BluJay Solutions Provides Contech a Robust Transportation Management System with Clear Visibility
公司规模
1,000+
地区
- America
国家
- United States
产品
- BluJay Transportation Management System
技术栈
- SaaS-based solution
- Service-oriented architecture
实施规模
- Enterprise-wide Deployment
影响指标
- Cost Savings
- Customer Satisfaction
- Productivity Improvements
技术
- 功能应用 - 运输管理系统 (TMS)
- 平台即服务 (PaaS) - 连接平台
适用行业
- 建筑与基础设施
- 运输
适用功能
- 商业运营
- 物流运输
用例
- 车队管理
- 过程控制与优化
- 供应链可见性(SCV)
服务
- 软件设计与工程服务
- 系统集成
关于客户
Contech® Engineered Solutions provides site solutions for the civil engineering industry. Contech’s portfolio includes bridges, drainage, erosion control, retaining wall, sanitary and storm, and wastewater treatment products. Its products provide effective solutions for projects with a variety of loading conditions, foundation requirements, soil and water environments, and varied installation demands. Contech has office locations in all 50 states and third-party distributors in every major U.S. city. The company moves approximately 80,000 truckloads per year, which involves more than 1,000 carriers.
挑战
Contech needed to easily implement a robust transportation management system that provides good overall functionality, including ease of use, and excellent tender and freight payment visibility. They were looking to improve in the following areas: transportation was managed manually via spreadsheets, the freight accrual process was difficult, and freight audit and payment were split between Contech and a third-party freight payment service. Additionally, transportation data was limited to freight payment data.
解决方案
Contech chose BluJay’s Transportation Management because it provides transportation planning, shipment, financial settlement, and tracking visibility through a SaaS-based solution. Based on collaborative workflows on a service-oriented architecture, the BluJay Solutions Transportation Management System makes it easier for shippers such as Contech and its carriers to manage all modes of transportation. Contech uses a standard costing system to measure increases and decreases in spending, which has been a boon to the bottom line. BluJay’s Transportation Management has eliminated the manual process of tendering, thus automating the procedure with both contracted carriers and tenders via a bid system. BluJay’s Transportation Management enabled Contech to more easily deal with virtually any kind of carrier contract. Due to a large number of carriers, rate structures and contracts vary based on routes and mode of transportation. For example, the company manages short hauls with dedicated carrier contracts and long hauls with the bid process. When a carrier uses BluJay’s Transportation Management to accept a load from Contech, both parties know the exact rates involved. Therefore, when Contech receives the freight bill, it’s easy to verify the invoice’s accuracy and to manage practically any additional assessorial charges quickly and more easily.
运营影响
数量效益
Case Study missing?
Start adding your own!
Register with your work email and create a new case study profile for your business.
相关案例.

Case Study
IoT System for Tunnel Construction
The Zenitaka Corporation ('Zenitaka') has two major business areas: its architectural business focuses on structures such as government buildings, office buildings, and commercial facilities, while its civil engineering business is targeted at structures such as tunnels, bridges and dams. Within these areas, there presented two issues that have always persisted in regard to the construction of mountain tunnels. These issues are 'improving safety" and "reducing energy consumption". Mountain tunnels construction requires a massive amount of electricity. This is because there are many kinds of electrical equipment being used day and night, including construction machinery, construction lighting, and ventilating fan. Despite this, the amount of power consumption is generally not tightly managed. In many cases, the exact amount of power consumption is only ascertained when the bill from the power company becomes available. Sometimes, corporations install demand-monitoring equipment to help curb the maximum power demanded. However, even in these cases, the devices only allow the total volume of power consumption to be ascertained, or they may issue warnings to prevent the contracted volume of power from being exceeded. In order to tackle the issue of reducing power consumption, it was first necessary to obtain an accurate breakdown of how much power was being used in each particular area. In other words, we needed to be able to visualize the amount of power being consumed. Safety, was also not being managed very rigorously. Even now, tunnel construction sites often use a 'name label' system for managing entry into the work site. Specifically, red labels with white reverse sides that bear the workers' names on both sides are displayed at the tunnel work site entrance. The workers themselves then flip the name label to the appropriate side when entering or exiting from the work site to indicate whether or not they are working inside the tunnel at any given time. If a worker forgets to flip his or her name label when entering or exiting from the tunnel, management cannot be performed effectively. In order to tackle the challenges mentioned above, Zenitaka decided to build a system that could improve the safety of tunnel construction as well as reduce the amount of power consumed. In other words, this new system would facilitate a clear picture of which workers were working in each location at the mountain tunnel construction site, as well as which processes were being carried out at those respective locations at any given time. The system would maintain the safety of all workers while also carefully controlling the electrical equipment to reduce unnecessary power consumption. Having decided on the concept, our next concern was whether there existed any kind of robust hardware that would not break down at the construction work site, that could move freely in response to changes in the working environment, and that could accurately detect workers and vehicles using radio frequency identification (RFID). Given that this system would involve many components that were new to Zenitaka, we decided to enlist the cooperation of E.I.Sol Co., Ltd. ('E.I.Sol') as our joint development partner, as they had provided us with a highly practical proposal.
