Unilever's Demand Sensing and Inventory Optimisation with Terra Technology
Company Size
1,000+
Region
- America
- Asia
- Europe
Country
- India
- United States
Product
- Enterprise Demand Sensing Platform
- Multi-Enterprise Inventory Optimisation
- SAP Advanced Planner and Optimizer (APO)
Tech Stack
- Demand Sensing
- Inventory Optimisation
- SAP APO Integration
Implementation Scale
- Enterprise-wide Deployment
Impact Metrics
- Cost Savings
- Customer Satisfaction
- Environmental Impact Reduction
- Productivity Improvements
Technology Category
- Analytics & Modeling - Predictive Analytics
- Application Infrastructure & Middleware - Data Exchange & Integration
- Functional Applications - Inventory Management Systems
Applicable Industries
- Consumer Goods
- Retail
Use Cases
- Inventory Management
- Predictive Maintenance
- Supply Chain Visibility
Services
- Software Design & Engineering Services
- System Integration
About The Customer
Unilever is one of the largest FMCG manufacturers globally, with a presence in over 190 countries and a portfolio of more than 400 brands. The company serves 2 billion consumers daily and primarily uses SAP systems for its operations. Unilever's demand planning is maintained within SAP Advanced Planner and Optimizer (APO). The company has a significant global reach and is committed to sustainability and innovation in its supply chain processes.
The Challenge
Unilever faced significant challenges in managing its supply chain due to increasing volatility in the market. The company identified five key global trends impacting its operations: multiple channels, sustainability, economic volatility, customer intimacy, and digital savviness. To address these challenges, Unilever needed a more agile supply chain that could handle the growing volatility without resorting to expensive inventory increases. The company aimed to improve its short-term forecast accuracy and reduce working capital tied up in inventory.
The Solution
Unilever partnered with Terra Technology to implement demand sensing and inventory optimisation tools. Terra Technology's Enterprise Demand Sensing Platform automates and synchronises various demand signals to improve short-term forecast accuracy. The Multi-Enterprise Inventory Optimisation platform provides optimal inventory targets across the supply chain, balancing cost and service while minimising waste. The implementation required senior management buy-in and a dedicated project team. The roll-out was phased, starting with more mature areas and gradually building confidence in the system's outputs.
Operational Impact
Quantitative Benefit
Case Study missing?
Start adding your own!
Register with your work email and create a new case study profile for your business.
Related Case Studies.
.png)
Case Study
Improving Vending Machine Profitability with the Internet of Things (IoT)
The vending industry is undergoing a sea change, taking advantage of new technologies to go beyond just delivering snacks to creating a new retail location. Intelligent vending machines can be found in many public locations as well as company facilities, selling different types of goods and services, including even computer accessories, gold bars, tickets, and office supplies. With increasing sophistication, they may also provide time- and location-based data pertaining to sales, inventory, and customer preferences. But at the end of the day, vending machine operators know greater profitability is driven by higher sales and lower operating costs.
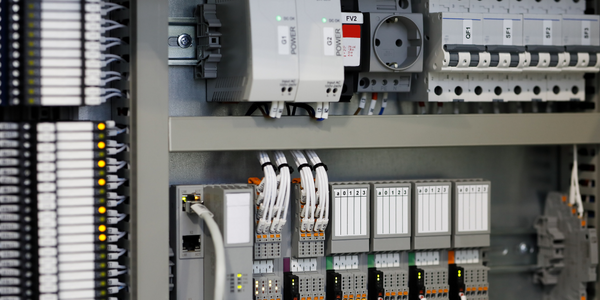
Case Study
Improving Production Line Efficiency with Ethernet Micro RTU Controller
Moxa was asked to provide a connectivity solution for one of the world's leading cosmetics companies. This multinational corporation, with retail presence in 130 countries, 23 global braches, and over 66,000 employees, sought to improve the efficiency of their production process by migrating from manual monitoring to an automatic productivity monitoring system. The production line was being monitored by ABB Real-TPI, a factory information system that offers data collection and analysis to improve plant efficiency. Due to software limitations, the customer needed an OPC server and a corresponding I/O solution to collect data from additional sensor devices for the Real-TPI system. The goal is to enable the factory information system to more thoroughly collect data from every corner of the production line. This will improve its ability to measure Overall Equipment Effectiveness (OEE) and translate into increased production efficiencies. System Requirements • Instant status updates while still consuming minimal bandwidth to relieve strain on limited factory networks • Interoperable with ABB Real-TPI • Small form factor appropriate for deployment where space is scarce • Remote software management and configuration to simplify operations
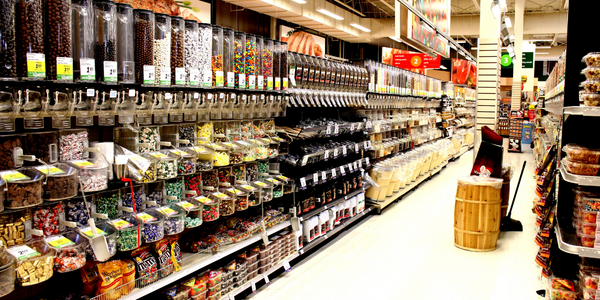
Case Study
How Sirqul’s IoT Platform is Crafting Carrefour’s New In-Store Experiences
Carrefour Taiwan’s goal is to be completely digital by end of 2018. Out-dated manual methods for analysis and assumptions limited Carrefour’s ability to change the customer experience and were void of real-time decision-making capabilities. Rather than relying solely on sales data, assumptions, and disparate systems, Carrefour Taiwan’s CEO led an initiative to find a connected IoT solution that could give the team the ability to make real-time changes and more informed decisions. Prior to implementing, Carrefour struggled to address their conversion rates and did not have the proper insights into the customer decision-making process nor how to make an immediate impact without losing customer confidence.
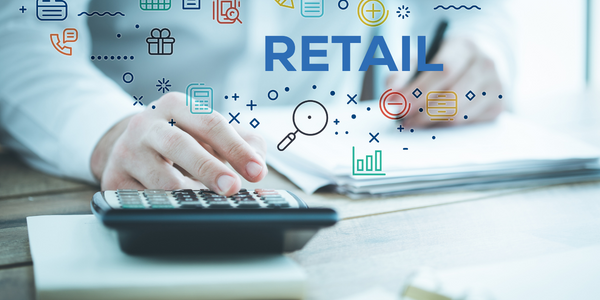
Case Study
Digital Retail Security Solutions
Sennco wanted to help its retail customers increase sales and profits by developing an innovative alarm system as opposed to conventional connected alarms that are permanently tethered to display products. These traditional security systems were cumbersome and intrusive to the customer shopping experience. Additionally, they provided no useful data or analytics.