Maintenance intervention planning: a strategic challenge for ENGIE Solutions
Company Size
1,000+
Region
- Europe
Country
- France
Product
- Geoconcept Opti-Time
Tech Stack
- Geoconcept Opti-Time
- GSM Network
- Machine Learning
Implementation Scale
- Enterprise-wide Deployment
Impact Metrics
- Customer Satisfaction
- Environmental Impact Reduction
- Productivity Improvements
Technology Category
- Analytics & Modeling - Machine Learning
- Functional Applications - Remote Monitoring & Control Systems
Applicable Industries
- Buildings
- Utilities
Applicable Functions
- Facility Management
- Maintenance
Use Cases
- Fleet Management
- Predictive Maintenance
- Remote Asset Management
Services
- Software Design & Engineering Services
- System Integration
About The Customer
ENGIE Solutions is a part of the ENGIE group, which focuses on B2B energy operations. The company has restructured its operations to be more customer-focused, organizing its work streams into three business units: Town and Local Authorities, Industry, and the Tertiary and Proximity sector. ENGIE Solutions employs 7,000 technical staff and field workers who carry out installation maintenance for a wide range of customers. The company handles a multitude of installations, including boilers in residential buildings, air-cooling towers on industrial sites, cogeneration power systems, and heating and refrigeration networks. Each installation is managed by an agent, and technicians are assigned to service a certain number of installations. The company aims to ensure the nominal operation of all installations while complying with various environmental, operational, and health & safety regulations.
The Challenge
ENGIE Solutions faces the challenge of managing a diverse range of installations, including boilers, air-cooling towers, cogeneration power systems, and heating and refrigeration networks. Each installation requires different types of expertise and is subject to various regulations, making the scheduling of maintenance interventions complex. The company needs to ensure that all regulatory visits and operational maintenance interventions are carried out on time, while also taking into account customer constraints and the legal number of working hours per day. Additionally, the company aims to achieve convergence of tools and processes across its agencies to improve efficiency and service delivery.
The Solution
ENGIE Solutions uses Geoconcept's Opti-Time solution for scheduling and dispatching maintenance interventions. The scheduling teams draw up weekly, monthly, quarterly, and biannual maintenance visits as stipulated by the maintenance contracts. They establish an annual schedule that serves as a baseline for smoothing the technical workload and incorporate any contingencies during the week. Dispatchers handle corrective interventions, analyzing customer requests and assigning tasks to technicians based on urgency and availability. Mobile field technicians are equipped with tablets that have internally developed software and access to the Opti-Time interface. This allows them to access their schedules, carry out monitoring and surveillance tasks, and upload start and finish times for each intervention. The mobile device is synced to a GSM network, enabling real-time communication between technicians and the scheduling unit. The company is also exploring additional features of Opti-Time, such as real-time traffic monitoring and vehicle tracking, to further optimize technician workload and reduce journey times.
Operational Impact
Quantitative Benefit
Case Study missing?
Start adding your own!
Register with your work email and create a new case study profile for your business.
Related Case Studies.

Case Study
IoT Solutions for Smart City | Internet of Things Case Study
There were several challenges faced: It is challenging to build an appliance that can withstand a wide range of voltage fluctuations from as low at 90v to as high as 320v. Since the device would be installed in remote locations, its resilience was of paramount importance. The device would have to deal with poor network coverage and have the ability to store and re-transmit data if networks were not available, which is often the case in rural India. The device could store up to 30 days of data.

Case Study
Automation of the Oguz-Gabala-Baku water pipeline, Azerbaijan
The Oguz-Gabala-Baku water pipeline project dates back to plans from the 1970’s. Baku’s growth was historically driven by the booming oil industry and required the import of drinking water from outside of the city. Before the construction of the pipeline, some 60 percent of the city’s households received water for only a few hours daily. After completion of the project, 75 percent of the two million Baku residents are now served around the clock with potable water, based on World Health Organization (WHO) standards. The 262-kilometer pipeline requires no pumping station, but uses the altitude differences between the Caucasian mountains and the capital to supply 432,000 m³/d to the Ceyranbatan water reservoir. To the people of Baku, the pipeline is “the most important project not only in 2010, but of the last 20 years.”

Case Study
GPRS Mobile Network for Smart Metering
Around the world, the electricity supply industry is turning to ‘smart’ meters to lower costs, reduce emissions and improve the management of customer supplies. Smart meters collect detailed consumption information and using this feedback consumers can better understand their energy usage which in turn enables them to modify their consumption to save money and help to cut carbon emissions. A smart meter can be defined in many ways, but generally includes an element of two-way communication between the household meter and the utility provider to efficiently collect detailed energy usage data. Some implementations include consumer feedback beyond the energy bill to include online web data, SMS text messages or an information display in consumers’ premises. Providing a cost-effective, reliable communications mechanism is one of the most challenging aspects of a smart meter implementation. In New Zealand, the utilities have embraced smart metering and designed cost effective ways for it to be implemented. The New Zealand government has encouraged such a move to smart metering by ensuring the energy legislation is consistent with the delivery of benefits to the consumer while allowing innovation in this area. On the ground, AMS is a leader in the deployment of smart metering and associated services. Several of New Zealand’s energy retailers were looking for smart metering services for their residential and small business customers which will eventually account for over 500,000 meters when the multi-year national deployment program is concluded. To respond to these requirements, AMS needed to put together a solution that included data communications between each meter and the central data collection point and the solution proposed by Vodafone satisfied that requirement.

Case Study
Energy Saving & Power Monitoring System
Recently a university in Taiwan was experiencing dramatic power usage increases due to its growing number of campus buildings and students. Aiming to analyze their power consumption and increase their power efficiency across 52 buildings, the university wanted to build a power management system utilizing web-based hardware and software. With these goals in mind, they contacted Advantech to help them develop their system and provide them with the means to save energy in the years to come.
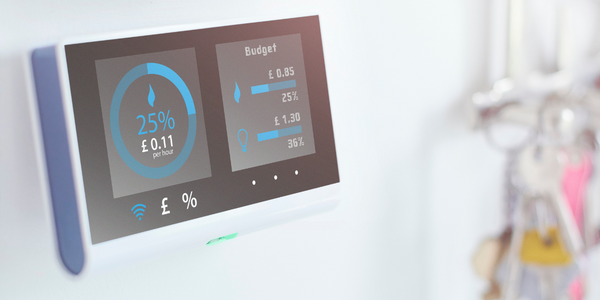
Case Study
NB-IoT connected smart meters to improve gas metering in Shenzhen
Shenzhen Gas has a large fleet of existing gas meters, which are installed in a variety of hard to reach locations, such as indoors and underground, meaning that existing communications networks have struggled to maintain connectivity with all meters. The meter success rate is low, data transmissions are so far unstable and power consumption is too high. Against this background, Shenzhen Gas, China Telecom, Huawei, and Goldcard have jointly trialed NB-IoT gas meters to try and solve some of the challenges that the industry faces with today’s smart gas meters.

Case Study
OneWireless Enabled Performance Guarantee Test
Tata Power's power generation equipment OEMs (M/s BHEL) is required to provide all of the instrumentation and measurement devices for conducting performance guarantee and performance evaluation tests. M/s BHEL faced a number of specific challenges in conducting PG tests: employing high-accuracy digital communications for instrumentation, shortening setup and dismantling time, reducing hardware required, making portable instrument setup, avoiding temporary cabling work and the material waste costs