The Alaska Railroad Engineers a Better Warehouse with RF-SMART
Customer Company Size
Large Corporate
Region
- America
Country
- United States
Product
- RF-SMART
- JD Edwards
Tech Stack
- Native JDE API
Implementation Scale
- Enterprise-wide Deployment
Impact Metrics
- Productivity Improvements
- Customer Satisfaction
- Cost Savings
Technology Category
- Functional Applications - Inventory Management Systems
- Application Infrastructure & Middleware - API Integration & Management
Applicable Industries
- Transportation
Applicable Functions
- Warehouse & Inventory Management
- Logistics & Transportation
Use Cases
- Inventory Management
- Warehouse Automation
- Supply Chain Visibility
Services
- System Integration
- Training
About The Customer
The Alaska Railroad Corporation (ARRC) is a full-service freight and passenger railroad, with rail lines in south central and interior Alaska. Primarily running as a regularly scheduled public transportation service, ARRC connects major cities such as Fairbanks and Anchorage with remote locations. With more than 500,000 passengers annually, ARRC routes across miles of wild landscape connecting metropolitan areas. Alaska Railroad freight operations transport materials both within Alaska and to/from the Lower 48. With complex internal operations meeting a variety of business demands, ARRC needed an inventory management solution for their supply warehouse to improve warehouse operations. Using strict metrics, ARRC chose RF-SMART.
The Challenge
Having implemented JD Edwards the previous year, ARRC was seeking a solution that would easily and seamlessly integrate into JD Edwards. As RF-SMART uses native JDE API and does not keep any data outside of JD Edwards, the ARRC selection team knew they had found the best solution to meet their needs. The architecture of how RF-SMART works with JD Edwards is really bullet proof. Not only is there no delay or gaps in our data, but we didn’t have to make any custom modifications. ARRC had found a solution to meet all its functionality requisites and solve their business needs, and one that would require little on the part of their IT team.
The Solution
ARRC uses RF-SMART in its warehouse to serve internal customers and different departments. The warehouse is a vital component for their railroad crew. Previously, maintaining an accurate inventory in the warehouse was almost impossible. Warehouse Supervisor, Ron Lewis notes that at times, it would be a week before data was entered from pick slips into JD Edwards. Relying heavily on paper process was time-consuming and error-laden. Now re-order/ review is accurate and up to date. Utilizing the built-in logic of RF-SMART, ARRC has reorganized its warehouse to follow RF-SMART; this one change alone has accounted for over 20% increase in inventory accuracy. Not only has RF-SMART made its warehouse layout more accurate and efficient, but as a result of implementing, ARRC is better utilizing their resources and supplies. Not only can they ensure they have inventory on hand to meet upcoming work orders, but they can meet immediate demands as needs arise. With RF-SMART, ARRC is better able to maintain accurate inventory of its critical components, such as air-brake valves and bearings. Lewis knows he can now monitor daily usage and assure that critical items will be available when needed, taking manufacturer lead times and other logistical considerations into account. Having accurate information at all times allows them to identify demand, better respond to internal customers’ needs and keep its trains - and revenue - on schedule.
Operational Impact
Quantitative Benefit
Case Study missing?
Start adding your own!
Register with your work email and create a new case study profile for your business.
Related Case Studies.
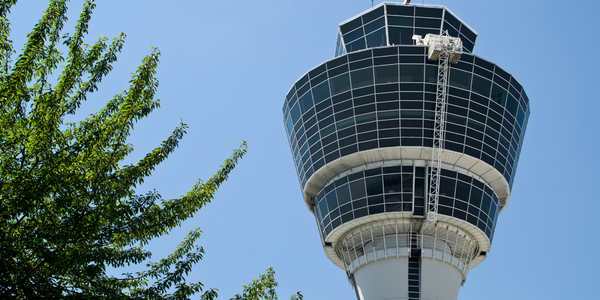
Case Study
Airport SCADA Systems Improve Service Levels
Modern airports are one of the busiest environments on Earth and rely on process automation equipment to ensure service operators achieve their KPIs. Increasingly airport SCADA systems are being used to control all aspects of the operation and associated facilities. This is because unplanned system downtime can cost dearly, both in terms of reduced revenues and the associated loss of customer satisfaction due to inevitable travel inconvenience and disruption.
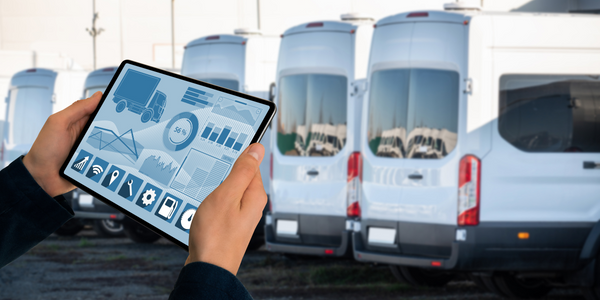
Case Study
IoT-based Fleet Intelligence Innovation
Speed to market is precious for DRVR, a rapidly growing start-up company. With a business model dependent on reliable mobile data, managers were spending their lives trying to negotiate data roaming deals with mobile network operators in different countries. And, even then, service quality was a constant concern.
