Customer Case Study
公司规模
200-1,000
地区
- Europe
国家
- United Kingdom
产品
- Priority ERP
技术栈
- Microsoft Technology
实施规模
- Enterprise-wide Deployment
影响指标
- Customer Satisfaction
- Digital Expertise
- Productivity Improvements
技术
- 应用基础设施与中间件 - 数据交换与集成
- 功能应用 - 企业资源规划系统 (ERP)
适用功能
- 流程制造
- 质量保证
- 仓库和库存管理
用例
- 库存管理
- 预测性维护
- 供应链可见性(SCV)
服务
- 软件设计与工程服务
- 系统集成
关于客户
BSC Diecasting & Finishing are a long established, well respected and highly innovative supplier of castings in the Midlands, UK. For over 45 years they have been refining their processes to deliver the best castings with the best finish to industry both in the UK & around the world. Their 24,000 ft facility features the latest diecasting equipment which they cast & finish hundreds of thousands of items for a wide variety of customers every year.
挑战
In order to streamline their operations and improve their customer service levels, BSC went on the search for a new IT system that would provide the following: • Totally integrated solution to cover all operations including the planning & execution of their manufacturing operations. • A configuration mechanism to allow the quoting of customers for new products & requoting for existing products. Accounting for cost changes & modifying the mark up. • “Quote to production in a click of a button”: Generating part numbers, BOMS & routings quickly through the configurator. • Stock management, traceability, managing sub contractors, labels printing & sales admin.
解决方案
Priority ERP was implemented to cover all areas of BSC Diecasting & Finishing's business, integrating all their operations within one seamless database. The solution consisted of the full standard manufacturing suite of Priority along with customizations to exactly fit BSC's business processes. Such customizations fit seamlessly into the product & are fully upgradeable through all new versions into the future without the need for BSC to invest further.
运营影响
数量效益
Case Study missing?
Start adding your own!
Register with your work email and create a new case study profile for your business.
相关案例.

Case Study
Remote Monitoring & Predictive Maintenance App for a Solar Energy System
The maintenance & tracking of various modules was an overhead for the customer due to the huge labor costs involved. Being an advanced solar solutions provider, they wanted to ensure early detection of issues and provide the best-in-class customer experience. Hence they wanted to automate the whole process.

Case Study
Remote Temperature Monitoring of Perishable Goods Saves Money
RMONI was facing temperature monitoring challenges in a cold chain business. A cold chain must be established and maintained to ensure goods have been properly refrigerated during every step of the process, making temperature monitoring a critical business function. Manual registration practice can be very costly, labor intensive and prone to mistakes.
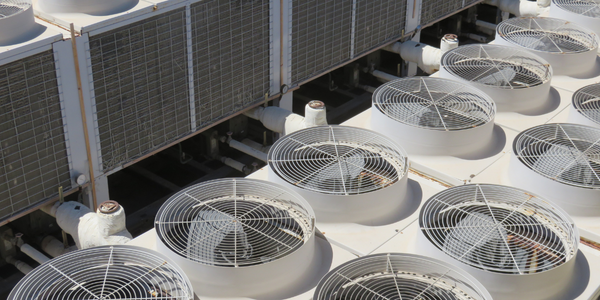
Case Study
Predictive Maintenance for Industrial Chillers
For global leaders in the industrial chiller manufacturing, reliability of the entire production process is of the utmost importance. Chillers are refrigeration systems that produce ice water to provide cooling for a process or industrial application. One of those leaders sought a way to respond to asset performance issues, even before they occur. The intelligence to guarantee maximum reliability of cooling devices is embedded (pre-alarming). A pre-alarming phase means that the cooling device still works, but symptoms may appear, telling manufacturers that a failure is likely to occur in the near future. Chillers who are not internet connected at that moment, provide little insight in this pre-alarming phase.
