Norauto Revs Up Supply Chain Performance With Manhattan Associates
Customer Company Size
Large Corporate
Region
- Europe
- America
Country
- France
- Poland
- Spain
Product
- Manhattan Warehouse Management
- Manhattan Slotting Optimisation
- Vocollect Voice-Recognition Technology
Tech Stack
- IBM System p
- SAP ERP
- Voice-Recognition Technology
Implementation Scale
- Enterprise-wide Deployment
Impact Metrics
- Productivity Improvements
- Cost Savings
- Customer Satisfaction
Technology Category
- Functional Applications - Warehouse Management Systems (WMS)
- Application Infrastructure & Middleware - Data Exchange & Integration
- Functional Applications - Inventory Management Systems
Applicable Industries
- Automotive
- Retail
Applicable Functions
- Logistics & Transportation
- Warehouse & Inventory Management
Use Cases
- Inventory Management
- Warehouse Automation
- Supply Chain Visibility
Services
- System Integration
- Software Design & Engineering Services
About The Customer
Norauto, established in 1970, is a leading international company in the European car maintenance and equipment market. With operations in eight countries across Europe and South America, Norauto has experienced significant growth. The company has expanded its portfolio through acquisitions and the launch of discount operator Carter Cash, doubling its revenues and tripling the number of outlets. Norauto relies on five warehouses in France, Spain, and Poland to supply goods to over 350 automotive stores in its core markets.
The Challenge
Norauto’s expensive and inefficient proprietary warehouse system had become obsolete. The company needed to support its growth and replace the outdated system to improve operational productivity, comply with automotive sector tracking standards, and achieve a 99.9% order accuracy in the fulfillment process. The goal was to implement a reliable and upgradable supply chain execution system.
The Solution
Norauto selected Manhattan Associates’ Warehouse Management solution to replace its obsolete system. The solution was deployed at the 13,000m2 Lesquin warehouse in France and integrated seamlessly with Norauto’s SAP ERP system. This integration allowed for efficient data exchange between supply chain execution applications and back-office systems. Additionally, Vocollect’s voice-recognition technology was implemented to enhance picking operations. The combined technologies provided Norauto with the ability to manage the flow of goods across the supply chain, optimize inventory levels, and streamline inbound goods processing.
Operational Impact
Quantitative Benefit
Case Study missing?
Start adding your own!
Register with your work email and create a new case study profile for your business.
Related Case Studies.
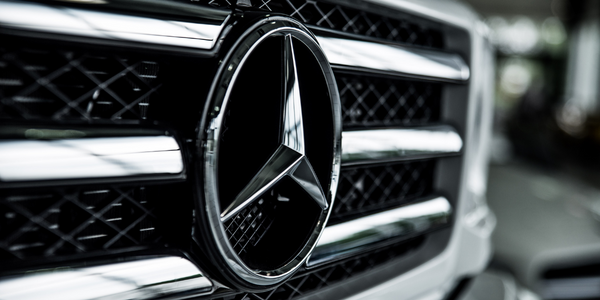
Case Study
Integral Plant Maintenance
Mercedes-Benz and his partner GAZ chose Siemens to be its maintenance partner at a new engine plant in Yaroslavl, Russia. The new plant offers a capacity to manufacture diesel engines for the Russian market, for locally produced Sprinter Classic. In addition to engines for the local market, the Yaroslavl plant will also produce spare parts. Mercedes-Benz Russia and his partner needed a service partner in order to ensure the operation of these lines in a maintenance partnership arrangement. The challenges included coordinating the entire maintenance management operation, in particular inspections, corrective and predictive maintenance activities, and the optimizing spare parts management. Siemens developed a customized maintenance solution that includes all electronic and mechanical maintenance activities (Integral Plant Maintenance).
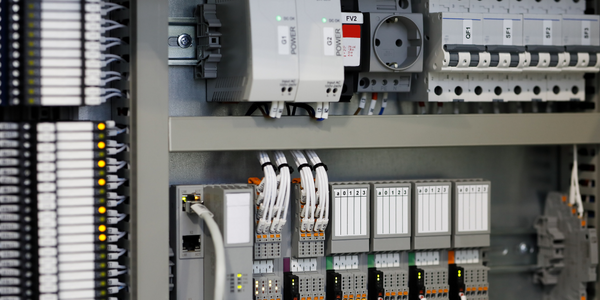
Case Study
Improving Production Line Efficiency with Ethernet Micro RTU Controller
Moxa was asked to provide a connectivity solution for one of the world's leading cosmetics companies. This multinational corporation, with retail presence in 130 countries, 23 global braches, and over 66,000 employees, sought to improve the efficiency of their production process by migrating from manual monitoring to an automatic productivity monitoring system. The production line was being monitored by ABB Real-TPI, a factory information system that offers data collection and analysis to improve plant efficiency. Due to software limitations, the customer needed an OPC server and a corresponding I/O solution to collect data from additional sensor devices for the Real-TPI system. The goal is to enable the factory information system to more thoroughly collect data from every corner of the production line. This will improve its ability to measure Overall Equipment Effectiveness (OEE) and translate into increased production efficiencies. System Requirements • Instant status updates while still consuming minimal bandwidth to relieve strain on limited factory networks • Interoperable with ABB Real-TPI • Small form factor appropriate for deployment where space is scarce • Remote software management and configuration to simplify operations