Technology Category
- Networks & Connectivity - 5G
- Platform as a Service (PaaS) - Application Development Platforms
Applicable Industries
- Pharmaceuticals
- Transportation
Applicable Functions
- Facility Management
- Logistics & Transportation
Use Cases
- Last Mile Delivery
- Transportation Simulation
About The Customer
The customer is a leading specialty generic pharmaceuticals company, founded in 1983. It is one of the largest of its kind in the world, with over 40 manufacturing facilities. The company provides high-quality, affordable medicines to more than 100 countries across the globe. With a vast global footprint, the company manages over 100 monthly shipments via ocean and air, making its logistics operations complex and challenging. The company was facing significant challenges in tracking the progress of all freight and assessing the performance of Logistics Service Providers (LSPs), leading to inefficiencies and penalties.
The Challenge
The company, a global leader in specialty generic pharmaceuticals, was facing significant challenges in managing its logistics operations. With over 100 monthly shipments via ocean and air, tracking the progress of all freight and assessing the performance of Logistics Service Providers (LSPs) was a daunting task. The communication process was inefficient, with updates on task completion being shared via emails, leading to multiple email trails for each shipment. This made it difficult to map and audit the progress of every shipment. The inability to track shipment status and assign follow-up tasks to stakeholders resulted in hefty penalties like demurrage and detention charges. Furthermore, the negligence of the LSPs could not be identified until the fine was levied. The documentation process was also unorganized, with all shipment documents being shared via email. The lack of a common repository for these documents led to process inefficiencies and difficulty in tracking missing documents.
The Solution
The company implemented GoComet’s GoShipment module to streamline its logistics operations and minimize communication gaps. This solution provided a single platform for interacting with all stakeholders, sharing documents, and mapping the progress of each shipment. GoShipment enabled a control tower view over their entire logistics operations, offering visibility over the progress of every crucial task on a single window. This eliminated the need for multiple calls and emails as all stakeholders could easily communicate and coordinate, assign responsibilities, and trace the flow of tasks on the platform. The solution also offered a Cloud Documentation and checklist facility, allowing the logistics team to upload and store relevant documents all in one place with 24×7 access. Additionally, the solution provided transparent performance management with real-time updates on delays, enabling the team to proactively prioritize tasks and address bottlenecks. They could also access detailed performance reports of every stakeholder on a single analytics dashboard.
Operational Impact
Case Study missing?
Start adding your own!
Register with your work email and create a new case study profile for your business.
Related Case Studies.
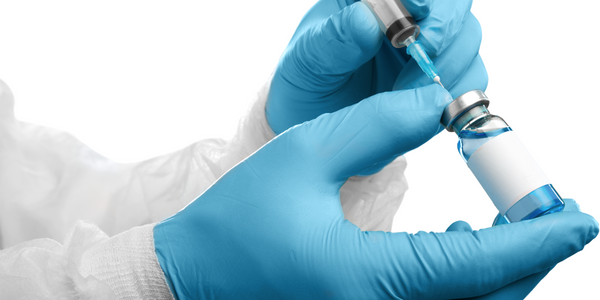
Case Study
Case Study: Pfizer
Pfizer’s high-performance computing software and systems for worldwide research and development support large-scale data analysis, research projects, clinical analytics, and modeling. Pfizer’s computing services are used across the spectrum of research and development efforts, from the deep biological understanding of disease to the design of safe, efficacious therapeutic agents.
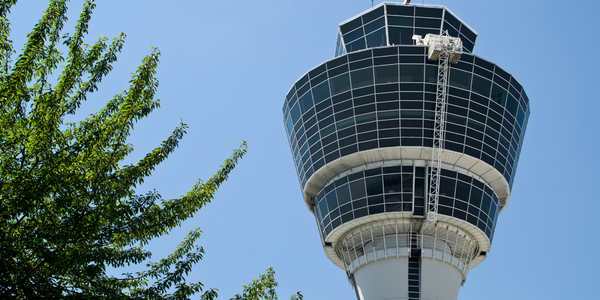
Case Study
Airport SCADA Systems Improve Service Levels
Modern airports are one of the busiest environments on Earth and rely on process automation equipment to ensure service operators achieve their KPIs. Increasingly airport SCADA systems are being used to control all aspects of the operation and associated facilities. This is because unplanned system downtime can cost dearly, both in terms of reduced revenues and the associated loss of customer satisfaction due to inevitable travel inconvenience and disruption.
