Customer Company Size
Large Corporate
Region
- Asia
- Africa
- Middle East
Country
- India
Product
- Lectra Cutting Room Technology
- Lectra Patternmaking Technology
Tech Stack
- Automated Pattern Making
- Automated Marker Making
- Automated Cut Planning
- Automated Spreading
Implementation Scale
- Enterprise-wide Deployment
Impact Metrics
- Productivity Improvements
- Cost Savings
- Customer Satisfaction
- Environmental Impact Reduction
Technology Category
- Functional Applications - Product Lifecycle Management Systems (PLM)
- Functional Applications - Manufacturing Execution Systems (MES)
- Functional Applications - Remote Monitoring & Control Systems
Applicable Industries
- Apparel
- Consumer Goods
Applicable Functions
- Discrete Manufacturing
- Quality Assurance
- Warehouse & Inventory Management
Use Cases
- Predictive Maintenance
- Inventory Management
- Manufacturing System Automation
- Process Control & Optimization
Services
- System Integration
- Software Design & Engineering Services
- Training
About The Customer
Maxwell Industries is a vertically-integrated fashion company based in Mumbai, India, specializing in the design, manufacture, and retail of affordable, quality undergarments for men, women, and children. The company produces over 37 million pieces annually for brands such as VIP Innerwear, Frenchie, Frenchie X, and VIP Feeling. Approximately 70% of its products are sold in the local market through more than 110,000 points of sale, including its own-name stores, while the remaining 30% are exported to other countries. Maxwell Industries is a household name in the local undergarment industry and aims to expand its presence in India, Africa, and the Middle East. The company is committed to maintaining high-quality standards and has a strong focus on sustainability and efficiency in its operations.
The Challenge
Maxwell Industries, based in Mumbai, India, designs, manufactures, and retails affordable, quality undergarments for men, women, and children. The company produces over 37 million pieces a year for brands such as VIP Innerwear, Frenchie, Frenchie X, and VIP Feeling. Approximately 70% of its product is destined for more than 110,000 points of sale in the local market, including the company’s own-name stores, while the remaining 30% is exported to other countries. Maxwell Industries wanted to expand its presence in India and its two other main markets: Africa and the Middle East. To do this, it needed to replace its partially-outsourced, manual process with an automated lean pre-production process that would streamline operations and reduce costs, without sacrificing the quality on which the company had built its reputation.
The Solution
Maxwell Industries partnered with Lectra to improve their development process and boost productivity in their cutting room at their main plant in Thingalur. Lectra conducted an in-depth analysis and worked with Maxwell to create a customized action plan that would allow them to move all their cutting in-house and automate certain aspects of development and production. With Lectra’s support, Maxwell was able to automate its pattern making, marker making, spreading, cut planning, and cutting. Lectra’s integrated solutions also streamlined communication across the company’s different departments. The changes allowed Maxwell to speed up its development process, reduce fabric consumption by 5%, and produce a better quality product with fewer errors. This gave Maxwell the agility needed to pursue its expansion goals. The company was so impressed with the results that it decided to roll out a similar project in its Umbergoan, Gujarat facility.
Operational Impact
Quantitative Benefit
Case Study missing?
Start adding your own!
Register with your work email and create a new case study profile for your business.
Related Case Studies.
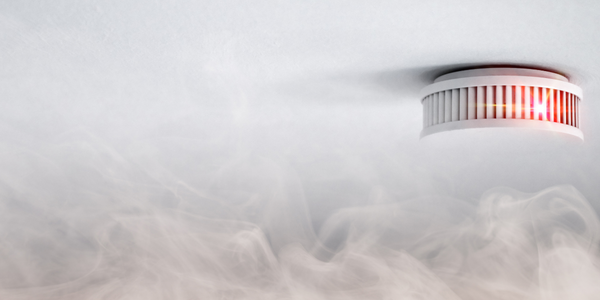
Case Study
Fire Alarm System and Remote Monitoring Sytem
Fire alarm systems are essential in providing an early warning in the event of fire. They help to save lives and protect property whilst also fulfilling the needs of insurance companies and government departments.Fire alarm systems typically consist of several inter-linked components, such as smoke detectors, heat detector, carbon monoxide, manual call points, sounders, alarm and buzzer. The fire alarm system should give immediate information in order to prevent the fire spread and protect live and property.To get maximum protection a shoe manufacturer in Indonesia opted for a new fire alarm system to monitor 13 production sites spread over 160 hectars. Although the company had an existing fire alarm system, it could not be monitored remotely.It was essential that the new system would be able to be monitored from a central control room. It needed to be able to connect to the existing smoke detector and manual call point. Information should be easily collected and passed on to the Supervisory Control and Data Acquisition (SCADA) system. Furthermore, the system should have several features such as alarm management, auto reporting, being connected to many client computers without additional cost, and run 24/7 without fails. The company also needed a system which could be implemented without changing the architecture of the existing fire alarm system.
