Outsourcing Generates Supply Chain Efficiencies
Customer Company Size
Large Corporate
Region
- America
- Asia
Country
- United States
- Vietnam
Product
- Navisphere
Tech Stack
- Electronic Data Interchange (EDI)
- Optimization Tool
- ERP System
Implementation Scale
- Enterprise-wide Deployment
Impact Metrics
- Cost Savings
- Customer Satisfaction
- Productivity Improvements
Technology Category
- Functional Applications - Enterprise Resource Planning Systems (ERP)
- Analytics & Modeling - Predictive Analytics
Applicable Industries
- Transportation
Applicable Functions
- Logistics & Transportation
- Warehouse & Inventory Management
Use Cases
- Supply Chain Visibility
- Inventory Management
- Predictive Maintenance
Services
- System Integration
- Cloud Planning, Design & Implementation Services
- Training
About The Customer
Toshiba International Corporation’s Motor Business Unit (MBU) is a global leader in the design, manufacture, and sale of electric motors. With a production system extending from Japan to China and Vietnam to Texas, Toshiba’s MBU depends on flawless logistics processes to support their aggressive growth goals and maintain service and quality standards. In 2010, Toshiba moved some manufacturing for premium industrial motors from Houston to a factory strategically located near Ho Chi Minh City, Vietnam’s international port. The new Vietnam plant was planned to ship up to 1.2 million motors a year to the global market. Toshiba’s MBU in Houston sought to resolve cost and service failures with their incumbent logistics provider and needed a highly efficient, collaborative supply chain relationship to support their growth goals.
The Challenge
With a global footprint and production system extending from Japan to China and Vietnam to Texas, the Motor Business Unit (MBU) of Toshiba International Corporation’s (Toshiba’s) Industrial Division depends on flawless logistics processes. In 2010, Toshiba moved some manufacturing for premium industrial motors from Houston to a factory strategically located near Ho Chi Minh City, Vietnam’s international port. With plans for the new Vietnam plant to ship up to 1.2 million motors a year to the global market, Toshiba needed a highly efficient, collaborative supply chain relationship to support their aggressive growth goals and maintain service and quality standards.\n\nToshiba’s MBU in Houston searched for a solution to resolve cost and service failures with the incumbent logistics provider. With limited tracking and traceability, poorly defined and followed standard operating procedures (SOPs), a narrow focus on inbound transportation, and no visibility to freight costs, leadership felt the lack of internal supply chain expertise hindered their ability to grow. They needed creative solutions.
The Solution
C.H. Robinson, having successfully handled domestic truckload needs for Toshiba since 2007, was invited to bid for a portion of Toshiba’s international business transportation spend — both inbound and outbound. Toshiba looked for a truly collaborative outsource to reduce costs, add automation and visibility through technology, and improve processes. The solution included supply chain consulting and account management to identify, improve, and standardize global organizational processes, technology to automate orders for eight commodities to eliminate manual entries and quickly provide visibility to the order cycle, and a strategy to reduce transportation costs while improving customer service.\n\nThe transition team developed a detailed onboarding plan, including mapping process flows for the order cycle, gap analysis, testing, training, measurement, improvement, and constant communication. One of the first actions was to create a process for shipping from Vietnam to Houston, or anywhere in North America. The collaborative team documented the necessary shipping steps and created SOPs from the bonded warehouse to customer locations. C.H. Robinson also worked with inventory control in Houston for product dimensions; the information was then fed into an optimization tool to create container diagrams. The new container process yielded positive outcomes — shipment weights in legal limits and containers loaded based on specific diagrams to maximize space, minimize the number of containers, and reduce costs.
Operational Impact
Quantitative Benefit
Case Study missing?
Start adding your own!
Register with your work email and create a new case study profile for your business.
Related Case Studies.
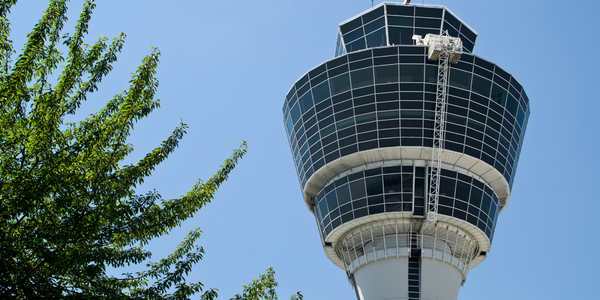
Case Study
Airport SCADA Systems Improve Service Levels
Modern airports are one of the busiest environments on Earth and rely on process automation equipment to ensure service operators achieve their KPIs. Increasingly airport SCADA systems are being used to control all aspects of the operation and associated facilities. This is because unplanned system downtime can cost dearly, both in terms of reduced revenues and the associated loss of customer satisfaction due to inevitable travel inconvenience and disruption.
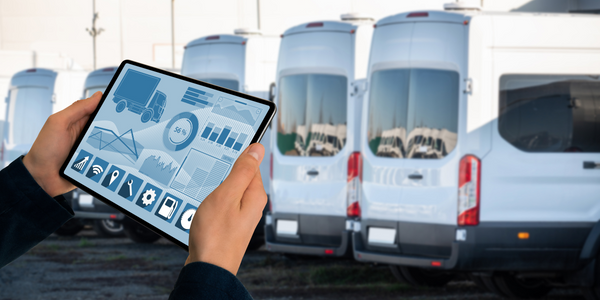
Case Study
IoT-based Fleet Intelligence Innovation
Speed to market is precious for DRVR, a rapidly growing start-up company. With a business model dependent on reliable mobile data, managers were spending their lives trying to negotiate data roaming deals with mobile network operators in different countries. And, even then, service quality was a constant concern.
