Logistics Provider Closes More Business, Develops Stronger Customer Relationship
Company Size
200-1,000
Region
- America
- Europe
Country
- Belgium
- United States
Product
- E2open Transportation Management Application
Tech Stack
- XML-based API
Implementation Scale
- Enterprise-wide Deployment
Impact Metrics
- Customer Satisfaction
- Productivity Improvements
- Revenue Growth
Technology Category
- Application Infrastructure & Middleware - API Integration & Management
- Functional Applications - Transportation Management Systems (TMS)
Applicable Industries
- Chemicals
Applicable Functions
- Business Operation
- Logistics & Transportation
Use Cases
- Fleet Management
- Predictive Replenishment
- Supply Chain Visibility
Services
- Software Design & Engineering Services
- System Integration
About The Customer
A global logistics and transportation service provider (LSP) for the chemical and process industries works with a network of carriers and provides managed logistics, third-party and consulting services to clients such as Procter & Gamble, BASF® Chemtura® and Dial Corporation. With nearly 300 employees, the company is headquartered in Connecticut and has offices in North Carolina, New Jersey and Belgium. The LSP was looking to expand its global operations and, with its international customer base growing, the company also recognized it needed to automate its contract management and pricing process.
The Challenge
In thinking about what the company would need to meet its growth objectives, the logistics team realized the current process itself created a clear barrier to growth because it wasn’t scalable. Essentially, the team needed to manually look up contract and rate data for each new transaction. “We are expanding our business into international markets, adding new contracts and rates, and therefore needed a fully automated process that allowed us to handle more quoting without having to hire additional staff,” said the company’s SVP of Global Marine and International Logistics Services. Additionally, the growing company wanted to upgrade its service offerings by integrating an automated system into its own solution platform that would allow its customers, with little or no experience in pricing, to compare full bottom-line rates across multiple service contracts on their own.
The Solution
After a comprehensive vendor evaluation, the logistics provider selected a transportation management application from E2open to automate its contract management process and provide its customers with flexible and competitive routing and rate options for international shipments. This web-based application manages costs, automatically generates quotes and proposals and helps companies comply with tariff filing requirements. The logistics provider chose a platform that would enable the company to centrally manage its ocean service contracts, describing every term with a powerful rules engine to create “calculable contracts.” The platform looks at various options for route combinations in conjunction with potential tariffs that would apply if those routes were selected. This empowers users with little or no experience in pricing to compare full bottom-line rates across multiple service contracts, modes of transport, routings and service levels. The logistics provider also integrated the E2open transportation management application with its own branded platform using an XML-based application programming interface (API). This allows users to check an ocean rate stored in the E2open platform without leaving the logistics provider’s system.
Operational Impact
Quantitative Benefit
Case Study missing?
Start adding your own!
Register with your work email and create a new case study profile for your business.
Related Case Studies.
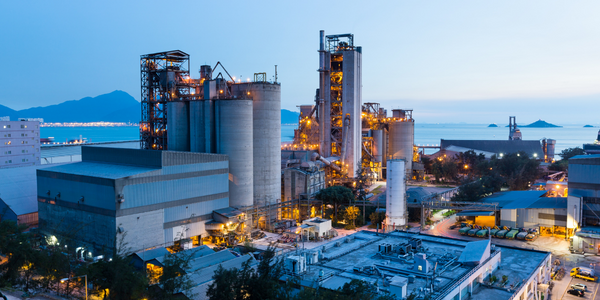
Case Study
Honeywell - Tata Chemicals Improves Data Accessibility with OneWireless
Tata was facing data accessibility challenges in the cement plant control room tapping signals from remote process control areas and other distant locations, including the gas scrubber. Tata needed a wireless solution to extend its control network securely to remote locations that would also provide seamless communication with existing control applications.

Case Study
Advanced Elastomer Systems Upgrades Production
In order to maintain its share of the international market for thermoplastic elastomers AES recently expanded its Florida plant by adding a new production line. While the existing lines were operating satisfactorily using a PROVOX distributed control system with traditional analog I/O, AES wanted advanced technology on the new line for greater economy, efficiency, and reliability. AES officials were anxious to get this line into production to meet incoming orders, but two hurricanes slowed construction.
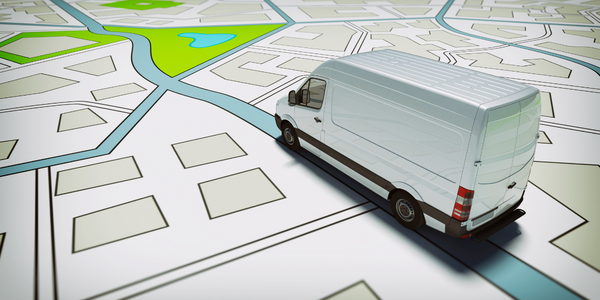
Case Study
Wireless GPS Tracking & Security Monitoring
Enhancing the security of hazardous freight and ensuring compliance with Homeland Security’s Transportation Security Administration mandate that all trains carrying chemicals capable of creating a toxic inhalation condition are equipped with on-board safety monitoring systems.
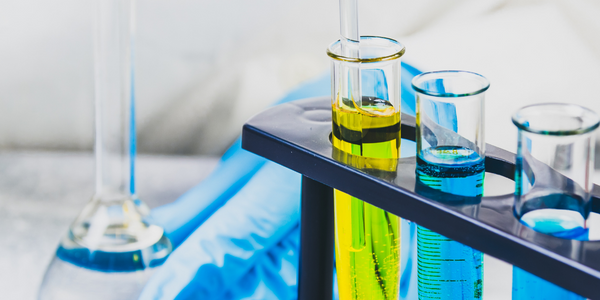
Case Study
Field Device Asset Management For Chemical Company in China
Chinese chemical subsidiary of multinational corporation serves customers throughout the world. Sales offices and research and technology centers are strategically located to provide rapid response to customer requests. Just two workers were assigned to maintain thousands of intelligent instruments in three production units, so they could do little more than react to device issues as they appeared. This costly maintenance method inevitably led to unexpected downtime when a critical instrument failed. Plant management recognized the need to change from reactive to predictive maintenance for all assets, including instruments and control valves, but help was needed in implementing such a technology-based initiative.
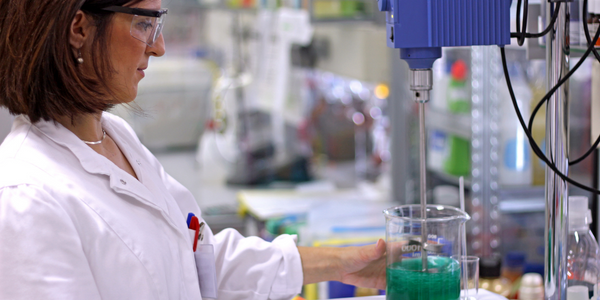
Case Study
Industrial Workforce Mobility for Improved Safety & Operations
Huntsman Corporation, a global manufacturer and marketer of differentiated chemicals, undertook an aggressive program to eliminate injuries, product defects, and environmental releases at their Port Neches facility. Termed “Project Zero”, this program required a completely mobile solution to empower operations and maintenance personnel to capture defects, track work progress and make process and safety related decisions in real-time.