BAE Systems Puts People First: An iBASEt MES/Quality Customer Success Story
公司规模
Large Corporate
地区
- America
国家
- United States
- United Kingdom
产品
- iBASEt Digital Operations Suite
- iBASEt Manufacturing Execution System (MES)
- iBASEt Supplier Quality Management (SQM)
- iBASEt Maintenance, Repair, and Overhaul (MRO)
技术栈
- Cloud-native microservices architecture
- Open APIs
- Solumina platform
实施规模
- Enterprise-wide Deployment
影响指标
- Customer Satisfaction
- Productivity Improvements
- Digital Expertise
技术
- 功能应用 - 制造执行系统 (MES)
- 功能应用 - 企业资源规划系统 (ERP)
- 功能应用 - 产品生命周期管理系统 (PLM)
适用行业
- 航天
适用功能
- 质量保证
- 流程制造
用例
- 自动化制造系统
- 过程控制与优化
- 预测性维护
服务
- 系统集成
- 培训
- 软件设计与工程服务
关于客户
BAE Systems, plc, a British multinational conglomerate, is one of the largest Aerospace & Defense (A&D) companies in the world—the product of a 1999 merger between British Aerospace (BAe) and Marconi Electronic Systems. One of the company’s numerous global subdivisions is its U.S. based electronic systems division, which manufactures components and systems for the U.S. defense sector as well as various commercial industries. Much like its parent organization, the BAE Systems electronics systems division has a legacy of several mergers and acquisitions, which resulted in a heterogeneous culture with numerous and disparate locations. With divisions and subdivisions all over the world, keeping their business running smoothly can be complicated.
挑战
When it came to change management in its US-based electronic systems division, BAE faced a major challenge. Numerous physical locations, heterogenous work culture, and over 10,000 employees necessitated a streamlined solution for manufacturing execution. With such a large workforce across diverse locations and market sectors, BAE Systems quickly learned the importance of capturing the necessary engagement across functions within the project lifecycle, from the generation of requirements to scenario testing and gap identification to training and post go-live support.
解决方案
The company decided to move to a more gradual, incremental roll-out, starting with two smaller sites going live initially and followed by three remaining sites in the following six months. This phased approach allowed for a much greater real-time evaluation of the effectiveness of the project and flexibility for any necessary adjustments required. It also allowed extra people resources to be deployed in a concentrated fashion to devote to different phases of the project. The company set up a matrix of leaders covering functional areas across the project, including solution training, information training, supply chain integration, performance excellence, and especially—change management. By bringing in dedicated change management assistance, the company was able to gain a clearer view of the current and future-state organizational fabric and to better anticipate the impacts of project change on people and processes.
运营影响
数量效益
Case Study missing?
Start adding your own!
Register with your work email and create a new case study profile for your business.
相关案例.
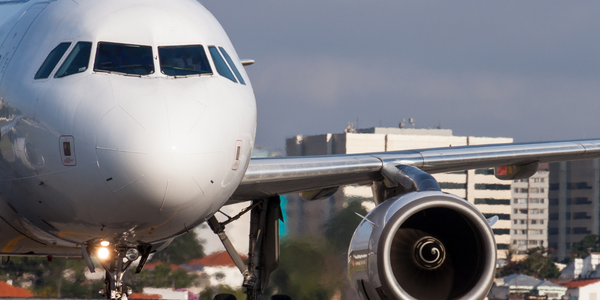
Case Study
Airbus Soars with Wearable Technology
Building an Airbus aircraft involves complex manufacturing processes consisting of thousands of moving parts. Speed and accuracy are critical to business and competitive advantage. Improvements in both would have high impact on Airbus’ bottom line. Airbus wanted to help operators reduce the complexity of assembling cabin seats and decrease the time required to complete this task.
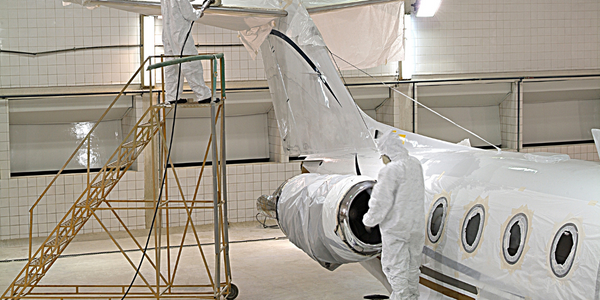
Case Study
Aircraft Predictive Maintenance and Workflow Optimization
First, aircraft manufacturer have trouble monitoring the health of aircraft systems with health prognostics and deliver predictive maintenance insights. Second, aircraft manufacturer wants a solution that can provide an in-context advisory and align job assignments to match technician experience and expertise.
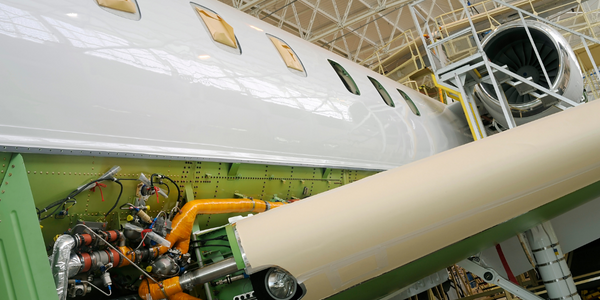
Case Study
Aerospace & Defense Case Study Airbus
For the development of its new wide-body aircraft, Airbus needed to ensure quality and consistency across all internal and external stakeholders. Airbus had many challenges including a very aggressive development schedule and the need to ramp up production quickly to satisfy their delivery commitments. The lack of communication extended design time and introduced errors that drove up costs.