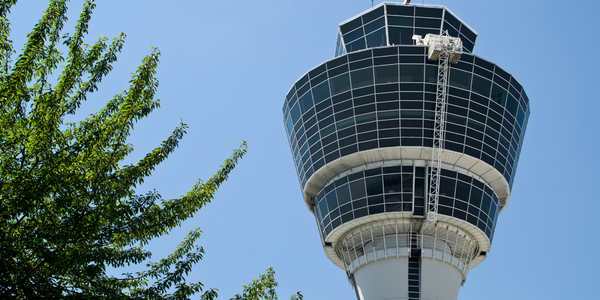
Case Study
Airport SCADA Systems Improve Service Levels
Modern airports are one of the busiest environments on Earth and rely on process automation equipment to ensure service operators achieve their KPIs. Increasingly airport SCADA systems are being used to control all aspects of the operation and associated facilities. This is because unplanned system downtime can cost dearly, both in terms of reduced revenues and the associated loss of customer satisfaction due to inevitable travel inconvenience and disruption.
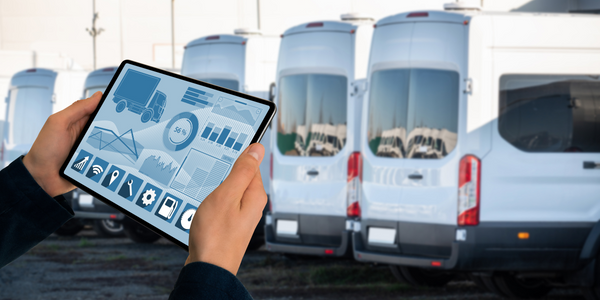
Case Study
IoT-based Fleet Intelligence Innovation
Speed to market is precious for DRVR, a rapidly growing start-up company. With a business model dependent on reliable mobile data, managers were spending their lives trying to negotiate data roaming deals with mobile network operators in different countries. And, even then, service quality was a constant concern.
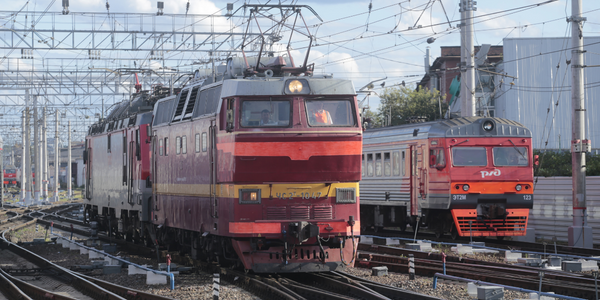
Case Study
Digitize Railway with Deutsche Bahn
To reduce maintenance costs and delay-causing failures for Deutsche Bahn. They need manual measurements by a position measurement system based on custom-made MEMS sensor clusters, which allow autonomous and continuous monitoring with wireless data transmission and long battery. They were looking for data pre-processing solution in the sensor and machine learning algorithms in the cloud so as to detect critical wear.
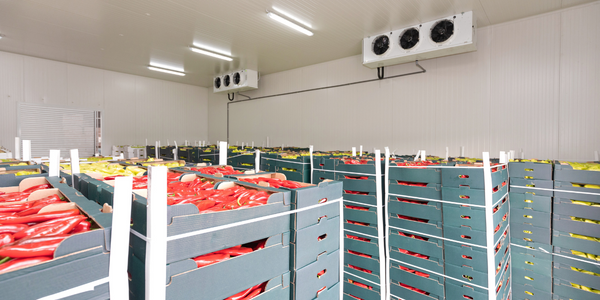
Case Study
Cold Chain Transportation and Refrigerated Fleet Management System
1) Create a digital connected transportation solution to retrofit cold chain trailers with real-time tracking and controls. 2) Prevent multi-million dollar losses due to theft or spoilage. 3) Deliver a digital chain-of-custody solution for door to door load monitoring and security. 4) Provide a trusted multi-fleet solution in a single application with granular data and access controls.
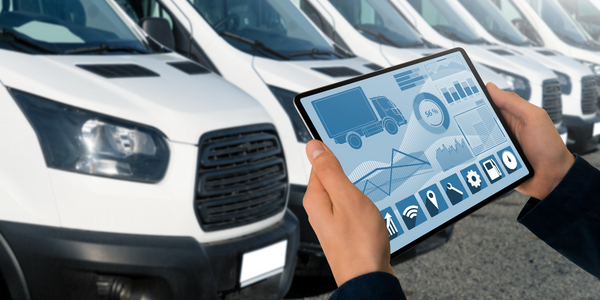
Case Study
Vehicle Fleet Analytics
Organizations frequently implement a maintenance strategy for their fleets of vehicles using a combination of time and usage based maintenance schedules. While effective as a whole, time and usage based schedules do not take into account driving patterns, environmental factors, and sensors currently deployed within the vehicle measuring crank voltage, ignition voltage, and acceleration, all of which have a significant influence on the overall health of the vehicle.In a typical fleet, a large percentage of road calls are related to electrical failure, with battery failure being a common cause. Battery failures result in unmet service agreement levels and costly re-adjustment of scheduled to provide replacement vehicles. To reduce the impact of unplanned maintenance, the transportation logistics company was interested in a trial of C3 Vehicle Fleet Analytics.