Technology Category
- Cybersecurity & Privacy - Security Compliance
- Sensors - Camera / Video Systems
Applicable Industries
- Metals
- Transportation
Applicable Functions
- Quality Assurance
- Sales & Marketing
Use Cases
- Driver Performance Monitoring
- Time Sensitive Networking
About The Customer
Sabel Steel is a family-owned steel and scrap enterprise established in 1856. The company specializes in the sale, fabrication, and transportation of steel products, with locations across three states. Sabel Steel takes great pride in delivering exceptional customer service, emphasizing safety, and valuing their employees, whom they regard as their foremost asset. The company operates a fleet of 45 trucks for the transportation of their products. Prior to adopting Motive, Sabel Steel used a well-known provider as their ELD solution, which presented numerous challenges.
The Challenge
Sabel Steel, a family-owned steel and scrap enterprise, was facing growing driver dissatisfaction with their electronic logging devices (ELDs). The ELD solution they were using from a well-known provider was proving to be costly, unreliable, and complex. The hardware was not dependable, and the user experience was complicated, leading to frequent complaints from drivers. Moreover, getting assistance from the provider's customer service was a time-consuming and difficult process. This situation was causing frustration for the DOT compliance and safety manager, Diane Woodruff. The company also faced a significant challenge when one of their trucks was forced off the road and into a ditch by a pickup truck, causing damage exceeding $120,000. Without video evidence to confirm their driver was not at fault, they had to rely solely on the driver’s testimony and the accident report.
The Solution
To address these challenges, Sabel Steel decided to switch to Motive, an IoT solution that offered a more user-friendly, dependable experience, enhanced customer support, and cost-effectiveness. They installed Motive Smart Dashcams in their trucks to safeguard their drivers and the company from similar incidents in the future. The dash cam footage proved invaluable in vindicating their drivers in case of accidents, saving the company from costly litigation. Motive’s prioritized footage and coaching tools also enhanced the efficiency of the safety manager, allowing her to review incidents using video footage, discuss events, and help drivers learn from their experiences. The company also used Motive’s tracking solution to monitor their drivers’ real-time locations, improving accountability and customer service by providing accurate ETAs.
Operational Impact
Quantitative Benefit
Case Study missing?
Start adding your own!
Register with your work email and create a new case study profile for your business.
Related Case Studies.
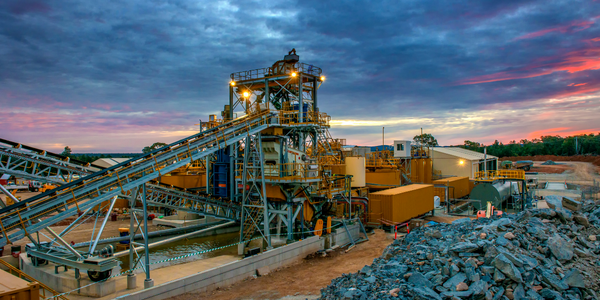
Case Study
Goldcorp: Internet of Things Enables the Mine of the Future
Goldcorp is committed to responsible mining practices and maintaining maximum safety for its workers. At the same time, the firm is constantly exploring ways to improve the efficiency of its operations, extend the life of its assets, and control costs. Goldcorp needed technology that can maximize production efficiency by tracking all mining operations, keep employees safe with remote operations and monitoring of hazardous work areas and control production costs through better asset and site management.
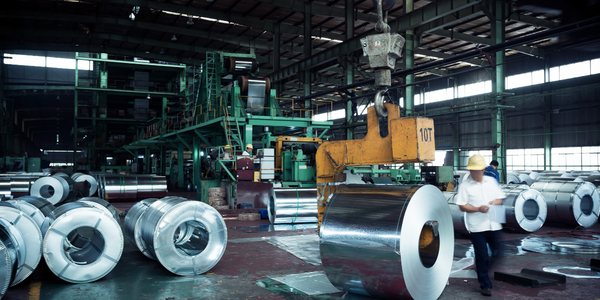
Case Study
KSP Steel Decentralized Control Room
While on-site in Pavlodar, Kazakhstan, the DAQRI team of Business Development and Solutions Architecture personnel worked closely with KSP Steel’s production leadership to understand the steel production process, operational challenges, and worker pain points.
