Technology Category
- Robots - Wheeled Robots
Applicable Industries
- Cement
- Mining
Use Cases
- Onsite Human Safety Management
- Personnel Tracking & Monitoring
Services
- System Integration
- Training
About The Customer
Spartan Controls is an industrial services company with 14 locations across three provinces in Western Canada. They deliver innovation in industrial services to a multitude of customers in various industries, such as oil and gas, mining, and more. With a noble vision to create a safer and more sustainable world for their teams and customers, Spartan Controls is helping to protect people and the environment one customer at a time. They have been offering their services for over 60 years and have a workforce spread across multiple locations.
The Challenge
Spartan Controls, a company with 14 locations across three provinces, faced a significant challenge in managing safety across all sites using a paper and Excel-based safety system. This method resulted in administrative burden and efficiency losses, with most of their time spent managing paperwork and completing actions manually rather than focusing on key priorities. The paper-based system made it difficult to follow up on tasks and provide feedback or corrective actions to teams based on forms submitted. With a workforce spread across multiple locations, participation and connection amongst teams were harder to gauge. The paper-based system also made employees feel there was no feedback loop when forms were submitted, resulting in lower safety engagement. Employees traveling from site to site had to manually manage hazard reports and inspections, which was inefficient and led to a safety culture that was not at its highest potential. Manual processes and Excel spreadsheets also led to little insight into safety metrics and KPIs, making it difficult to track data and build reports.
The Solution
Spartan Controls has now completely digitised and centralised all their safety information and data into one easily accessible digital solution, making them completely paperless. This has helped to streamline their processes as everything is now automated. Employees can complete inspections and forms within the system, hit submit, and drive the necessary corrective actions. eCompliance has helped connect their teams as they all work within one system. With a mobile workforce, the mobile app has been essential as it offers offline capabilities and is extremely user-friendly. Employees can easily complete forms and inspections as it is now at their fingertips. This has resulted in a shift in the safety culture with increased engagement and reporting. The robust reporting engine and advanced analytics capabilities have also given the team a chance to gain greater visibility into their safety program. This has allowed them to be more proactive and track trends and patterns to efficiently protect their teams and customers.
Operational Impact
Quantitative Benefit
Case Study missing?
Start adding your own!
Register with your work email and create a new case study profile for your business.
Related Case Studies.

Case Study
System 800xA at Indian Cement Plants
Chettinad Cement recognized that further efficiencies could be achieved in its cement manufacturing process. It looked to investing in comprehensive operational and control technologies to manage and derive productivity and energy efficiency gains from the assets on Line 2, their second plant in India.
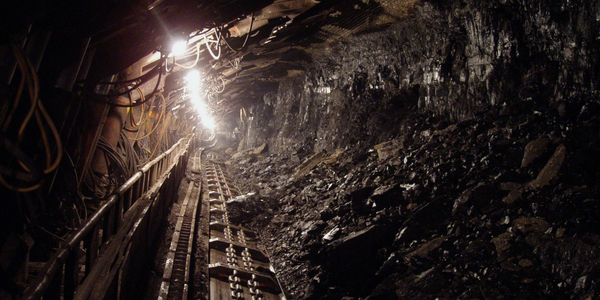
Case Study
Underground Mining Safety
The goal was to produce a safety system to monitor and support underground mining operations; existing systems were either too simple (i.e. phone line) or overly complex and expensive, inhibiting deployment, and providing little-to-no support in event of an accident. Given the dangerous nature of the mining work environment and the strict regulations placed on the industry, the solution would have to comply with Mine Safety and Health Administration (MSHA) regulations. Yet the product needed to allow for simple deployment to truly be a groundbreaking solution - increasing miner safety and changing daily operations for the better.
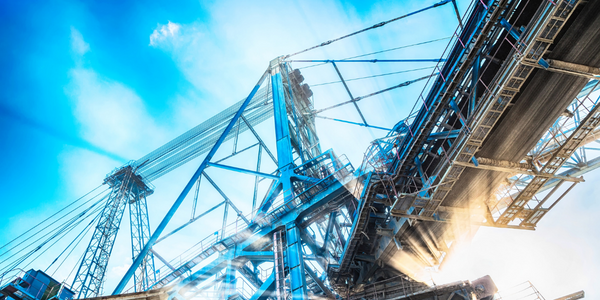
Case Study
Mining Firm Quadruples Production, with Internet of Everything
Dundee Precious Metal’s flagship mine, in Chelopech, Bulgaria, produces a gold, copper, and silver concentrate set a goal to increase production by 30%. Dundee wanted to increase production quality and output without increasing headcount and resources, improve miner safety, and minimize cost.
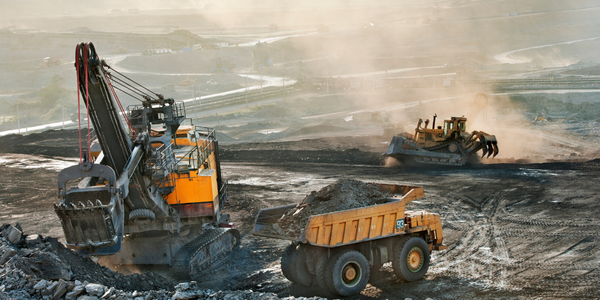
Case Study
Fastenal Builds the Future of Manufacturing with MachineMetrics
Fastenal's objective was to better understand their machine downtime, utilization, quality issues, and to embrace cutting-edge manufacturing technology/process improvement capabilities to bring their team to the next level. However, there was a lack of real-time data, visualization, and actionable insights made this transition impossible.
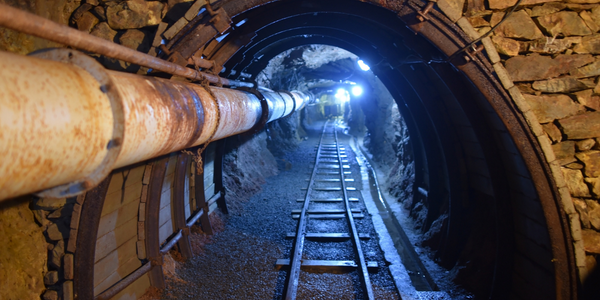
Case Study
Joy Mining Systems
Joy equipment faces many challenges. The first is machine integration and control. The business end of the machine has a rapidly-spinning cylinder with 6-inch diamond-studded cutting teeth. It chews through rock at rates measured in tens of tons per minute. The system grinds through the rock in front, creating a rectangular mine tunnel. Hydraulic lifters support the ceiling as the machine moves forward. Automated drills and screws drive 3-ft long screws into the ceiling to stabilize it. The rock and coal fall into a set of gathering "fingers" below the cutting cylinder. These fingers scoop up the rock and coal and deposit it onto a conveyor belt. The conveyor passes under the machine and out the back. A train of conveyor belt cars, up to a mile long, follows the cutter into the mine. The rock shoots along this train at over 400 feet per minute until it empties into rail cars at the end. Current systems place an operator cage next to the cutter. Choking dust (potentially explosive), the risk of collapse and the proximity of metal and rock mayhem make the operator cage a hazardous location.