Australian Railway Leader Reduces Labor Costs by 80% and Easily Passes Safety Audits After Partnering with Avetta
公司规模
1,000+
地区
- Pacific
国家
- Australia
产品
- Avetta
技术栈
- Risk Management
- Reporting & Dashboards
- Supply Chain Management
实施规模
- Enterprise-wide Deployment
影响指标
- Cost Savings
- Customer Satisfaction
- Employee Satisfaction
- Productivity Improvements
技术
- 分析与建模 - 预测分析
- 功能应用 - 企业资源规划系统 (ERP)
- 功能应用 - 远程监控系统
适用行业
- 铁路与地铁
- 运输
适用功能
- 维护
- 采购
- 质量保证
用例
- 预测性维护
- 远程资产管理
- 供应链可见性(SCV)
服务
- 系统集成
- 培训
关于客户
This railway leader operates a fleet of 407 three-car train sets over 837 kilometers of track, providing over 14,000 services each week and carries 415,000 passengers each weekday. Over the course of a year, its train fleet travels 30 million kilometers and provides more than 228 million customer boardings. The company is a metropolitan passenger rail network franchise in Australia, responsible for safely transporting citizens to and from work each day. Safety is a top priority, touching all aspects of the organization, including the construction and maintenance of trains, stations, and tracks. The company manages a large supply chain, including 3,500 contractors, to ensure that all work is performed safely and efficiently. The organization faced challenges in managing this extensive supply chain, particularly in prequalifying and overseeing contractors and suppliers. The lack of proper oversight and inefficient manual processes led to significant issues, including a failed audit by the Federal Safety Commissioner. This prompted the company to seek a comprehensive solution to improve supply chain management, ensure compliance, and enhance overall safety and efficiency.
挑战
For a metropolitan passenger rail network franchise in Australia, managing the supply chain is about more than bringing efficiency to the process or finding ways to save money. Although those goals are certainly important, the company’s primary responsibility is safely carrying the citizens to and from work each day. More than 415,000 passengers use the rail every weekday, and getting them to their destination safely, and on time, is the highest priority. Safety touches all aspects of the organization, including construction and maintenance of every train it operates, every station in the system, and every kilometer of track it lays. Since much of that work is done by contractors and suppliers, the railway leader needs to know that each of them are qualified to perform the work for which they’re hired. It’s important that suppliers deliver the service at a competitive price, but it’s vital that they meet environmental and safety requirements. For this company, supply chain management has enormous implications for passenger safety and service. Nevertheless, qualifying and managing some 3,500 contractors was a massive job that the organization simply wasn’t adequately staffed for. That was the stark conclusion of its Supply Development & Performance Manager when he stepped into a procurement role for the company. While reviewing the procurement process, he discovered that management of the supply chain—including prequalification of contractors and suppliers—wasn’t being performed properly. Responsibility for selecting and introducing new suppliers was largely handled by superintendents in the field. The lack of careful oversight hit a critical point—and came to the attention of the executive staff— in October 2013. That’s when the office of the Federal Safety Commissioner audited one of the organization’s business units—the group responsible for new stations, sections of mainline, and other construction projects. The audit of this group’s contract management process failed across the board, receiving one point out of 100. This was a key catalyst for change within the organization and provided incentive to revamp the way it managed contractors and suppliers. The problem wasn’t simply a lack of oversight. To the degree that the company prequalified and managed its supply chain, the process was simply inefficient. The prequalification process was a basic, manual, and labor-intensive process. It relied on paper records, was handled entirely in-house, and lacked the automation necessary to efficiently manage thousands of third-party workers. Various people across the company spent a good deal of time on this process. And because it was difficult to share information, there was a lot of duplication, both internally and within the supplier community.
