Tata Advanced Materials (TAML) Advances Cutting Technology, Optimizes Consumption, and Enhances Competitiveness

Customer Company Size
Large Corporate
Region
- Asia
Country
- India
Product
- DesignConceptTechTex
- DiaminoTechTex
- VectorTechTex
- Digiplan
Tech Stack
- Multi-CAD Environment
- Automatic Nesting
Implementation Scale
- Enterprise-wide Deployment
Impact Metrics
- Cost Savings
- Productivity Improvements
- Customer Satisfaction
Technology Category
- Analytics & Modeling - Predictive Analytics
- Application Infrastructure & Middleware - Data Exchange & Integration
- Functional Applications - Remote Monitoring & Control Systems
Applicable Industries
- Aerospace
Applicable Functions
- Quality Assurance
Use Cases
- Predictive Maintenance
- Machine Condition Monitoring
- Process Control & Optimization
Services
- System Integration
- Software Design & Engineering Services
About The Customer
Tata Advanced Materials Limited (TAML), promoted by Tata Industries Limited, is a pioneer and leader in composite solutions, catering to the global aerospace, space defense, and industrial markets. TAML provides its customers with unprecedented quality and innovative engineering solutions, using advanced composite materials. TAML is the first company in India to be certified by NADCAP in composite manufacturing. With the state-of-the-art facilities, technology, and processes, TAML has all required know-how for undertaking “Design to Build” solutions for the global market.
The Challenge
With increasing demand from its customers, Tata Advanced Materials (TAML) was faced with the challenge of reducing design cycle time and cutting manufacturing costs while delivering the best quality in the most efficient way possible. Given this challenge, the company prioritized speeding up the manufacturing process and optimizing the consumption of their specialized materials. But with their wide variety of clients creating designs in a variety of CAD programs, it was also critical to have a system that could work with different imported formats. In choosing a technology partner, TAML insisted on having access to the latest, most reliable and proven technology backed by active research, long-term return on investment, and prompt customer service.
The Solution
The DesignConceptTechTex and DiaminoTechTex package – the most appropriate solution on the market for importing diverse data from different CAD environments – delivers remarkable fabric savings for TAML via tightly packed markers. The VectorTechTex easily handles these optimized markers with remarkable precision, delivering high quality cut parts at lower costs. “Through Lectra’s expertise and technology, we have made the cutting process more efficient and consistent,” said TAML CEO Mr. Arvind Mathew. “This enables us to reduce material consumption and enhance our competitiveness.” Lectra’s solutions result in remarkable savings. DesignConceptTechTex, with its particular focus on specialized industrial fabrics requiring a high level of technology, offers advanced functionalities, designed for creating technical drawings and assembly plans. Using this powerful solution, TAML is now able to import its existing DXF data from a multi-CAD environment and achieve remarkable savings. Within months after acquiring the start-up design solutions, TAML chose to upgrade DiaminoTechTex with the more advanced module. This solution experience combines the marker-making operators with the speed and calculation power of automatic nesting. These additional features have helped TAML to achieve significant improvement in fabric optimization, which resulted in further savings. This was important as TAML uses expensive industrial fabrics commonly associated with the aerospace, personal protective equipment, and special defense equipment sectors.
Operational Impact
Quantitative Benefit
Case Study missing?
Start adding your own!
Register with your work email and create a new case study profile for your business.
Related Case Studies.
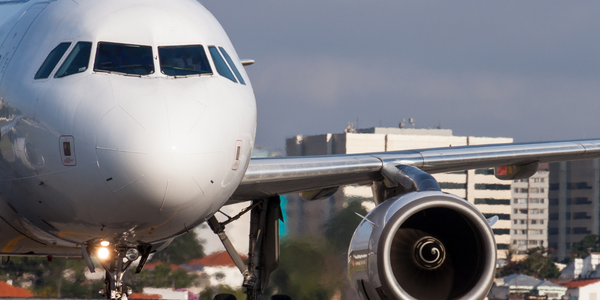
Case Study
Airbus Soars with Wearable Technology
Building an Airbus aircraft involves complex manufacturing processes consisting of thousands of moving parts. Speed and accuracy are critical to business and competitive advantage. Improvements in both would have high impact on Airbus’ bottom line. Airbus wanted to help operators reduce the complexity of assembling cabin seats and decrease the time required to complete this task.
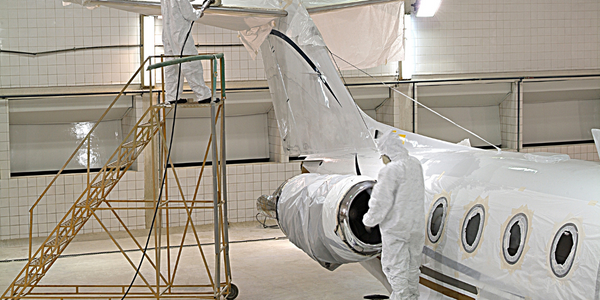
Case Study
Aircraft Predictive Maintenance and Workflow Optimization
First, aircraft manufacturer have trouble monitoring the health of aircraft systems with health prognostics and deliver predictive maintenance insights. Second, aircraft manufacturer wants a solution that can provide an in-context advisory and align job assignments to match technician experience and expertise.