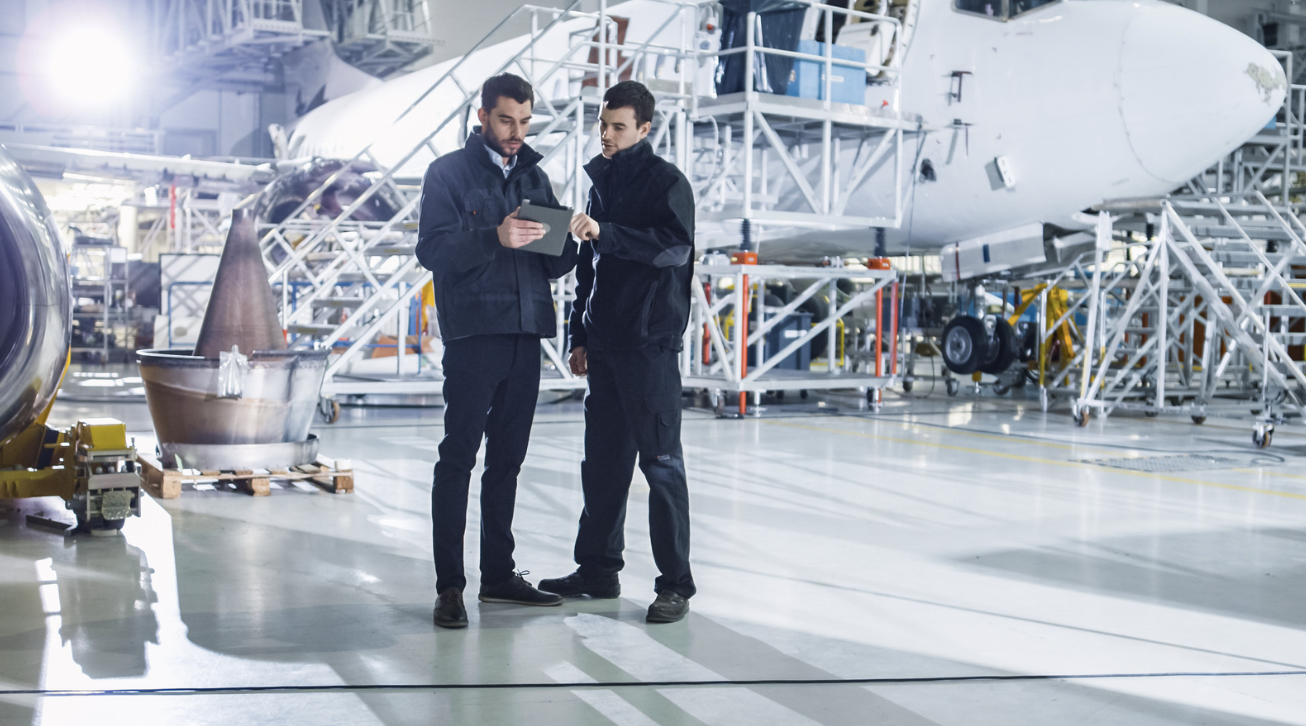
Case Study
Developing Smart Tools for the Airbus Factory
Manufacturing and assembly of aircraft, which involves tens of thousands of steps that must be followed by the operators, and a single mistake in the process could cost hundreds of thousands of dollars to fix, makes the room for error very small.
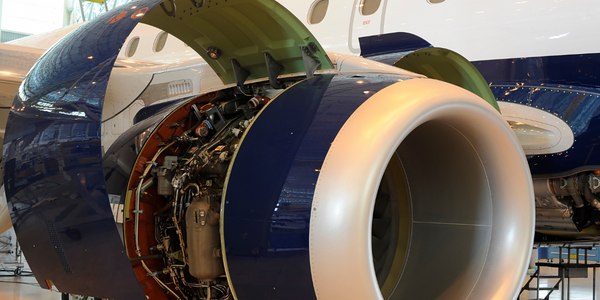
Case Study
Accelerate Production for Spirit AeroSystems
The manufacture and assembly of massive fuselage assemblies and other large structures generates a river of data. In fact, the bill of materials for a single fuselage alone can be millions of rows of data. In-house production processes and testing, as well as other manufacturers and customers created data flows that overwhelmed previous processes and information systems. Spirit’s customer base had grown substantially since their 2005 divestiture from Boeing, resulting in a $41 billion backlog of orders to fill. To address this backlog, meet increased customer demands and minimize additional capital investment, the company needed a way to improve throughput in the existing operational footprint. Spirit had a requirement from customers to increase fuselage production by 30%. To accomplish this goal, Spirit needed real-time information on its value chain and workflow. However, the two terabytes of data being pulled from their SAP ECC was unmanageable and overloaded their business warehouse. It had become time-consuming and difficult to pull aggregate data, disaggregate it for the needed information and then reassemble to create a report. During the 6-8 hours it took to build a report, another work shift (they run three per day) would have already taken place, thus the report content was out-of-date before it was ever delivered. As a result, supervisors often had to rely on manual efforts to provide charts, reports and analysis.