Technology Category
- Functional Applications - Computerized Maintenance Management Systems (CMMS)
- Functional Applications - Transportation Management Systems (TMS)
Applicable Industries
- Renewable Energy
- Transportation
Applicable Functions
- Maintenance
- Product Research & Development
Use Cases
- Construction Management
- Transportation Simulation
About The Customer
Thesan is an Italian company based in Chiusa di San Michele that designs, manufactures, and distributes mounting structures for photovoltaic plants. In addition, the company also develops, constructs, and operates renewable energy power plants, including photovoltaic and mini-hydroelectric power plants. Thesan was founded in 2008 and operates as a subsidiary of Savio Spa, a global manufacturer and foremost specialist in hardware for aluminum windows and doors, with factories in Italy, China, and India. Drawing on the Savio Group’s competence in the design of steel and aluminum structures and thanks to a team of over 40 engineers, Thesan is able to satisfy every construction requirement of photovoltaic power plants at all altitude and climatic conditions, using any specific fixation requirements. The company provides the technical expertise and the corresponding experience to follow all phases of the production chain; from project development to construction, management to maintenance of the power plant.
The Challenge
Thesan, an Italian company specializing in the design, manufacture, and distribution of mounting structures for photovoltaic plants, was faced with the challenge of optimizing the mounting structure of a medium-sized PV field with a power of 5 MW. The field consisted of 1700 arrays, each mounted on two poles, with each individual assembled structure weighing about 60 kg. The total weight of the mounted structures on the field was 204 tons of steel, with material costs of about 170,000 Euro. A weight reduction of only 5 kg per structure would lead to significant savings in material and cost. The structure was composed of two main parts, a steel driven pile and an aluminum rafter, with the weight reduction of the more costly aluminum parts being crucial. Another significant factor for cost savings was transportation, as PV fields are often built in remote areas with poor infrastructure. Lighter structures would not only mean less material costs in production, but also lower transportation efforts and costs. However, the new, lighter weight structures still had to be able to carry all occurring loads from natural causes such as wind or snow and the dead load of the structure, ensuring perfect quality, consistent stability and the requested stiffness of the structures.
The Solution
To reduce the weight of the overall structure while still ensuring stiffness and safety, the engineers at Thesan identified the profile of a mounting part (rafter), which is used to connect the solar panels to the support poles, as offering the highest potential for weight savings via structural optimization. They used OptiStruct®, the optimization tool and FE-solver included in Altair‘s HyperWorks® suite, to optimize the rafter component. They created a design space, added boundary conditions and loads such as those coming from snow, wind, and dead loads, and varied the wall thicknesses and the overall shape of the profile to minimize weight while keeping stresses and displacements within an acceptable level. The optimization results proposed a new profile design, with a decreased upper, lateral, and lower wall thickness and an overall increased height as well as an increased lower section. The new design was then verified with FE analysis to assure its stiffness and safety at possible angles and occurring loads. A similar strategy was then applied to reduce thickness and optimize the shape of the steel structure, leading to a light but nonetheless reliable and safe structure.
Operational Impact
Quantitative Benefit
Case Study missing?
Start adding your own!
Register with your work email and create a new case study profile for your business.
Related Case Studies.

Case Study
Remote Monitoring & Predictive Maintenance App for a Solar Energy System
The maintenance & tracking of various modules was an overhead for the customer due to the huge labor costs involved. Being an advanced solar solutions provider, they wanted to ensure early detection of issues and provide the best-in-class customer experience. Hence they wanted to automate the whole process.
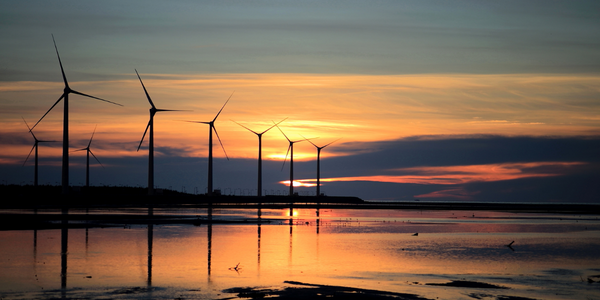
Case Study
Vestas: Turning Climate into Capital with Big Data
Making wind a reliable source of energy depends greatly on the placement of the wind turbines used to produce electricity. Turbulence is a significant factor as it strains turbine components, making them more likely to fail. Vestas wanted to pinpoint the optimal location for wind turbines to maximize power generation and reduce energy costs.