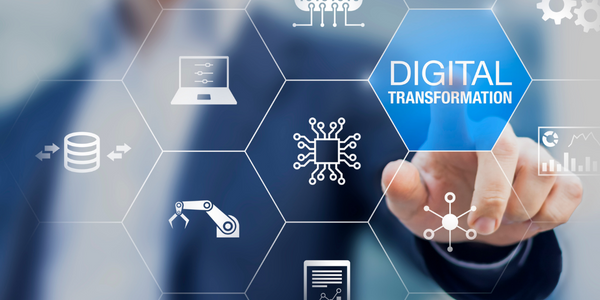
Case Study
Bluescope Steel on Path to Digitally Transform Operations and IT
Increasing competition and fluctuations in the construction market prompted BlueScope Steel to look toward digital transformation of its four businesses, including modern core applications and IT infrastructure. BlueScope needed to modernize its infrastructure and adopt new technologies to improve operations and supply chain efficiency while maintaining and updating an aging application portfolio.
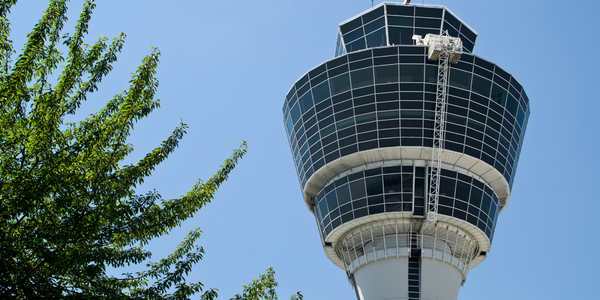
Case Study
Airport SCADA Systems Improve Service Levels
Modern airports are one of the busiest environments on Earth and rely on process automation equipment to ensure service operators achieve their KPIs. Increasingly airport SCADA systems are being used to control all aspects of the operation and associated facilities. This is because unplanned system downtime can cost dearly, both in terms of reduced revenues and the associated loss of customer satisfaction due to inevitable travel inconvenience and disruption.
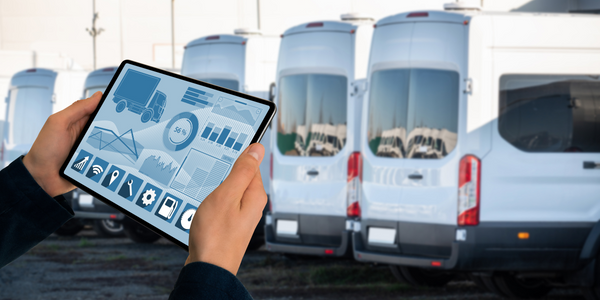
Case Study
IoT-based Fleet Intelligence Innovation
Speed to market is precious for DRVR, a rapidly growing start-up company. With a business model dependent on reliable mobile data, managers were spending their lives trying to negotiate data roaming deals with mobile network operators in different countries. And, even then, service quality was a constant concern.
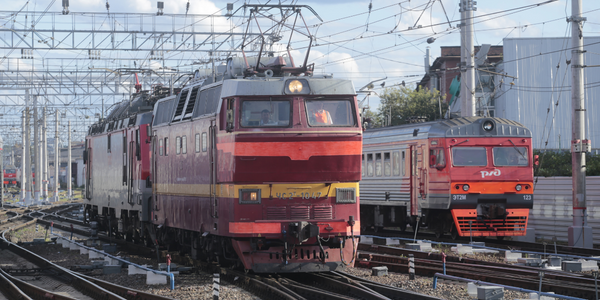
Case Study
Digitize Railway with Deutsche Bahn
To reduce maintenance costs and delay-causing failures for Deutsche Bahn. They need manual measurements by a position measurement system based on custom-made MEMS sensor clusters, which allow autonomous and continuous monitoring with wireless data transmission and long battery. They were looking for data pre-processing solution in the sensor and machine learning algorithms in the cloud so as to detect critical wear.