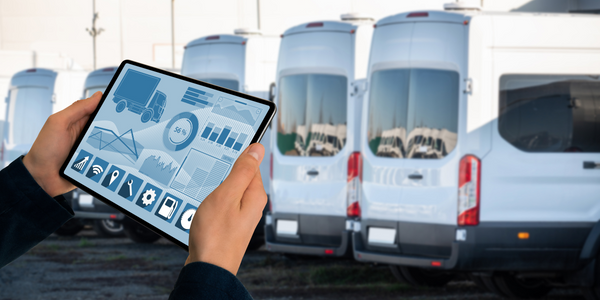
Case Study
IoT-based Fleet Intelligence Innovation
Speed to market is precious for DRVR, a rapidly growing start-up company. With a business model dependent on reliable mobile data, managers were spending their lives trying to negotiate data roaming deals with mobile network operators in different countries. And, even then, service quality was a constant concern.
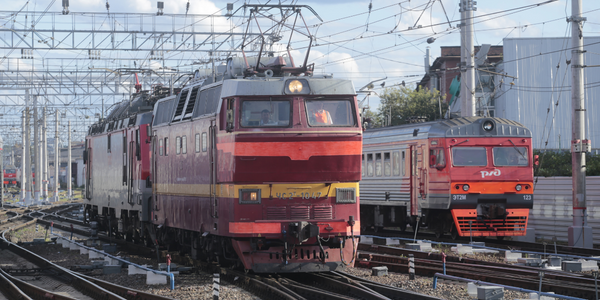
Case Study
Digitize Railway with Deutsche Bahn
To reduce maintenance costs and delay-causing failures for Deutsche Bahn. They need manual measurements by a position measurement system based on custom-made MEMS sensor clusters, which allow autonomous and continuous monitoring with wireless data transmission and long battery. They were looking for data pre-processing solution in the sensor and machine learning algorithms in the cloud so as to detect critical wear.
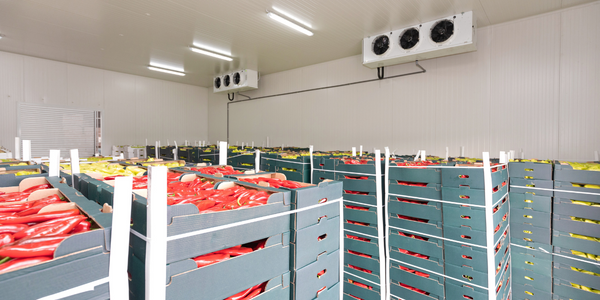
Case Study
Cold Chain Transportation and Refrigerated Fleet Management System
1) Create a digital connected transportation solution to retrofit cold chain trailers with real-time tracking and controls. 2) Prevent multi-million dollar losses due to theft or spoilage. 3) Deliver a digital chain-of-custody solution for door to door load monitoring and security. 4) Provide a trusted multi-fleet solution in a single application with granular data and access controls.
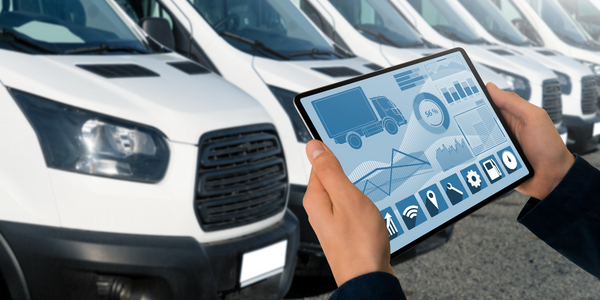
Case Study
Vehicle Fleet Analytics
Organizations frequently implement a maintenance strategy for their fleets of vehicles using a combination of time and usage based maintenance schedules. While effective as a whole, time and usage based schedules do not take into account driving patterns, environmental factors, and sensors currently deployed within the vehicle measuring crank voltage, ignition voltage, and acceleration, all of which have a significant influence on the overall health of the vehicle.In a typical fleet, a large percentage of road calls are related to electrical failure, with battery failure being a common cause. Battery failures result in unmet service agreement levels and costly re-adjustment of scheduled to provide replacement vehicles. To reduce the impact of unplanned maintenance, the transportation logistics company was interested in a trial of C3 Vehicle Fleet Analytics.