公司规模
Large Corporate
地区
- America
国家
- United States
产品
- Domo
- AirPortal®
技术栈
- Data Aggregation
- Real-time Dashboard
- Business Reporting
实施规模
- Enterprise-wide Deployment
影响指标
- Customer Satisfaction
- Productivity Improvements
技术
- 分析与建模 - 实时分析
适用功能
- 销售与市场营销
用例
- 供应链可见性(SCV)
- 需求计划与预测
服务
- 数据科学服务
- 系统集成
关于客户
Christopherson Business Travel 是一家旅游管理公司,专注于旅游技术和优质客户服务。该公司被《Business Travel News》评为美国第 11 大商务旅行社。Christopherson 在五个提供全方位服务的地点开展业务,2016 年为全国 900 多家公司和组织预订了超过 6 亿美元的旅行。该公司开发了自己的专有商务旅行软件 AirPortal®。
挑战
旅行管理公司 Christopherson Business Travel 的专有商务旅行软件 AirPortal® 面临挑战。由于任何时候都有数百万笔交易通过其系统,该公司希望找到一种方法来汇总实时仪表板上的数据。这将使客户和内部员工更好地了解他们如何花费旅行预算。该公司需要汇总来自多个来源和输入的数据,并希望整合业务报告结构。
解决方案
Christopherson 向其客户经理推出了 Domo,以便与客户分享与他们的消费和旅行习惯相关的定制卡片。这有助于客户做出更好的决策,改善整体客户体验,并提高所提供的旅行分析的质量。客户现在无需使用基本的旅行管理报告系统,而是可以访问丰富的数据,而这些数据是他们无法通过 Christopherson 和 Domo 以外的任何地方获得的。客户可以查看员工正在使用的航空公司、汽车租赁和连锁酒店的平均预订率,以及允许进行综合报告的详细指标。然后,Christopherson 可以利用这些数据,代表其客户与供应商协商折扣。
运营影响
Case Study missing?
Start adding your own!
Register with your work email and create a new case study profile for your business.
相关案例.

Case Study
Remote Temperature Monitoring of Perishable Goods Saves Money
RMONI was facing temperature monitoring challenges in a cold chain business. A cold chain must be established and maintained to ensure goods have been properly refrigerated during every step of the process, making temperature monitoring a critical business function. Manual registration practice can be very costly, labor intensive and prone to mistakes.
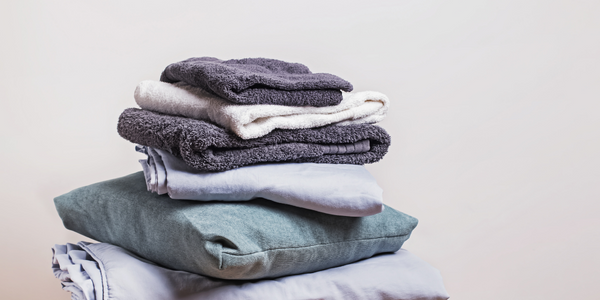
Case Study
Retail Uses RFID to Enable Cold Chain Monitoring
Like most grocery retailers, Hy-Vee is faced with the challenge of providing the highest quality products to its shoppers. Shoppers want the longest possible shelf life from perishable products and expect a consistent product experience each time they shop. Controlling the quality of products sold leads to shopper loyalty, which is of paramount importance to the success of Hy-Vee. Before products arrive in stores, Hy-Vee's distribution centers (DCs) handle items including dairy products, fresh meats, seafood, deli items, produce and frozen goods, all of which have different temperature needs and sensitivities. During transit from suppliers to DCs, Hy-Vee has limited visibility and temperature management abilities due to large amount of supplier managed transportation. For instance, during a week-long transit, a supplier's carrier equipment may malfunction, causing an item to thaw and then refreeze once repairs are made. Hy-Vee sought help from TempTRIP, an RFID solution provider that focuses on shipping, storage, receiving, and temperature control. TempTRIP's EPC RFID tags use Impinj chips to monitor and report temperature readings throughout the shipping and receiving process. The tags can also be re-configured and re-used, a unique feature within the current market of temperature monitoring devices.
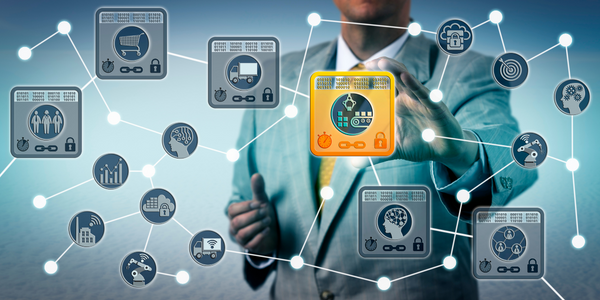
Case Study
Covisint Improves Mitsubishi's Collaboration With Its Supply Chain
Mitsubishi sought to improve supplier relationships on a global basis and to offer an easy-to-use solution to interact with them. In August 2004, Mitsubishi selected Covisint’s platform to help improve sharing of information and collaborative business processes with its global suppliers. Covisint enabled Mitsubishi to provide its suppliers with immediate access to information and applications to obtain more collaborative working relationships