解决方案
In exploring supply chain risk management solutions, the internal team was thinking beyond problem-solving. They knew they had to correct certain deficiencies—fix the prequalification process, ensure compliance, modernize the procurement process and so on—but they also had a larger vision for the solution. Effective management of the supply chain was considered critical for passenger safety as well as the growth and agility of the organization. Moreover, while the company itself was growing, its parent company was also on the verge of landing its second franchise in Australia, serving another large city. This metro system would require the same careful management of its supply chain, and could leverage this solution—if it worked. The organization’s vision for supply chain risk management included all of the rail industry. The rail network franchise felt it could help propel the industry into the 21st century with respect to procurement and supplier management. This idea of developing a “rail sector solution” was discussed with every supply chain risk management vendor that the company approached. Avetta was the only company willing to work with them to develop more functionality in a long-term, collaborative approach to the product. This openness to the idea of a collaboration was an important reason the team chose Avetta for its supply chain risk management solution. Ease of use was another key differentiator of the Avetta solution. The company wanted a solution that end users would actually use. The organization found the Avetta solutions to be very accessible, very easy to use, especially from the users’ point of view. In addition, Avetta provided other core capabilities and functionality that were needed, including reporting, dashboards, and risk management. Of the five vendors considered, Avetta met the broadest range of requirements. After a rigorous process and proper due diligence, the company selected Avetta in the summer of 2014 and went live with the solution by September. Avetta supported the go-live process by collaborating with the railways leader to inform contractors and suppliers about the new system. Avetta called each one, sent out an initial mailing and worked with the internal team on program education. This “two-pronged attack,” with efforts by both companies, helped underscore the importance of the initiative and led to a faster sign-up rate. It also reinforced the collaborative approach so important to the organization.
运营影响
数量效益
Case Study missing?
Start adding your own!
Register with your work email and create a new case study profile for your business.
相关案例.
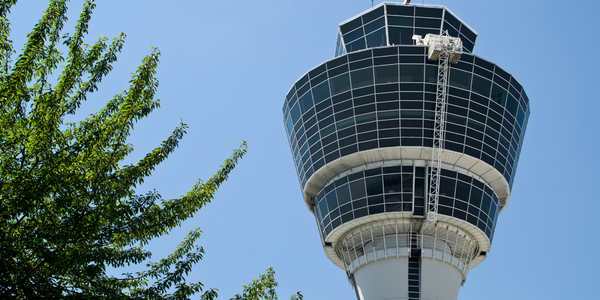
Case Study
Airport SCADA Systems Improve Service Levels
Modern airports are one of the busiest environments on Earth and rely on process automation equipment to ensure service operators achieve their KPIs. Increasingly airport SCADA systems are being used to control all aspects of the operation and associated facilities. This is because unplanned system downtime can cost dearly, both in terms of reduced revenues and the associated loss of customer satisfaction due to inevitable travel inconvenience and disruption.
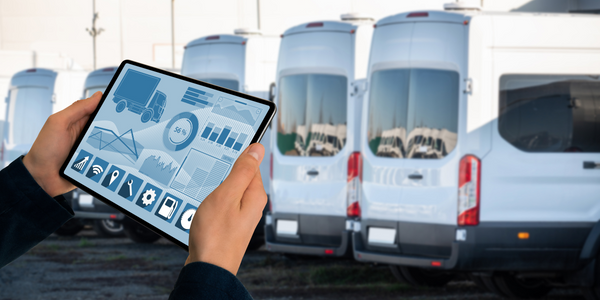
Case Study
IoT-based Fleet Intelligence Innovation
Speed to market is precious for DRVR, a rapidly growing start-up company. With a business model dependent on reliable mobile data, managers were spending their lives trying to negotiate data roaming deals with mobile network operators in different countries. And, even then, service quality was a constant concern.
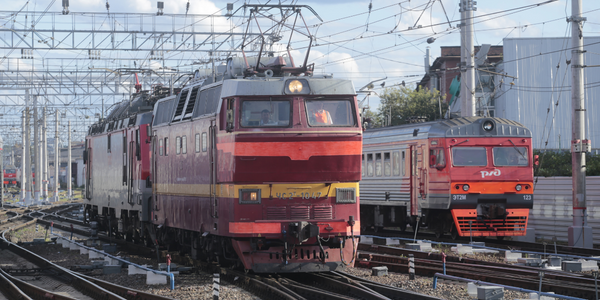
Case Study
Digitize Railway with Deutsche Bahn
To reduce maintenance costs and delay-causing failures for Deutsche Bahn. They need manual measurements by a position measurement system based on custom-made MEMS sensor clusters, which allow autonomous and continuous monitoring with wireless data transmission and long battery. They were looking for data pre-processing solution in the sensor and machine learning algorithms in the cloud so as to detect critical wear.
