SPARTAN MOTORS Fuels Innovation, Productivity & Quality with Aras Enterprise PLM
Company Size
1,000+
Region
- America
Country
- United States
Product
- Aras Innovator
- SolidWorks CAD
- SolidWorks Enterprise PDM
Tech Stack
- Web-based PLM
- ERP Integration
Implementation Scale
- Enterprise-wide Deployment
Impact Metrics
- Customer Satisfaction
- Digital Expertise
- Productivity Improvements
Technology Category
- Functional Applications - Enterprise Resource Planning Systems (ERP)
- Functional Applications - Product Lifecycle Management Systems (PLM)
Applicable Industries
- Automotive
- Specialty Vehicles
Applicable Functions
- Product Research & Development
- Quality Assurance
Services
- Software Design & Engineering Services
- System Integration
About The Customer
Spartan Motors is a leading provider of high-quality specialty vehicles, chassis, and truck bodies, serving markets such as emergency-rescue, recreational vehicles, and specialty vehicles. Founded in 1976 by a group of engineers dedicated to quality, value, service, and innovation, Spartan Motors has grown into a successful public company with approximately 1,800 employees across six facilities. The company is known for its customer-centric methodology, fostering innovation, speed, and agility. Spartan Motors is committed to Lean continuous process improvement and Green business practices, setting it apart from competitors and ensuring the delivery of premium custom products and services. The company’s product range includes fire trucks, delivery vans, motorhomes, and military armored vehicles.
The Challenge
Spartan Motors faced the challenge of standardizing cross-functional processes across multiple product lines and locations to achieve greater consistency, efficiency, and responsiveness. The company relied on SolidWorks CAD software for product design and SolidWorks Enterprise PDM for managing CAD files and drawings, but had numerous stand-alone, custom databases for other product-related information. This fragmented system led to inefficiencies and a lack of company-wide visibility. Spartan needed a scalable enterprise PLM solution that would not impact SolidWorks users or require the replacement of their existing SolidWorks Enterprise PDM environment.
The Solution
To address its challenges, Spartan Motors selected Aras for enterprise PLM and implemented a full Engineering Bill of Materials (BOM) with item-based product structure for configuration management and Enterprise Change Management. The implementation replaced the fragmented custom databases with a modern Web-based PLM solution that is item-based and process-centric. This consolidation streamlined processes and provided company-wide visibility. The Aras enterprise PLM solution now manages over 1.8 million BOM lines and more than 330,000 released parts, with an average of 1,000 new parts created per month. The solution also automated part number and drawing number generation, integrated with the ERP system, and enabled easy search and reuse of parts and BOMs, significantly boosting efficiency and productivity.
Operational Impact
Quantitative Benefit
Case Study missing?
Start adding your own!
Register with your work email and create a new case study profile for your business.
Related Case Studies.
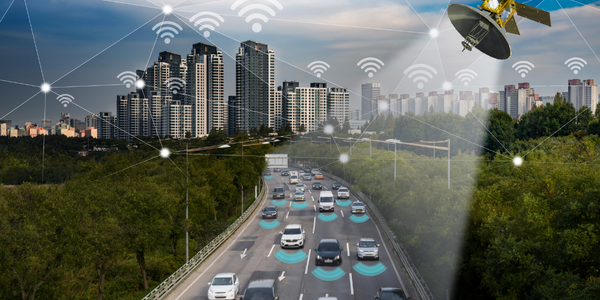
Case Study
Transformation for IoT Business Model in Connected Industrial Vehicles
CNH Industrial wanted to put IoT-enabled viechles onto the market. Whether monitoring a single machine or integrating an entire fleet, operators are able to track the status, speed, and movement of machines and their performance and also receive alerts on issues that may require service by a qualified technician to improve uptime and overall effectiveness of the vehicle.
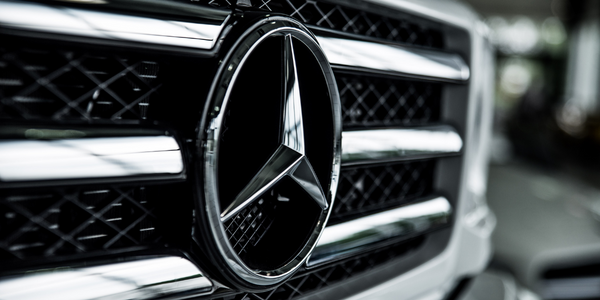
Case Study
Integral Plant Maintenance
Mercedes-Benz and his partner GAZ chose Siemens to be its maintenance partner at a new engine plant in Yaroslavl, Russia. The new plant offers a capacity to manufacture diesel engines for the Russian market, for locally produced Sprinter Classic. In addition to engines for the local market, the Yaroslavl plant will also produce spare parts. Mercedes-Benz Russia and his partner needed a service partner in order to ensure the operation of these lines in a maintenance partnership arrangement. The challenges included coordinating the entire maintenance management operation, in particular inspections, corrective and predictive maintenance activities, and the optimizing spare parts management. Siemens developed a customized maintenance solution that includes all electronic and mechanical maintenance activities (Integral Plant Maintenance).