Technology Category
- Functional Applications - Manufacturing Execution Systems (MES)
Applicable Industries
- Aerospace
- National Security & Defense
Applicable Functions
- Procurement
- Product Research & Development
Use Cases
- Additive Manufacturing
- Manufacturing Process Simulation
About The Customer
Rafael is a leading company in the Aerospace & Defense industry with over 8,000 employees and a revenue of $3 billion. For more than 70 years, Rafael has pioneered advances in defense, cyber, and security solutions for air, land, sea, and space. The company's engineers involved in the product development process are typically expected to have vast amounts of expertise and knowledge. As part of their company roadmap, Rafael made a business decision to invest heavily in design to cost initiatives, aiming to manage cost from the design stage all the way up to manufacturing.
The Challenge
Rafael, a pioneer in defense, cyber, and security solutions for over 70 years, had set challenging design to cost targets as part of their company roadmap. The goal was to manage cost from the design stage all the way up to manufacturing, including initiatives related to procurement, project management, system engineering, and requirements management. However, achieving these targets required the right tools and technology. Rafael's engineers, who are typically expected to have vast amounts of expertise and knowledge, needed a technology that they could rely on to work together efficiently, seamlessly, and collaboratively to meet these design to cost initiatives.
The Solution
Rafael chose aPriori as their technology partner to meet their design to cost goals. aPriori was provided to all product development engineers to facilitate collaboration across departments. The manufacturing insights provided by aPriori were the perfect technology to meet their strategy. By utilizing the digital factories and manufacturing simulation in aPriori, the lines of communication opened up between the engineers at Rafael. This allowed them to modify designs for cost, achieving significant cost savings on parts. For instance, a part that was originally designed at around $1,400 was simplified using aPriori to achieve a modified cost of $650.
Operational Impact
Quantitative Benefit
Case Study missing?
Start adding your own!
Register with your work email and create a new case study profile for your business.
Related Case Studies.
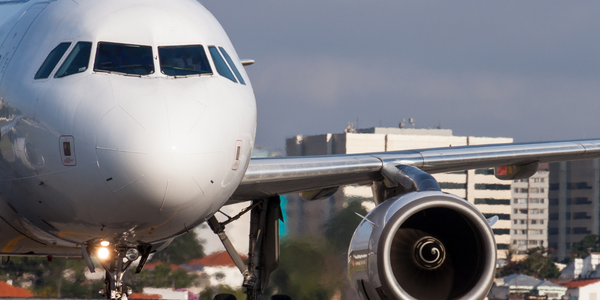
Case Study
Airbus Soars with Wearable Technology
Building an Airbus aircraft involves complex manufacturing processes consisting of thousands of moving parts. Speed and accuracy are critical to business and competitive advantage. Improvements in both would have high impact on Airbus’ bottom line. Airbus wanted to help operators reduce the complexity of assembling cabin seats and decrease the time required to complete this task.
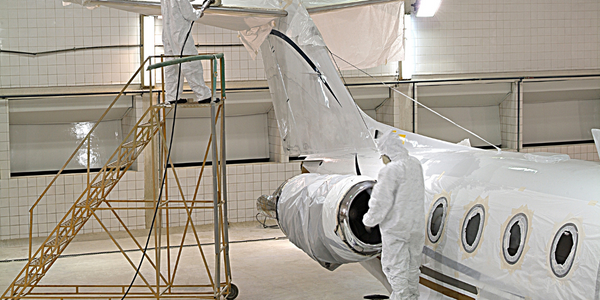
Case Study
Aircraft Predictive Maintenance and Workflow Optimization
First, aircraft manufacturer have trouble monitoring the health of aircraft systems with health prognostics and deliver predictive maintenance insights. Second, aircraft manufacturer wants a solution that can provide an in-context advisory and align job assignments to match technician experience and expertise.
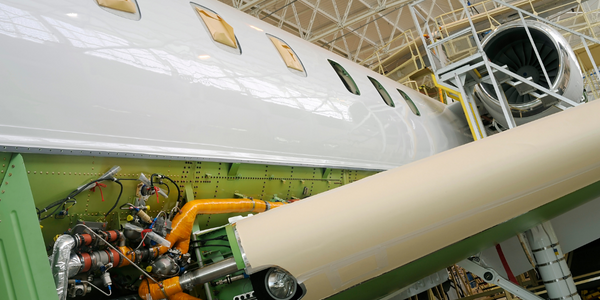
Case Study
Aerospace & Defense Case Study Airbus
For the development of its new wide-body aircraft, Airbus needed to ensure quality and consistency across all internal and external stakeholders. Airbus had many challenges including a very aggressive development schedule and the need to ramp up production quickly to satisfy their delivery commitments. The lack of communication extended design time and introduced errors that drove up costs.