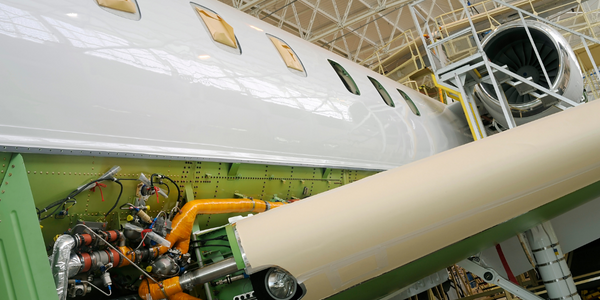
Case Study
Aerospace & Defense Case Study Airbus
For the development of its new wide-body aircraft, Airbus needed to ensure quality and consistency across all internal and external stakeholders. Airbus had many challenges including a very aggressive development schedule and the need to ramp up production quickly to satisfy their delivery commitments. The lack of communication extended design time and introduced errors that drove up costs.
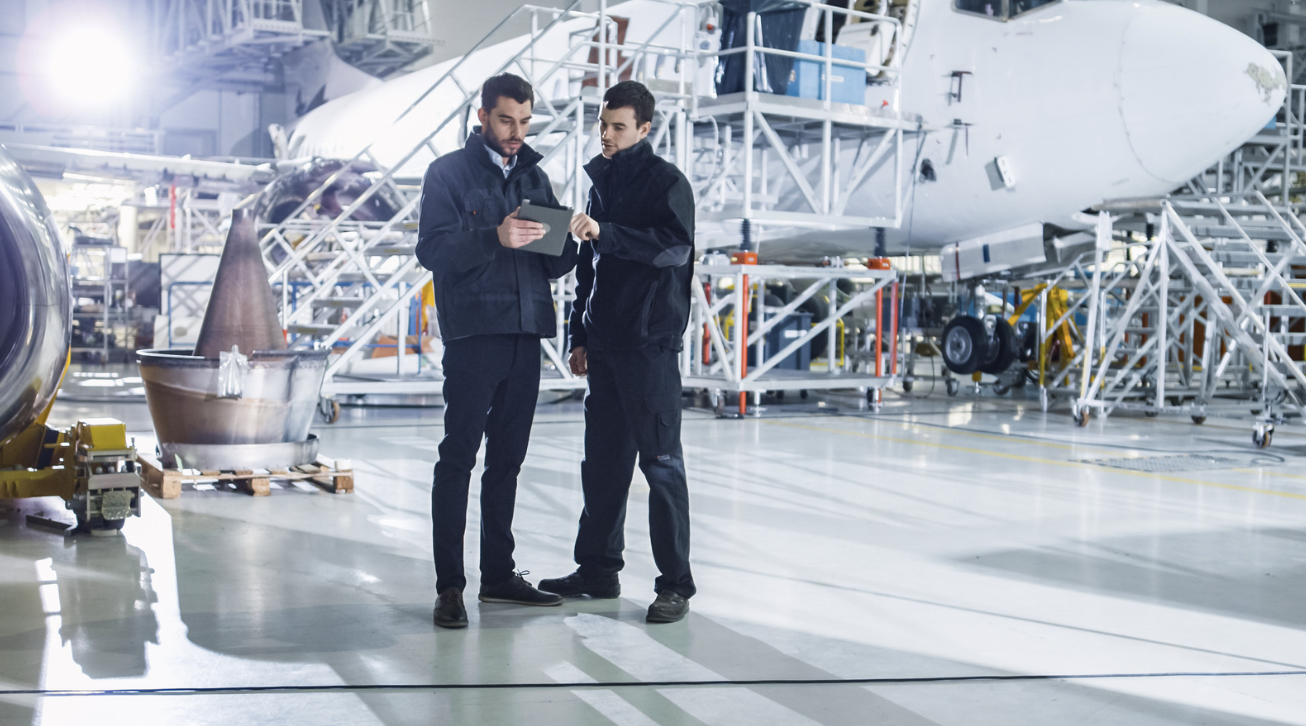
Case Study
Developing Smart Tools for the Airbus Factory
Manufacturing and assembly of aircraft, which involves tens of thousands of steps that must be followed by the operators, and a single mistake in the process could cost hundreds of thousands of dollars to fix, makes the room for error very small.
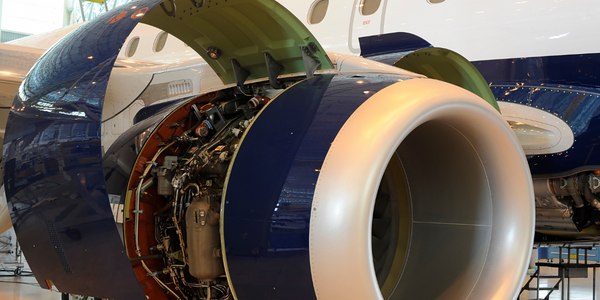
Case Study
Accelerate Production for Spirit AeroSystems
The manufacture and assembly of massive fuselage assemblies and other large structures generates a river of data. In fact, the bill of materials for a single fuselage alone can be millions of rows of data. In-house production processes and testing, as well as other manufacturers and customers created data flows that overwhelmed previous processes and information systems. Spirit’s customer base had grown substantially since their 2005 divestiture from Boeing, resulting in a $41 billion backlog of orders to fill. To address this backlog, meet increased customer demands and minimize additional capital investment, the company needed a way to improve throughput in the existing operational footprint. Spirit had a requirement from customers to increase fuselage production by 30%. To accomplish this goal, Spirit needed real-time information on its value chain and workflow. However, the two terabytes of data being pulled from their SAP ECC was unmanageable and overloaded their business warehouse. It had become time-consuming and difficult to pull aggregate data, disaggregate it for the needed information and then reassemble to create a report. During the 6-8 hours it took to build a report, another work shift (they run three per day) would have already taken place, thus the report content was out-of-date before it was ever delivered. As a result, supervisors often had to rely on manual efforts to provide charts, reports and analysis.