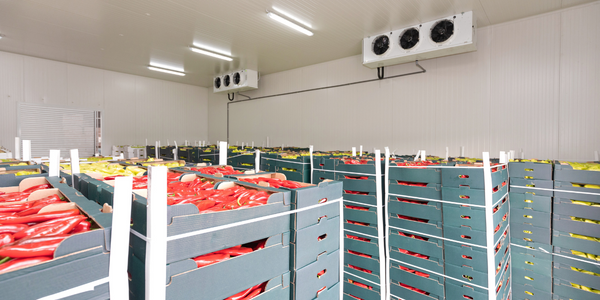
Case Study
Cold Chain Transportation and Refrigerated Fleet Management System
1) Create a digital connected transportation solution to retrofit cold chain trailers with real-time tracking and controls. 2) Prevent multi-million dollar losses due to theft or spoilage. 3) Deliver a digital chain-of-custody solution for door to door load monitoring and security. 4) Provide a trusted multi-fleet solution in a single application with granular data and access controls.
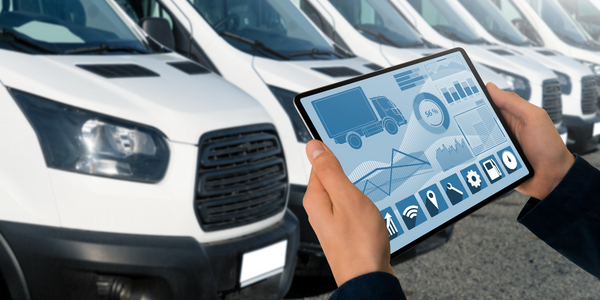
Case Study
Vehicle Fleet Analytics
Organizations frequently implement a maintenance strategy for their fleets of vehicles using a combination of time and usage based maintenance schedules. While effective as a whole, time and usage based schedules do not take into account driving patterns, environmental factors, and sensors currently deployed within the vehicle measuring crank voltage, ignition voltage, and acceleration, all of which have a significant influence on the overall health of the vehicle.In a typical fleet, a large percentage of road calls are related to electrical failure, with battery failure being a common cause. Battery failures result in unmet service agreement levels and costly re-adjustment of scheduled to provide replacement vehicles. To reduce the impact of unplanned maintenance, the transportation logistics company was interested in a trial of C3 Vehicle Fleet Analytics.
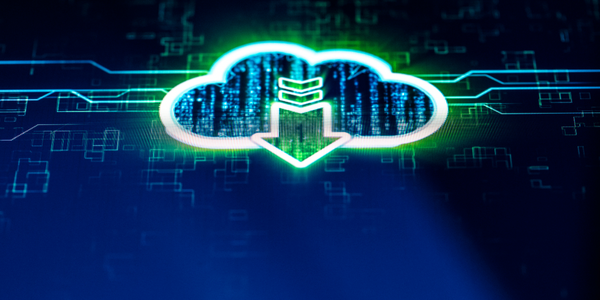
Case Study
3M Gains Real-Time Insight with Cloud Solution
The company has a long track record of innovative technology solutions. For example, 3M helps its customers optimize parking operations by automating fee collection and other processes. To improve support for this rapidly expanding segment, 3M needed to automate its own data collection and reporting. The company had recently purchased the assets of parking, tolling, and automatic license plate reader businesses, and required better insight into these acquisitions. Chad Reed, Global Business Manager for 3M Parking Systems, says, “With thousands of installations across the world, we couldn’t keep track of our software and hardware deployments, which made it difficult to understand our market penetration.” 3M wanted a tracking application that sales staff could use to get real-time information about the type and location of 3M products in parking lots and garages. So that it could be used on-site with potential customers, the solution would have to provide access to data anytime, anywhere, and from an array of mobile devices. Jason Fox, Mobile Application Architect at 3M, upped the ante by volunteering to deliver the new app in one weekend. For Fox and his team, these requirements meant turning to the cloud instead of an on-premises datacenter. “My first thought was to go directly to the cloud because we needed to provide access not only to our salespeople, but to resellers who didn’t have access to our internal network,” says Fox. “The cloud just seemed like a logical choice.”