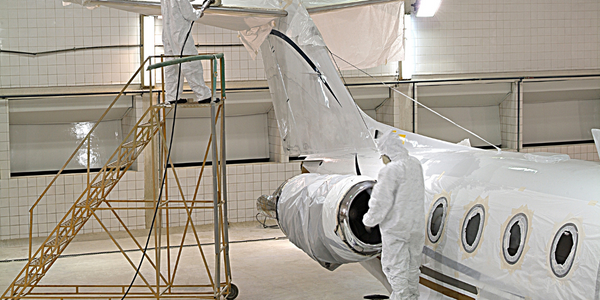
Case Study
Aircraft Predictive Maintenance and Workflow Optimization
First, aircraft manufacturer have trouble monitoring the health of aircraft systems with health prognostics and deliver predictive maintenance insights. Second, aircraft manufacturer wants a solution that can provide an in-context advisory and align job assignments to match technician experience and expertise.
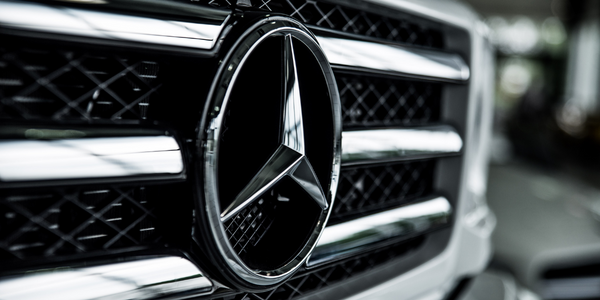
Case Study
Integral Plant Maintenance
Mercedes-Benz and his partner GAZ chose Siemens to be its maintenance partner at a new engine plant in Yaroslavl, Russia. The new plant offers a capacity to manufacture diesel engines for the Russian market, for locally produced Sprinter Classic. In addition to engines for the local market, the Yaroslavl plant will also produce spare parts. Mercedes-Benz Russia and his partner needed a service partner in order to ensure the operation of these lines in a maintenance partnership arrangement. The challenges included coordinating the entire maintenance management operation, in particular inspections, corrective and predictive maintenance activities, and the optimizing spare parts management. Siemens developed a customized maintenance solution that includes all electronic and mechanical maintenance activities (Integral Plant Maintenance).
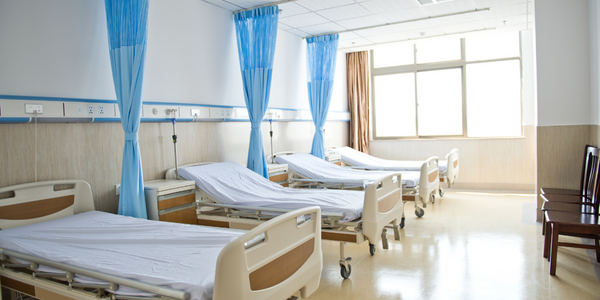
Case Study
Hospital Inventory Management
The hospital supply chain team is responsible for ensuring that the right medical supplies are readily available to clinicians when and where needed, and to do so in the most efficient manner possible. However, many of the systems and processes in use at the cancer center for supply chain management were not best suited to support these goals. Barcoding technology, a commonly used method for inventory management of medical supplies, is labor intensive, time consuming, does not provide real-time visibility into inventory levels and can be prone to error. Consequently, the lack of accurate and real-time visibility into inventory levels across multiple supply rooms in multiple hospital facilities creates additional inefficiency in the system causing over-ordering, hoarding, and wasted supplies. Other sources of waste and cost were also identified as candidates for improvement. Existing systems and processes did not provide adequate security for high-cost inventory within the hospital, which was another driver of cost. A lack of visibility into expiration dates for supplies resulted in supplies being wasted due to past expiry dates. Storage of supplies was also a key consideration given the location of the cancer center’s facilities in a dense urban setting, where space is always at a premium. In order to address the challenges outlined above, the hospital sought a solution that would provide real-time inventory information with high levels of accuracy, reduce the level of manual effort required and enable data driven decision making to ensure that the right supplies were readily available to clinicians in the right location at the right time.