KW Micro Power Creates Lightweight Multifunctional Microturbine Housing with Embedded Cooling Channels
Customer Company Size
SME
Region
- America
Country
- United States
Product
- nTopology
- VELO3D
Tech Stack
- Additive Manufacturing
- Conformal Cooling Channels
- Variable Shelling
Implementation Scale
- Enterprise-wide Deployment
Impact Metrics
- Cost Savings
- Productivity Improvements
- Innovation Output
Technology Category
- Other - Additive Manufacturing
- Functional Applications - Product Lifecycle Management Systems (PLM)
Applicable Industries
- Aerospace
Applicable Functions
- Product Research & Development
- Quality Assurance
Use Cases
- Additive Manufacturing
Services
- Software Design & Engineering Services
- System Integration
About The Customer
KW Micro Power is a small Florida-based manufacturer specializing in high power density Auxiliary Power Units (APUs) for commercial aviation and military applications. The company is known for its innovative approach to designing and manufacturing micro generator products optimized for various use cases. For landbound applications, weight is not a significant concern, but for APUs on board aircraft or drones, lightweighting is a top priority. KW Micro Power aims to stay at the forefront of the industry by adopting cutting-edge solutions and advanced engineering design tools.
The Challenge
KW Micro Power faced the challenge of reducing the weight of their aerospace-grade Auxiliary Power Units (APUs) for commercial aviation and military applications. The primary concern was to make the APUs lightweight without compromising on performance, as every gram counts in aerospace applications. Additionally, they needed to improve the thermal management of their high power density generator to ensure optimal performance and safety. The original CNC machined housing was heavy and did not offer integrated cooling solutions, which posed a significant challenge in achieving their goals.
The Solution
KW Micro Power leveraged nTopology's advanced engineering design tools to redesign the housing of their compact turbogenerator for metal Additive Manufacturing. The team used variable shelling to remove unnecessary material, creating a hollow shell with variable wall thickness. This process reduced the generator housing weight by 44%, from approximately 10.4 kg to 5.9 kg. Additionally, the hollow structure was converted into a conformal cooling channel to improve thermal management. The cooling channels used fuel as the heat transfer medium, preheating it from room temperature to 55°C, which increased the efficiency of the combustion process. The entire redesign process was performed almost instantaneously without errors and took less than a day before the part was ready for manufacturing.
Operational Impact
Quantitative Benefit
Case Study missing?
Start adding your own!
Register with your work email and create a new case study profile for your business.
Related Case Studies.
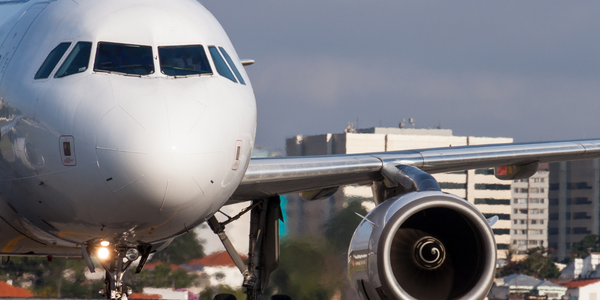
Case Study
Airbus Soars with Wearable Technology
Building an Airbus aircraft involves complex manufacturing processes consisting of thousands of moving parts. Speed and accuracy are critical to business and competitive advantage. Improvements in both would have high impact on Airbus’ bottom line. Airbus wanted to help operators reduce the complexity of assembling cabin seats and decrease the time required to complete this task.
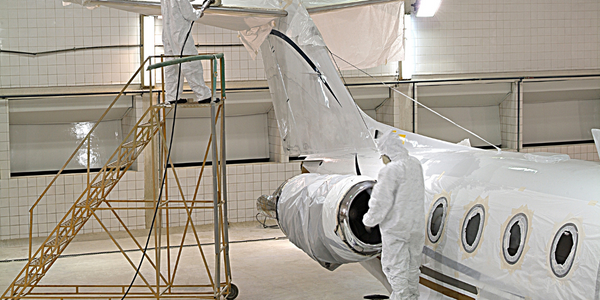
Case Study
Aircraft Predictive Maintenance and Workflow Optimization
First, aircraft manufacturer have trouble monitoring the health of aircraft systems with health prognostics and deliver predictive maintenance insights. Second, aircraft manufacturer wants a solution that can provide an in-context advisory and align job assignments to match technician experience and expertise.
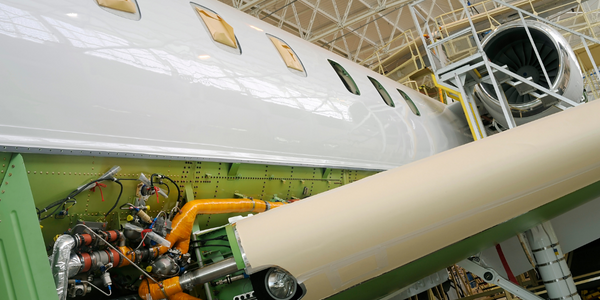
Case Study
Aerospace & Defense Case Study Airbus
For the development of its new wide-body aircraft, Airbus needed to ensure quality and consistency across all internal and external stakeholders. Airbus had many challenges including a very aggressive development schedule and the need to ramp up production quickly to satisfy their delivery commitments. The lack of communication extended design time and introduced errors that drove up costs.