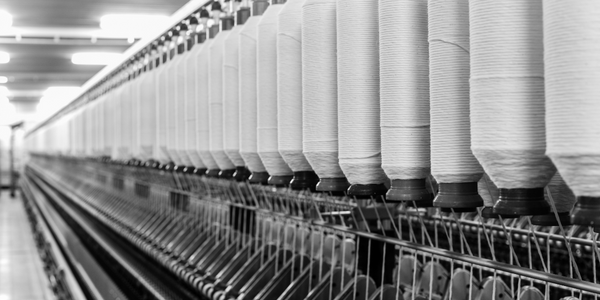
Case Study
IoT Applications and Upgrades in Textile Plant
At any given time, the textile company’s manufacturing facility has up to 2,000 textile carts in use. These carts are pushed from room to room, carrying materials or semi-finished products. Previously, a paper with a hand-written description was attached to each cart. This traditional method of processing made product tracking extremely difficult. Additionally, making sure that every cart of materials or semi-finished products went to its correct processing work station was also a problem. Therefore, the company desired an intelligent solution for tracking assets at their factories. They also wanted a solution that would help them collect process data so they could improve their manufacturing efficiency.
.png)
Case Study
Improving Vending Machine Profitability with the Internet of Things (IoT)
The vending industry is undergoing a sea change, taking advantage of new technologies to go beyond just delivering snacks to creating a new retail location. Intelligent vending machines can be found in many public locations as well as company facilities, selling different types of goods and services, including even computer accessories, gold bars, tickets, and office supplies. With increasing sophistication, they may also provide time- and location-based data pertaining to sales, inventory, and customer preferences. But at the end of the day, vending machine operators know greater profitability is driven by higher sales and lower operating costs.
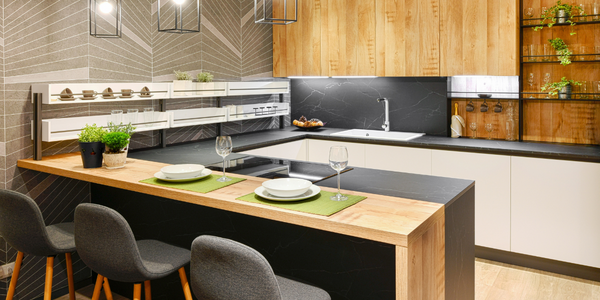
Case Study
Series Production with Lot-size-1 Flexibility
Nobilia manufactures customized fitted kitchens with a lot size of 1. They require maximum transparency of tracking design data and individual processing steps so that they can locate a particular piece of kitchen furniture in the sequence of processes.
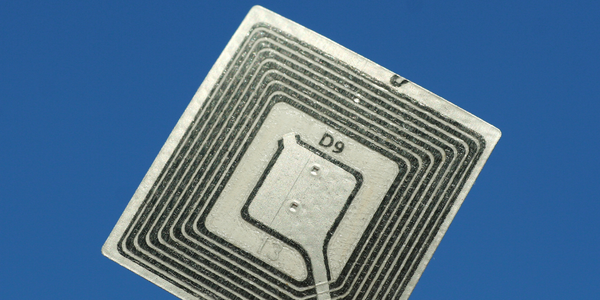
Case Study
Retailer Uses RFID Scanner to Improve Efficiency
Patrizia Pepe wished to improve the logistics of their warehouse: accepting incoming goods from their production sites, movement of items throughout
the warehouse, and packaging of goods for distribution to the retail locations. They initially tried to use barcodes for this function. Because barcodes must be individually scanned within a line-of-sight, the acceptance of goods coming into the warehouse was too time consuming. Working with the University of Florence, Patrizia Pepe instituted a five-month pilot project beginning in August of 2009 to test the validity of an RFID solution. The pilot involved tagging of about 60,000 items for the second seasonal collection, and convinced the company to move forward with tagging all items.