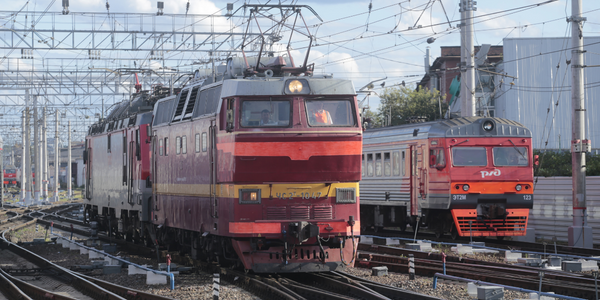
Case Study
Digitize Railway with Deutsche Bahn
To reduce maintenance costs and delay-causing failures for Deutsche Bahn. They need manual measurements by a position measurement system based on custom-made MEMS sensor clusters, which allow autonomous and continuous monitoring with wireless data transmission and long battery. They were looking for data pre-processing solution in the sensor and machine learning algorithms in the cloud so as to detect critical wear.
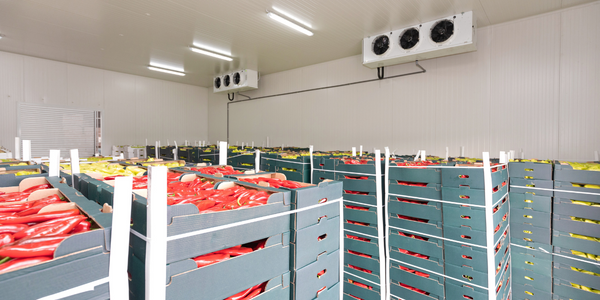
Case Study
Cold Chain Transportation and Refrigerated Fleet Management System
1) Create a digital connected transportation solution to retrofit cold chain trailers with real-time tracking and controls. 2) Prevent multi-million dollar losses due to theft or spoilage. 3) Deliver a digital chain-of-custody solution for door to door load monitoring and security. 4) Provide a trusted multi-fleet solution in a single application with granular data and access controls.
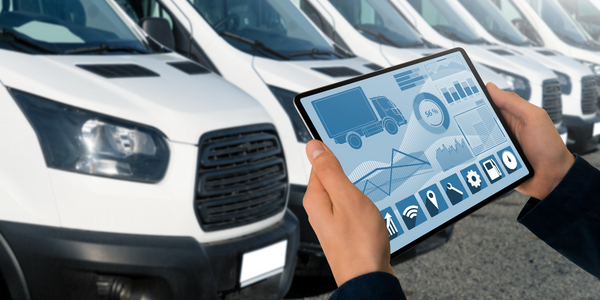
Case Study
Vehicle Fleet Analytics
Organizations frequently implement a maintenance strategy for their fleets of vehicles using a combination of time and usage based maintenance schedules. While effective as a whole, time and usage based schedules do not take into account driving patterns, environmental factors, and sensors currently deployed within the vehicle measuring crank voltage, ignition voltage, and acceleration, all of which have a significant influence on the overall health of the vehicle.In a typical fleet, a large percentage of road calls are related to electrical failure, with battery failure being a common cause. Battery failures result in unmet service agreement levels and costly re-adjustment of scheduled to provide replacement vehicles. To reduce the impact of unplanned maintenance, the transportation logistics company was interested in a trial of C3 Vehicle Fleet Analytics.
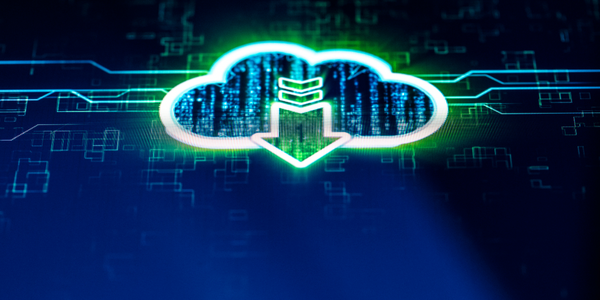
Case Study
3M Gains Real-Time Insight with Cloud Solution
The company has a long track record of innovative technology solutions. For example, 3M helps its customers optimize parking operations by automating fee collection and other processes. To improve support for this rapidly expanding segment, 3M needed to automate its own data collection and reporting. The company had recently purchased the assets of parking, tolling, and automatic license plate reader businesses, and required better insight into these acquisitions. Chad Reed, Global Business Manager for 3M Parking Systems, says, “With thousands of installations across the world, we couldn’t keep track of our software and hardware deployments, which made it difficult to understand our market penetration.” 3M wanted a tracking application that sales staff could use to get real-time information about the type and location of 3M products in parking lots and garages. So that it could be used on-site with potential customers, the solution would have to provide access to data anytime, anywhere, and from an array of mobile devices. Jason Fox, Mobile Application Architect at 3M, upped the ante by volunteering to deliver the new app in one weekend. For Fox and his team, these requirements meant turning to the cloud instead of an on-premises datacenter. “My first thought was to go directly to the cloud because we needed to provide access not only to our salespeople, but to resellers who didn’t have access to our internal network,” says Fox. “The cloud just seemed like a logical choice.”