fast-moving markets like telecom.” In China, the U.K., and the U.S., Filtronic employees are collaborating in real time with Arena to control and manage all drawings, procedures, and product documentation. Having revision-controlled information in one system gives all impacted teams a structured approach to manage parts, documents, and the entire product record effectively.
运营影响
数量效益
Case Study missing?
Start adding your own!
Register with your work email and create a new case study profile for your business.
相关案例.
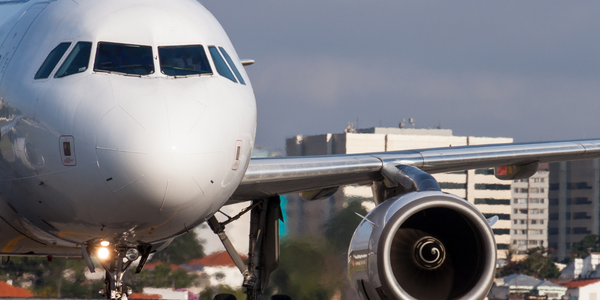
Case Study
Airbus Soars with Wearable Technology
Building an Airbus aircraft involves complex manufacturing processes consisting of thousands of moving parts. Speed and accuracy are critical to business and competitive advantage. Improvements in both would have high impact on Airbus’ bottom line. Airbus wanted to help operators reduce the complexity of assembling cabin seats and decrease the time required to complete this task.
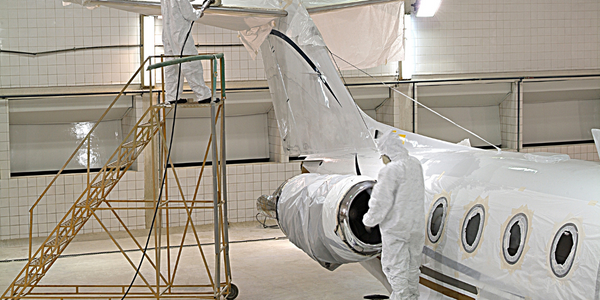
Case Study
Aircraft Predictive Maintenance and Workflow Optimization
First, aircraft manufacturer have trouble monitoring the health of aircraft systems with health prognostics and deliver predictive maintenance insights. Second, aircraft manufacturer wants a solution that can provide an in-context advisory and align job assignments to match technician experience and expertise.
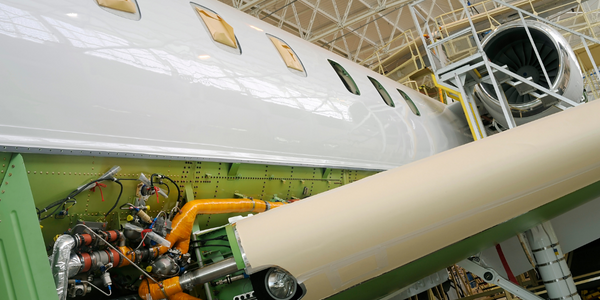
Case Study
Aerospace & Defense Case Study Airbus
For the development of its new wide-body aircraft, Airbus needed to ensure quality and consistency across all internal and external stakeholders. Airbus had many challenges including a very aggressive development schedule and the need to ramp up production quickly to satisfy their delivery commitments. The lack of communication extended design time and introduced errors that drove up costs.