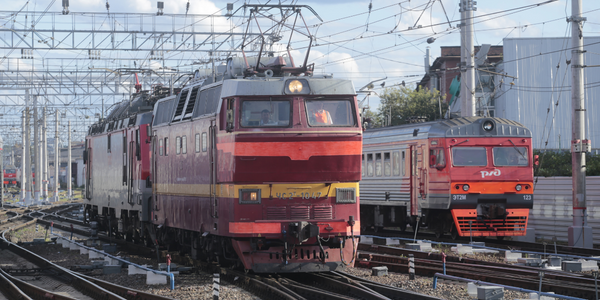
Case Study
Digitize Railway with Deutsche Bahn
To reduce maintenance costs and delay-causing failures for Deutsche Bahn. They need manual measurements by a position measurement system based on custom-made MEMS sensor clusters, which allow autonomous and continuous monitoring with wireless data transmission and long battery. They were looking for data pre-processing solution in the sensor and machine learning algorithms in the cloud so as to detect critical wear.
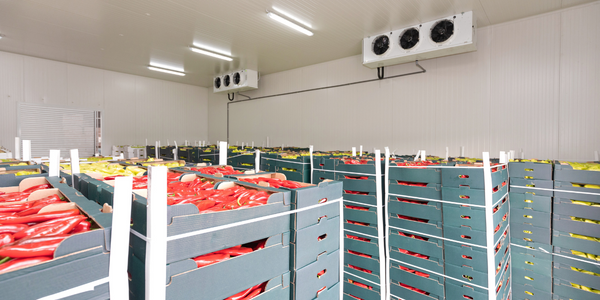
Case Study
Cold Chain Transportation and Refrigerated Fleet Management System
1) Create a digital connected transportation solution to retrofit cold chain trailers with real-time tracking and controls. 2) Prevent multi-million dollar losses due to theft or spoilage. 3) Deliver a digital chain-of-custody solution for door to door load monitoring and security. 4) Provide a trusted multi-fleet solution in a single application with granular data and access controls.
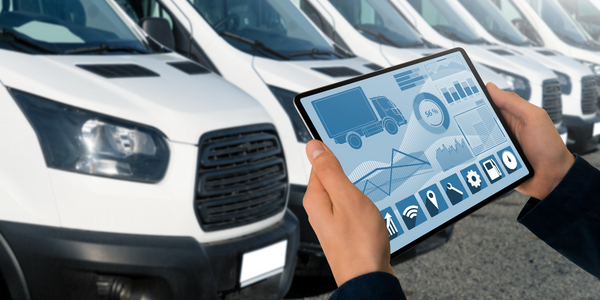
Case Study
Vehicle Fleet Analytics
Organizations frequently implement a maintenance strategy for their fleets of vehicles using a combination of time and usage based maintenance schedules. While effective as a whole, time and usage based schedules do not take into account driving patterns, environmental factors, and sensors currently deployed within the vehicle measuring crank voltage, ignition voltage, and acceleration, all of which have a significant influence on the overall health of the vehicle.In a typical fleet, a large percentage of road calls are related to electrical failure, with battery failure being a common cause. Battery failures result in unmet service agreement levels and costly re-adjustment of scheduled to provide replacement vehicles. To reduce the impact of unplanned maintenance, the transportation logistics company was interested in a trial of C3 Vehicle Fleet Analytics.
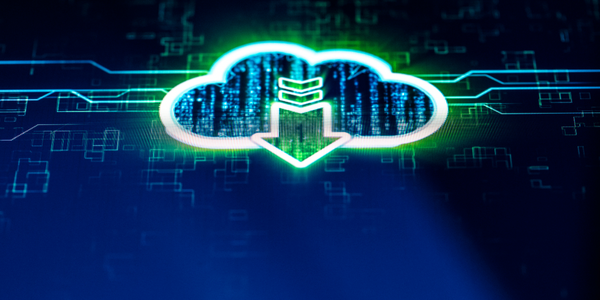
Case Study
3M Gains Real-Time Insight with Cloud Solution
The company has a long track record of innovative technology solutions. For example, 3M helps its customers optimize parking operations by automating fee collection and other processes. To improve support for this rapidly expanding segment, 3M needed to automate its own data collection and reporting. The company had recently purchased the assets of parking, tolling, and automatic license plate reader businesses, and required better insight into these acquisitions. Chad Reed, Global Business Manager for 3M Parking Systems, says, “With thousands of installations across the world, we couldn’t keep track of our software and hardware deployments, which made it difficult to understand our market penetration.” 3M wanted a tracking application that sales staff could use to get real-time information about the type and location of 3M products in parking lots and garages. So that it could be used on-site with potential customers, the solution would have to provide access to data anytime, anywhere, and from an array of mobile devices. Jason Fox, Mobile Application Architect at 3M, upped the ante by volunteering to deliver the new app in one weekend. For Fox and his team, these requirements meant turning to the cloud instead of an on-premises datacenter. “My first thought was to go directly to the cloud because we needed to provide access not only to our salespeople, but to resellers who didn’t have access to our internal network,” says Fox. “The cloud just seemed like a logical choice.”