Agile Industrial Robot Grippers with Topology Optimization & Metal 3D Printing
公司规模
Mid-size Company
地区
- Europe
国家
- Italy
产品
- nTopology
- Desktop Metal Studio System
技术栈
- Metal 3D Printing
- Topology Optimization
- Reusable Design Workflows
实施规模
- Enterprise-wide Deployment
影响指标
- Productivity Improvements
- Cost Savings
- Innovation Output
技术
- 功能应用 - 远程监控系统
- 分析与建模 - Generative AI
- 功能应用 - 制造执行系统 (MES)
适用行业
- 汽车
适用功能
- 流程制造
- 质量保证
用例
- 预测性维护
- 自动化制造系统
- 工厂可见化与智能化
服务
- 软件设计与工程服务
- 系统集成
关于客户
Preziosa Francesco SRL is a manufacturer of sheet metal cabinets based in Bergamo, Italy. The company has established itself as a leader in its field by investing in advanced manufacturing technologies, including a robotic cell and an automated press brake bending machine. These investments are crucial for maintaining their competitive edge and ensuring high-quality production. However, the company faced challenges with the long lead times associated with CNC machining custom robot grippers, which are essential for their automated processes. By partnering with Add-it and leveraging metal 3D printing, Preziosa Francesco SRL aimed to overcome these challenges and enhance their manufacturing capabilities.
挑战
Preziosa Francesco SRL faced a significant bottleneck in their automated press brake bending machine due to the long lead times of CNC machining new sets of custom robot grippers. This bottleneck threatened the efficiency and reliability of their robotic cell, which was a substantial investment. The challenge was to find a way to produce these grippers more quickly and reliably to ensure the smooth operation of their manufacturing process.
解决方案
To address the bottleneck, Preziosa Francesco SRL partnered with Add-it to move part production in-house using metal 3D printing. They utilized nTopology's software to create reusable design workflows, which allowed them to quickly generate custom grippers with optimized geometry. The engineers applied a honeycomb-like perforation pattern to the grippers to increase traction and reliability. Additionally, they used topology optimization to design more agile grippers with a smaller footprint, enhancing the robot's safe zone and process repeatability. This approach not only improved the reliability of the bending process but also enabled lights-out manufacturing and full utilization of their robotic system.
运营影响
数量效益
Case Study missing?
Start adding your own!
Register with your work email and create a new case study profile for your business.
相关案例.
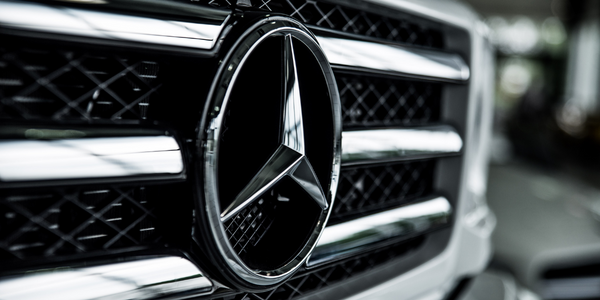
Case Study
Integral Plant Maintenance
Mercedes-Benz and his partner GAZ chose Siemens to be its maintenance partner at a new engine plant in Yaroslavl, Russia. The new plant offers a capacity to manufacture diesel engines for the Russian market, for locally produced Sprinter Classic. In addition to engines for the local market, the Yaroslavl plant will also produce spare parts. Mercedes-Benz Russia and his partner needed a service partner in order to ensure the operation of these lines in a maintenance partnership arrangement. The challenges included coordinating the entire maintenance management operation, in particular inspections, corrective and predictive maintenance activities, and the optimizing spare parts management. Siemens developed a customized maintenance solution that includes all electronic and mechanical maintenance activities (Integral Plant Maintenance).
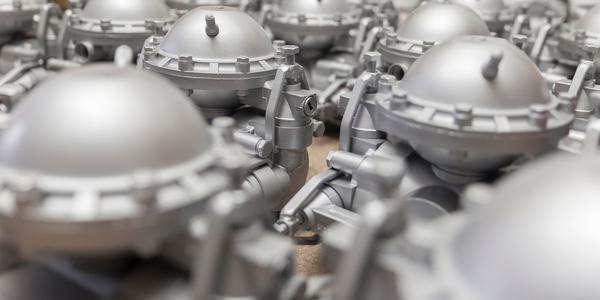
Case Study
Monitoring of Pressure Pumps in Automotive Industry
A large German/American producer of auto parts uses high-pressure pumps to deburr machined parts as a part of its production and quality check process. They decided to monitor these pumps to make sure they work properly and that they can see any indications leading to a potential failure before it affects their process.