Company Size
200-1,000
Region
- Europe
Country
- Germany
Product
- DocuWare
Tech Stack
- ERP system B2 from Bäurer
- Data capturing program for measurements
Implementation Scale
- Enterprise-wide Deployment
Impact Metrics
- Cost Savings
- Productivity Improvements
Technology Category
- Application Infrastructure & Middleware - Data Exchange & Integration
Applicable Industries
- Automotive
Applicable Functions
- Discrete Manufacturing
- Quality Assurance
Use Cases
- Inventory Management
- Manufacturing System Automation
Services
- System Integration
About The Customer
Founded in 1989 in Bogen, Germany, TECHNO COLOR is specialized in finding ideal solutions for complicated painting/coating projects for the automobile industry. Their core business is the surface refinement of parts for the inside of automobiles through the use of environmentally friendly finishes. The manufacturers of the raw pieces (companies in the plastics and custom molding fields), supply such items as airbag covers, steering wheels or dashboards to TECHNO COLOR. In high-tech production lines, the pieces are painted, additional parts are mounted, and finished products are then sent to customers or directly to automobile manufacturers.
The Challenge
TECHNO COLOR's huge volume of documents had become increasingly problematic: every day, about 1,000 pages of paper were tucked into binders and stored throughout various departments. Records from recent years were clustered in huge wall systems, while older documents were stored in dedicated warehouse space on pallets. This was all done in order to meet the legal requirements in their industry for document retention. Aside from all the wasted space, this paper-based archive had another problem – the search time that employees used to find individual records. Even employees working on the same project often had to look through different departments for delivery slips, contracts, test results or measurement protocols. At that point, copies were often made, so that duplicates were again stored at someone's own desk. This did not, however, guarantee that the information they found was the most current - like whether new details were discussed with a client, if new parts were already announced or if a recall was expected.
The Solution
All incoming records, such as proof of delivery slips or accounts payable invoices, are labeled with a barcode, scanned and then filed automatically. Outgoing records created with their ERP system – such as shipping forms, orders, accounts receivable invoices, production documents and test reports from the lab – are stored fully automatically in DocuWare with the help of DocuWare's COLD/READ module. In this process, spool data created while printing is automatically imported; the search criteria needed for retrieval is then filtered from the information. Tedious and time-consuming filing and searching was eliminated and access to the whole system is now possible from every desk. The chaotic stacks of paper everywhere are gone. With the approximately 1,000 new documents that are now stored digitally every day, the company is saving enormously - both in paper and additional warehousing space. The internet-based workflow system integrated in DocuWare helps speed up the processing of documents. When a certain record type, such as an accounts payable invoice or delivery slip, enters the document pool, a workflow is automatically launched. The employees responsible for handling the document immediately receive notice on their screen. All of the following steps in the chain are clearly defined; employees are always able to see the current status of a document and the current task at hand. As soon as a task is completed, the document is automatically forwarded to the next pre-defined user.
Operational Impact
Quantitative Benefit
Case Study missing?
Start adding your own!
Register with your work email and create a new case study profile for your business.
Related Case Studies.
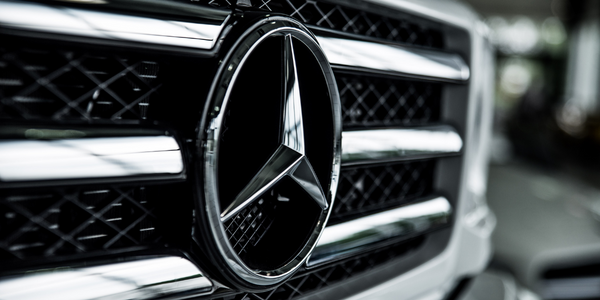
Case Study
Integral Plant Maintenance
Mercedes-Benz and his partner GAZ chose Siemens to be its maintenance partner at a new engine plant in Yaroslavl, Russia. The new plant offers a capacity to manufacture diesel engines for the Russian market, for locally produced Sprinter Classic. In addition to engines for the local market, the Yaroslavl plant will also produce spare parts. Mercedes-Benz Russia and his partner needed a service partner in order to ensure the operation of these lines in a maintenance partnership arrangement. The challenges included coordinating the entire maintenance management operation, in particular inspections, corrective and predictive maintenance activities, and the optimizing spare parts management. Siemens developed a customized maintenance solution that includes all electronic and mechanical maintenance activities (Integral Plant Maintenance).
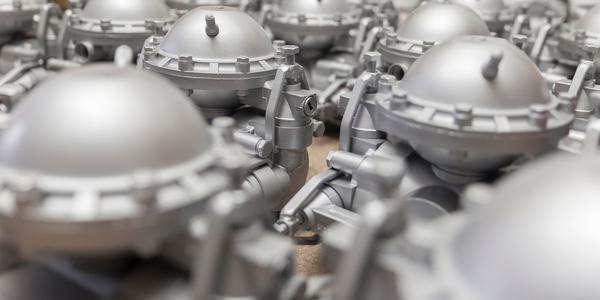
Case Study
Monitoring of Pressure Pumps in Automotive Industry
A large German/American producer of auto parts uses high-pressure pumps to deburr machined parts as a part of its production and quality check process. They decided to monitor these pumps to make sure they work properly and that they can see any indications leading to a potential failure before it affects their process.