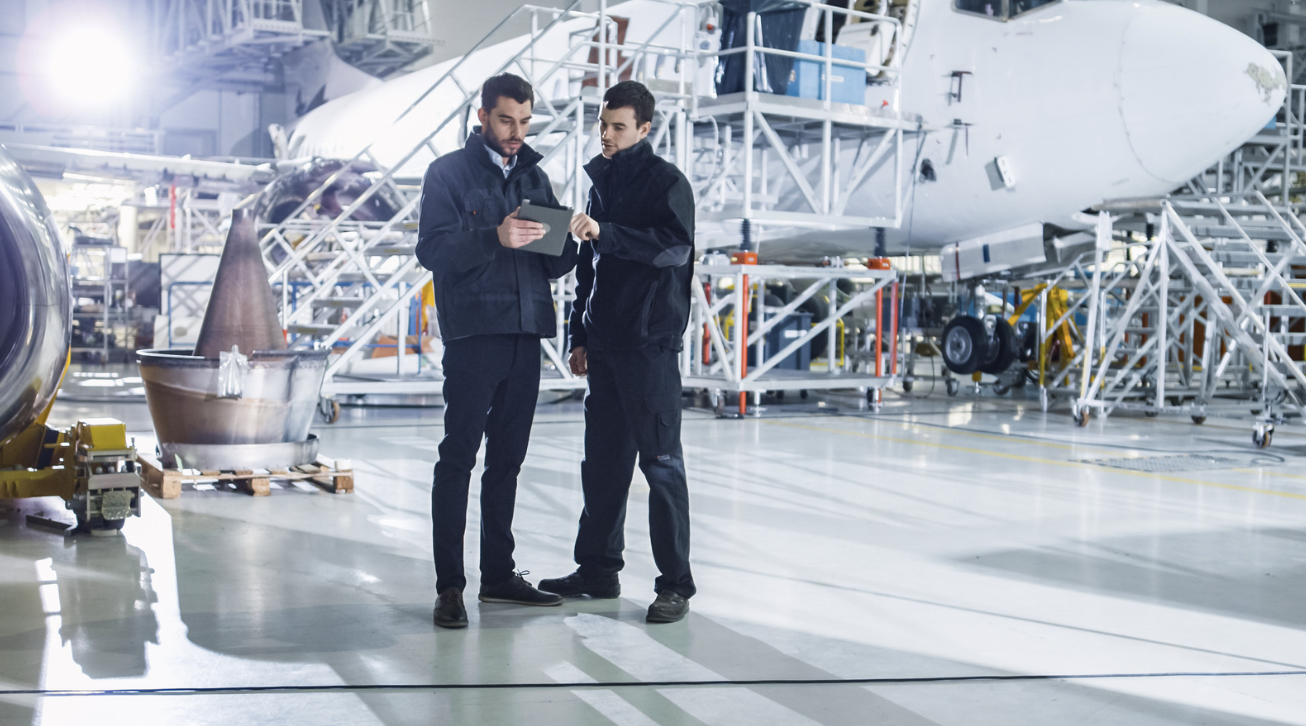
Case Study
Developing Smart Tools for the Airbus Factory
Manufacturing and assembly of aircraft, which involves tens of thousands of steps that must be followed by the operators, and a single mistake in the process could cost hundreds of thousands of dollars to fix, makes the room for error very small.
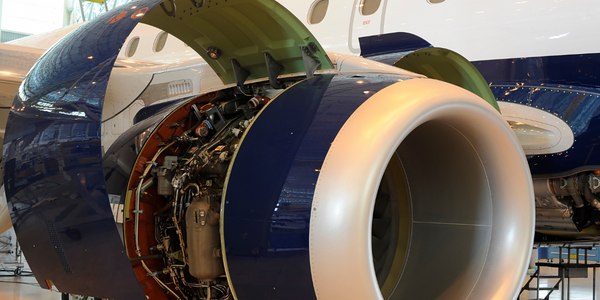
Case Study
Accelerate Production for Spirit AeroSystems
The manufacture and assembly of massive fuselage assemblies and other large structures generates a river of data. In fact, the bill of materials for a single fuselage alone can be millions of rows of data. In-house production processes and testing, as well as other manufacturers and customers created data flows that overwhelmed previous processes and information systems. Spirit’s customer base had grown substantially since their 2005 divestiture from Boeing, resulting in a $41 billion backlog of orders to fill. To address this backlog, meet increased customer demands and minimize additional capital investment, the company needed a way to improve throughput in the existing operational footprint. Spirit had a requirement from customers to increase fuselage production by 30%. To accomplish this goal, Spirit needed real-time information on its value chain and workflow. However, the two terabytes of data being pulled from their SAP ECC was unmanageable and overloaded their business warehouse. It had become time-consuming and difficult to pull aggregate data, disaggregate it for the needed information and then reassemble to create a report. During the 6-8 hours it took to build a report, another work shift (they run three per day) would have already taken place, thus the report content was out-of-date before it was ever delivered. As a result, supervisors often had to rely on manual efforts to provide charts, reports and analysis.