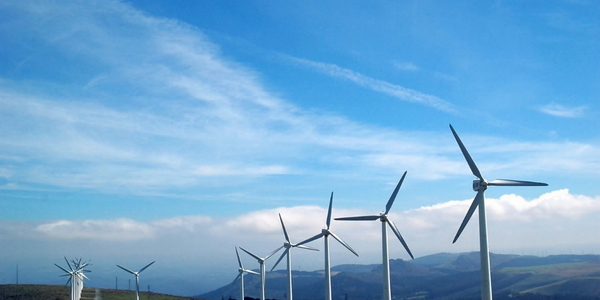
Case Study
Siemens Wind Power
Wind provides clean, renewable energy. The core concept is simple: wind turbines spin blades to generate power. However, today's systems are anything but simple. Modern wind turbines have blades that sweep a 120 meter circle, cost more than 1 million dollars and generate multiple megawatts of power. Each turbine may include up to 1,000 sensors and actuators – integrating strain gages, bearing monitors and power conditioning technology. The turbine can control blade speed and power generation by altering the blade pitch and power extraction. Controlling the turbine is a sophisticated job requiring many cooperating processors closing high-speed loops and implementing intelligent monitoring and optimization algorithms. But the real challenge is integrating these turbines so that they work together. A wind farm may include hundreds of turbines. They are often installed in difficult-to-access locations at sea. The farm must implement a fundamentally and truly distributed control system. Like all power systems, the goal of the farm is to match generation to load. A farm with hundreds of turbines must optimize that load by balancing the loading and generation across a wide geography. Wind, of course, is dynamic. Almost every picture of a wind farm shows a calm sea and a setting sun. But things get challenging when a storm goes through the wind farm. In a storm, the control system must decide how to take energy out of gusts to generate constant power. It must intelligently balance load across many turbines. And a critical consideration is the loading and potential damage to a half-billion-dollar installed asset. This is no environment for a slow or undependable control system. Reliability and performance are crucial.
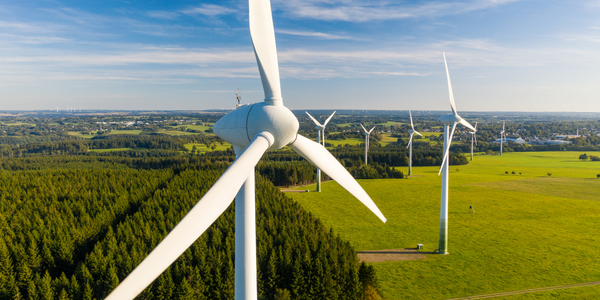
Case Study
Remote Monitoring and Control for a Windmill Generator
As concerns over global warming continue to grow, green technologies are becoming increasingly popular. Wind turbine companies provide an excellent alternative to burning fossil fuels by harnessing kinetic energy from the wind and converting it into electricity. A typical wind farm may include over 80 wind turbines so efficient and reliable networks to manage and control these installations are imperative. Each wind turbine includes a generator and a variety of serial components such as a water cooler, high voltage transformer, ultrasonic wind sensors, yaw gear, blade bearing, pitch cylinder, and hub controller. All of these components are controlled by a PLC and communicate with the ground host. Due to the total integration of these devices into an Ethernet network, one of our customers in the wind turbine industry needed a serial-to-Ethernet solution that can operate reliably for years without interruption.
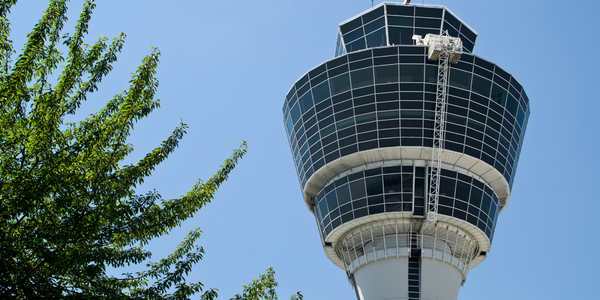
Case Study
Airport SCADA Systems Improve Service Levels
Modern airports are one of the busiest environments on Earth and rely on process automation equipment to ensure service operators achieve their KPIs. Increasingly airport SCADA systems are being used to control all aspects of the operation and associated facilities. This is because unplanned system downtime can cost dearly, both in terms of reduced revenues and the associated loss of customer satisfaction due to inevitable travel inconvenience and disruption.
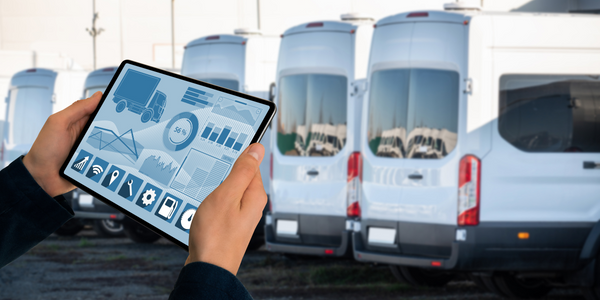
Case Study
IoT-based Fleet Intelligence Innovation
Speed to market is precious for DRVR, a rapidly growing start-up company. With a business model dependent on reliable mobile data, managers were spending their lives trying to negotiate data roaming deals with mobile network operators in different countries. And, even then, service quality was a constant concern.