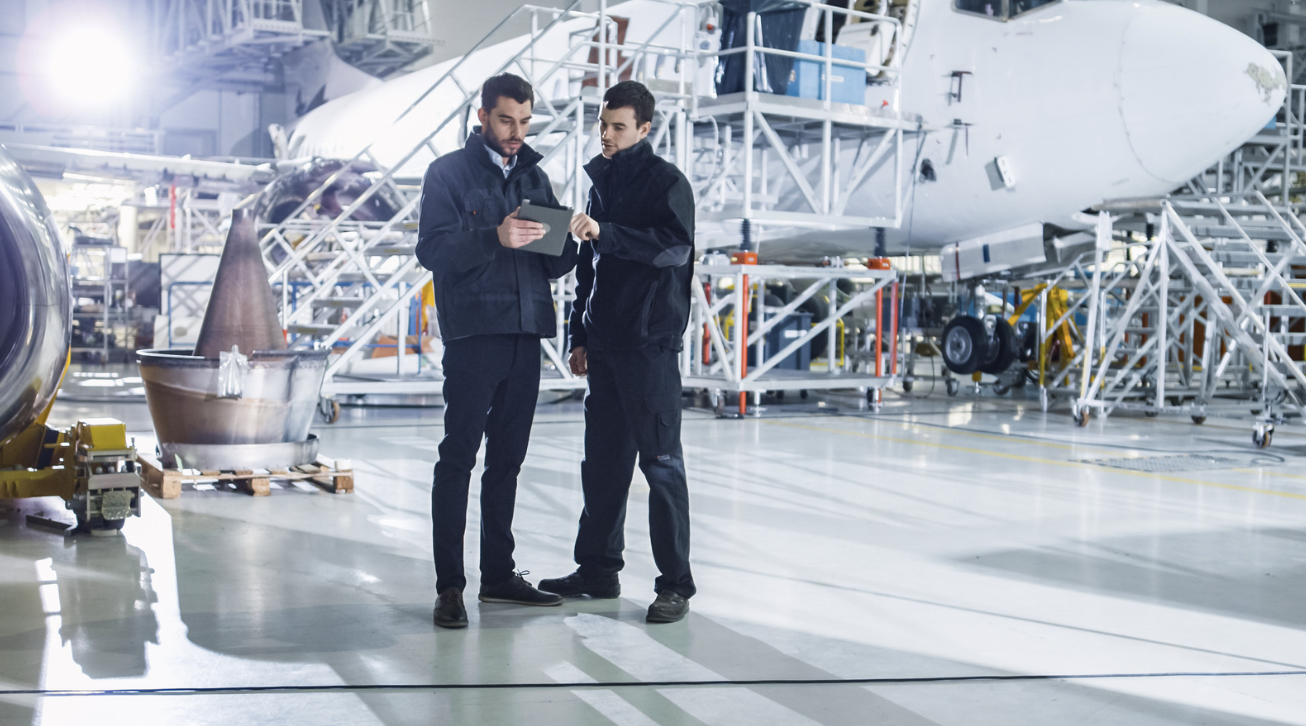
Case Study
Developing Smart Tools for the Airbus Factory
Manufacturing and assembly of aircraft, which involves tens of thousands of steps that must be followed by the operators, and a single mistake in the process could cost hundreds of thousands of dollars to fix, makes the room for error very small.
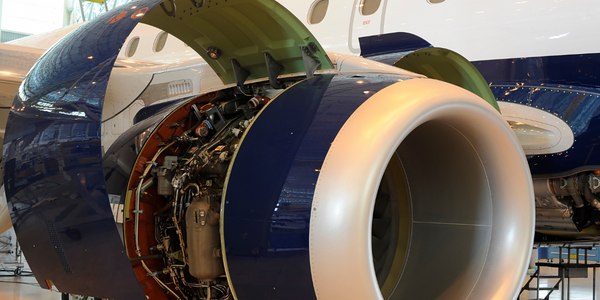
Case Study
Accelerate Production for Spirit AeroSystems
The manufacture and assembly of massive fuselage assemblies and other large structures generates a river of data. In fact, the bill of materials for a single fuselage alone can be millions of rows of data. In-house production processes and testing, as well as other manufacturers and customers created data flows that overwhelmed previous processes and information systems. Spirit’s customer base had grown substantially since their 2005 divestiture from Boeing, resulting in a $41 billion backlog of orders to fill. To address this backlog, meet increased customer demands and minimize additional capital investment, the company needed a way to improve throughput in the existing operational footprint. Spirit had a requirement from customers to increase fuselage production by 30%. To accomplish this goal, Spirit needed real-time information on its value chain and workflow. However, the two terabytes of data being pulled from their SAP ECC was unmanageable and overloaded their business warehouse. It had become time-consuming and difficult to pull aggregate data, disaggregate it for the needed information and then reassemble to create a report. During the 6-8 hours it took to build a report, another work shift (they run three per day) would have already taken place, thus the report content was out-of-date before it was ever delivered. As a result, supervisors often had to rely on manual efforts to provide charts, reports and analysis.