Pyramid: Turning a Light On
Customer Company Size
Large Corporate
Region
- Europe
Country
- Ireland
Product
- Pyramid Analytics
Tech Stack
- Analytics Platform
- Data Visualization
Implementation Scale
- Enterprise-wide Deployment
Impact Metrics
- Productivity Improvements
- Digital Expertise
- Customer Satisfaction
Technology Category
- Application Infrastructure & Middleware - Data Visualization
- Analytics & Modeling - Predictive Analytics
Applicable Industries
- Automotive
Applicable Functions
- Sales & Marketing
- Business Operation
Services
- Software Design & Engineering Services
- System Integration
About The Customer
Volkswagen Group Ireland is a subsidiary of the global automotive giant Volkswagen Group, responsible for the distribution and sales of Volkswagen vehicles and parts in Ireland. The company manages a network of dealerships across the country, covering all five Volkswagen Group brands. With a focus on delivering high-quality vehicles and exceptional customer service, Volkswagen Group Ireland is committed to leveraging advanced technologies to enhance its operations and drive business success. The organization employs over 1,000 people and is dedicated to maintaining its position as a leader in the automotive industry through continuous innovation and strategic decision-making.
The Challenge
Before Pyramid, reporting consisted of hardcopies and emailed PDFs sent to dealerships (covering all five Volkswagen Group Ireland brands) that were then compiled centrally—a very labor-intensive activity. The transition to using Pyramid didn’t require months of adjustment, extensive training, or increased staffing. In fact, according to Volkswagen Group Ireland, “Users throughout the organization were able to use Pyramid really quickly. We didn’t need to send trainers onsite to educate people because there’s no big learning curve.”
The Solution
With Pyramid, Volkswagen Group Ireland is able to select which of those users see which content—from detailed analysis of individual parts, to summaries of dealer and brand performance. They can easily customize content relevant to specific users such as area managers and retailers, with confidence that protected data cannot be accessed by unintended users. In particular, dealers and brand managers were amazed by how easily and quickly they could gain insights into operational improvements and revenue opportunities. Executives and decision makers could now view the business in a comprehensive and granular way—all in one easy-to-navigate platform. With success that includes completing previously day-long analytical tasks in mere minutes, other successful projects are now also using the Pyramid platform. As a data-driven business, Volkswagen Group Ireland continues its world-class performance with faster, better decision making across the enterprise.
Operational Impact
Quantitative Benefit
Case Study missing?
Start adding your own!
Register with your work email and create a new case study profile for your business.
Related Case Studies.
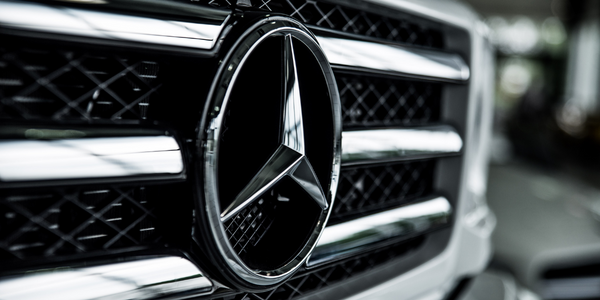
Case Study
Integral Plant Maintenance
Mercedes-Benz and his partner GAZ chose Siemens to be its maintenance partner at a new engine plant in Yaroslavl, Russia. The new plant offers a capacity to manufacture diesel engines for the Russian market, for locally produced Sprinter Classic. In addition to engines for the local market, the Yaroslavl plant will also produce spare parts. Mercedes-Benz Russia and his partner needed a service partner in order to ensure the operation of these lines in a maintenance partnership arrangement. The challenges included coordinating the entire maintenance management operation, in particular inspections, corrective and predictive maintenance activities, and the optimizing spare parts management. Siemens developed a customized maintenance solution that includes all electronic and mechanical maintenance activities (Integral Plant Maintenance).
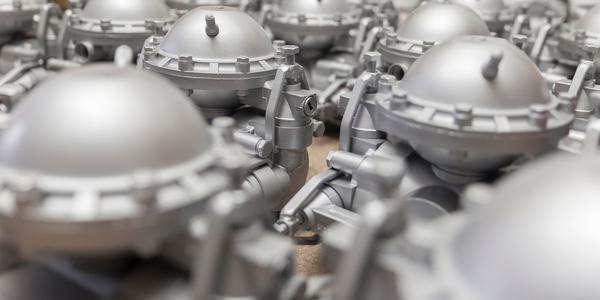
Case Study
Monitoring of Pressure Pumps in Automotive Industry
A large German/American producer of auto parts uses high-pressure pumps to deburr machined parts as a part of its production and quality check process. They decided to monitor these pumps to make sure they work properly and that they can see any indications leading to a potential failure before it affects their process.