Technology Category
- Platform as a Service (PaaS) - Application Development Platforms
- Robots - Autonomous Guided Vehicles (AGV)
Applicable Industries
- Automotive
- Healthcare & Hospitals
Applicable Functions
- Maintenance
- Product Research & Development
Use Cases
- Usage-Based Insurance
- Vehicle Performance Monitoring
Services
- System Integration
- Training
About The Customer
SISA is an insurance and investment company founded in 1962 in El Salvador. The company provides protection for natural and juridical persons through a wide range of insurance policies. With 60 years of experience and a commitment to customer care excellence, SISA has established itself as a leader in the insurance sector. The company embarked on a digital transformation journey in 2017, aiming to optimize its business processes using the AuraQuantic no-code platform. SISA's customer base includes individuals and businesses, and the company also works with a wide network of agents distributed throughout the country.
The Challenge
SISA, an insurance and investment company based in El Salvador, embarked on an ambitious digital transformation project in 2017. The company aimed to optimize its business processes using the AuraQuantic no-code platform. However, the COVID-19 pandemic significantly impacted SISA's plans, forcing the company to implement many of its projects within a tight timeframe of just three months. The company's top priority was to ensure optimal service levels for its customers and its extensive network of agents across the country. The pandemic also necessitated a shift to remote work, which presented additional challenges in terms of maintaining productivity and meeting new market needs.
The Solution
SISA leveraged the AuraQuantic no-code platform's flexibility and rapid application creation capabilities to adapt to the new working conditions. The platform enabled SISA's staff to continue their work remotely, meeting the new market needs that had arisen due to the pandemic. SISA implemented new processes that expedited document management and reduced waiting times for commission payments. A Guest Portal was also activated to facilitate online procedures and eliminate unnecessary travel for employees, agents, and customers. The AuraQuantic Training School provided crucial support, training SISA project leaders and all personnel involved in the project. The platform also allowed SISA to automate various processes, including vehicle claims, agent commissions, policy quotes and issuance, and healthcare claims.
Operational Impact
Quantitative Benefit
Case Study missing?
Start adding your own!
Register with your work email and create a new case study profile for your business.
Related Case Studies.
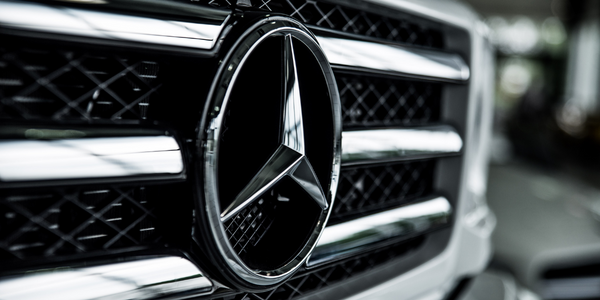
Case Study
Integral Plant Maintenance
Mercedes-Benz and his partner GAZ chose Siemens to be its maintenance partner at a new engine plant in Yaroslavl, Russia. The new plant offers a capacity to manufacture diesel engines for the Russian market, for locally produced Sprinter Classic. In addition to engines for the local market, the Yaroslavl plant will also produce spare parts. Mercedes-Benz Russia and his partner needed a service partner in order to ensure the operation of these lines in a maintenance partnership arrangement. The challenges included coordinating the entire maintenance management operation, in particular inspections, corrective and predictive maintenance activities, and the optimizing spare parts management. Siemens developed a customized maintenance solution that includes all electronic and mechanical maintenance activities (Integral Plant Maintenance).
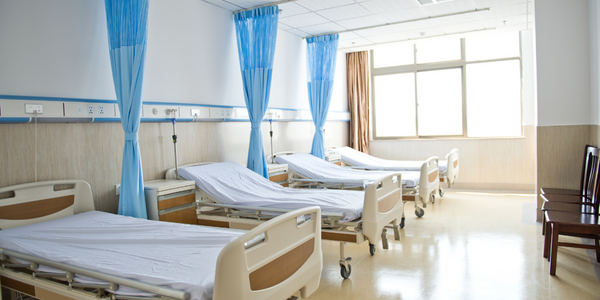
Case Study
Hospital Inventory Management
The hospital supply chain team is responsible for ensuring that the right medical supplies are readily available to clinicians when and where needed, and to do so in the most efficient manner possible. However, many of the systems and processes in use at the cancer center for supply chain management were not best suited to support these goals. Barcoding technology, a commonly used method for inventory management of medical supplies, is labor intensive, time consuming, does not provide real-time visibility into inventory levels and can be prone to error. Consequently, the lack of accurate and real-time visibility into inventory levels across multiple supply rooms in multiple hospital facilities creates additional inefficiency in the system causing over-ordering, hoarding, and wasted supplies. Other sources of waste and cost were also identified as candidates for improvement. Existing systems and processes did not provide adequate security for high-cost inventory within the hospital, which was another driver of cost. A lack of visibility into expiration dates for supplies resulted in supplies being wasted due to past expiry dates. Storage of supplies was also a key consideration given the location of the cancer center’s facilities in a dense urban setting, where space is always at a premium. In order to address the challenges outlined above, the hospital sought a solution that would provide real-time inventory information with high levels of accuracy, reduce the level of manual effort required and enable data driven decision making to ensure that the right supplies were readily available to clinicians in the right location at the right time.
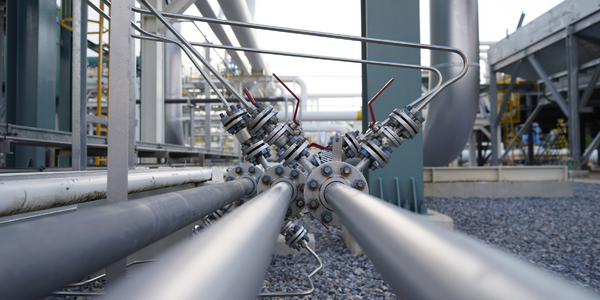
Case Study
Gas Pipeline Monitoring System for Hospitals
This system integrator focuses on providing centralized gas pipeline monitoring systems for hospitals. The service they provide makes it possible for hospitals to reduce both maintenance and labor costs. Since hospitals may not have an existing network suitable for this type of system, GPRS communication provides an easy and ready-to-use solution for remote, distributed monitoring systems System Requirements - GPRS communication - Seamless connection with SCADA software - Simple, front-end control capability - Expandable I/O channels - Combine AI, DI, and DO channels