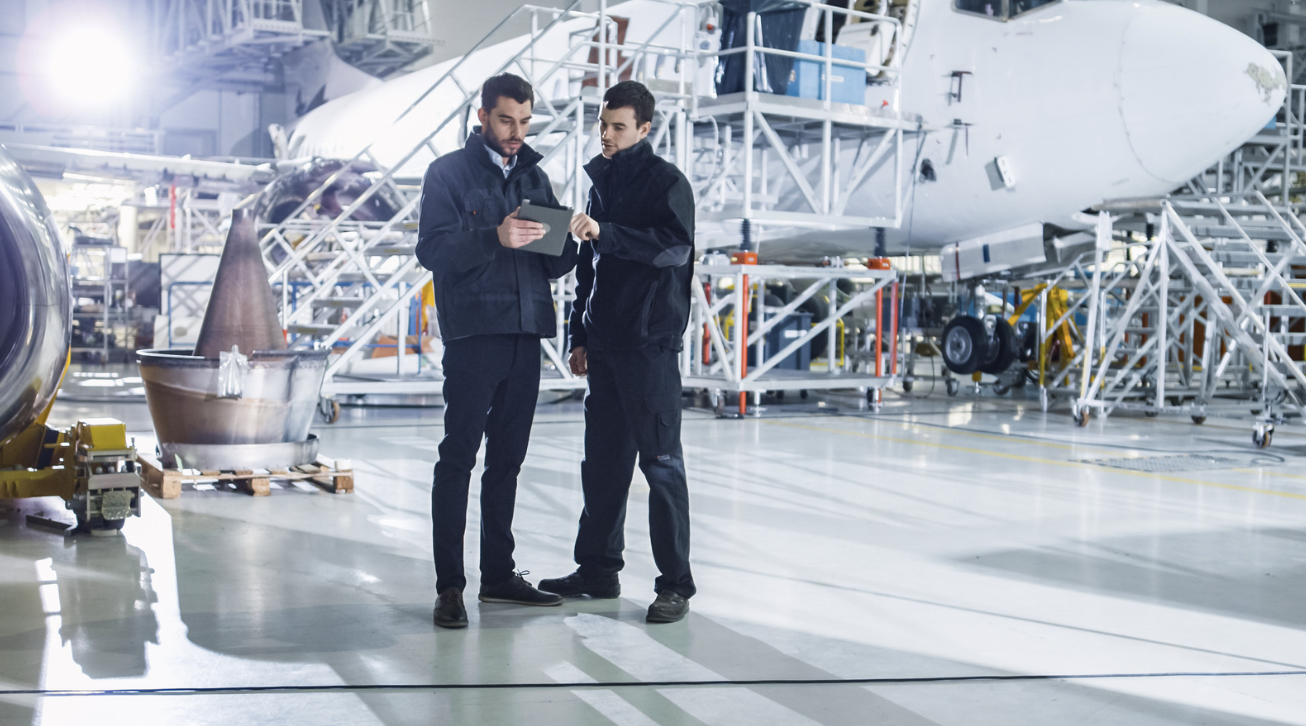
Case Study
Developing Smart Tools for the Airbus Factory
Manufacturing and assembly of aircraft, which involves tens of thousands of steps that must be followed by the operators, and a single mistake in the process could cost hundreds of thousands of dollars to fix, makes the room for error very small.
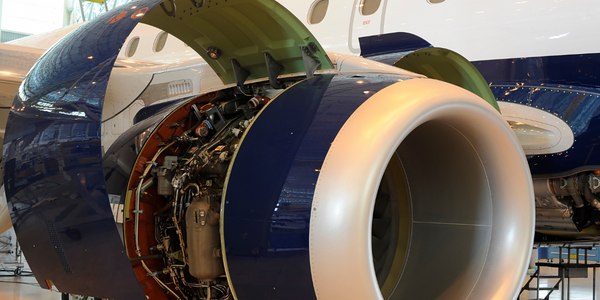
Case Study
Accelerate Production for Spirit AeroSystems
The manufacture and assembly of massive fuselage assemblies and other large structures generates a river of data. In fact, the bill of materials for a single fuselage alone can be millions of rows of data. In-house production processes and testing, as well as other manufacturers and customers created data flows that overwhelmed previous processes and information systems. Spirit’s customer base had grown substantially since their 2005 divestiture from Boeing, resulting in a $41 billion backlog of orders to fill. To address this backlog, meet increased customer demands and minimize additional capital investment, the company needed a way to improve throughput in the existing operational footprint. Spirit had a requirement from customers to increase fuselage production by 30%. To accomplish this goal, Spirit needed real-time information on its value chain and workflow. However, the two terabytes of data being pulled from their SAP ECC was unmanageable and overloaded their business warehouse. It had become time-consuming and difficult to pull aggregate data, disaggregate it for the needed information and then reassemble to create a report. During the 6-8 hours it took to build a report, another work shift (they run three per day) would have already taken place, thus the report content was out-of-date before it was ever delivered. As a result, supervisors often had to rely on manual efforts to provide charts, reports and analysis.