Technology Category
- Analytics & Modeling - Process Analytics
Applicable Industries
- Life Sciences
- Mining
Applicable Functions
- Logistics & Transportation
- Procurement
Use Cases
- Last Mile Delivery
Services
- System Integration
About The Customer
Johnson & Johnson is a multinational corporation that develops medical devices, pharmaceuticals, and consumer packaged goods. Founded in 1886, the company has grown to become one of the world's largest and most diverse healthcare companies, with operations in more than 60 countries. Johnson & Johnson's products are sold in over 175 countries, and the company employs approximately 132,200 people. The company is committed to innovation and continuous improvement, and is always looking for ways to optimize its processes and deliver better value to its customers.
The Challenge
Johnson & Johnson, a global healthcare and life sciences company, was seeking to digitize its continuous process improvement and bring its process mapping and discovery efforts into the 21st century. The company was facing challenges in identifying inefficiencies in their processes and understanding the value of Process Mining. The traditional methods of process improvement were not providing the desired results, and the company was looking for a more efficient and effective way to optimize their processes. The challenge was to find a solution that could be easily adopted by their global teams and provide consistent and rapid value creation.
The Solution
Johnson & Johnson identified Celonis as the perfect partner to help them digitize their process improvement efforts. They embarked on a proof of value exercise using Celonis to analyze data from a single system, uncover inefficiencies, and understand the value of Process Mining. This exercise quickly became a source of ongoing value, leading to the creation of global templates. These templates, enabled by Celonis, provided a strong foundation for Johnson & Johnson’s Process Center of Excellence. The company adopted a 'crawl, walk, run' methodology, getting users into the system and into their data as quickly as possible, refining user stories and analysis over time. The company also moved to a team-based methodology, creating metrics that could be leveraged upstream and downstream from the team that created them, while remaining tied to that team’s objectives.
Operational Impact
Quantitative Benefit
Case Study missing?
Start adding your own!
Register with your work email and create a new case study profile for your business.
Related Case Studies.
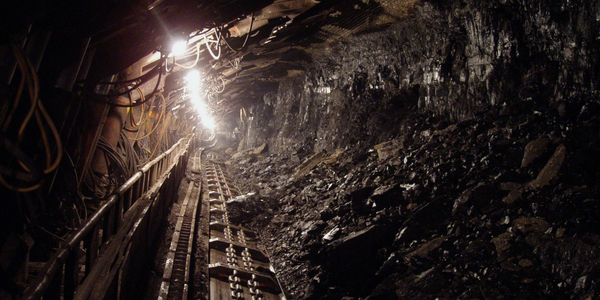
Case Study
Underground Mining Safety
The goal was to produce a safety system to monitor and support underground mining operations; existing systems were either too simple (i.e. phone line) or overly complex and expensive, inhibiting deployment, and providing little-to-no support in event of an accident. Given the dangerous nature of the mining work environment and the strict regulations placed on the industry, the solution would have to comply with Mine Safety and Health Administration (MSHA) regulations. Yet the product needed to allow for simple deployment to truly be a groundbreaking solution - increasing miner safety and changing daily operations for the better.
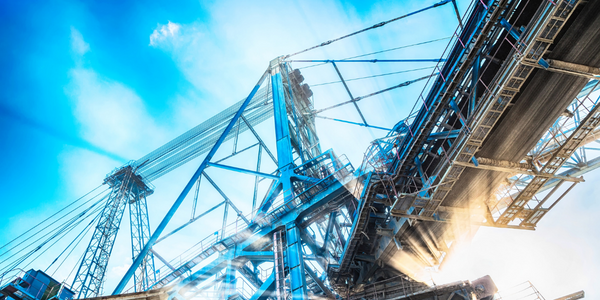
Case Study
Mining Firm Quadruples Production, with Internet of Everything
Dundee Precious Metal’s flagship mine, in Chelopech, Bulgaria, produces a gold, copper, and silver concentrate set a goal to increase production by 30%. Dundee wanted to increase production quality and output without increasing headcount and resources, improve miner safety, and minimize cost.
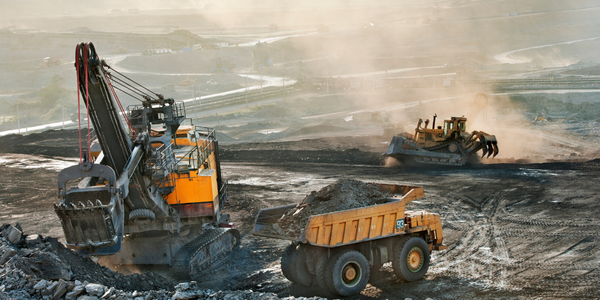
Case Study
Fastenal Builds the Future of Manufacturing with MachineMetrics
Fastenal's objective was to better understand their machine downtime, utilization, quality issues, and to embrace cutting-edge manufacturing technology/process improvement capabilities to bring their team to the next level. However, there was a lack of real-time data, visualization, and actionable insights made this transition impossible.
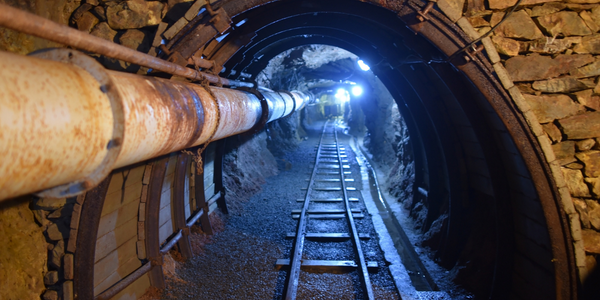
Case Study
Joy Mining Systems
Joy equipment faces many challenges. The first is machine integration and control. The business end of the machine has a rapidly-spinning cylinder with 6-inch diamond-studded cutting teeth. It chews through rock at rates measured in tens of tons per minute. The system grinds through the rock in front, creating a rectangular mine tunnel. Hydraulic lifters support the ceiling as the machine moves forward. Automated drills and screws drive 3-ft long screws into the ceiling to stabilize it. The rock and coal fall into a set of gathering "fingers" below the cutting cylinder. These fingers scoop up the rock and coal and deposit it onto a conveyor belt. The conveyor passes under the machine and out the back. A train of conveyor belt cars, up to a mile long, follows the cutter into the mine. The rock shoots along this train at over 400 feet per minute until it empties into rail cars at the end. Current systems place an operator cage next to the cutter. Choking dust (potentially explosive), the risk of collapse and the proximity of metal and rock mayhem make the operator cage a hazardous location.
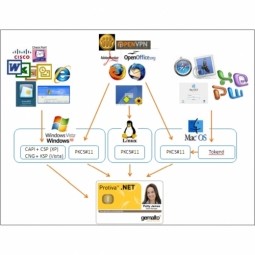
Case Study
Corporate Identity Solution Adds Convenience to Beckman Coulter
Beckman Coulter wanted to implement a single factor solution for physical and remote logical access to corporate network. Bechman Coulter's users were carrying smart card badges for doors, but also needed a one-time password token to access to our corporate network when they were not in the office. They wanted to simplify the process.
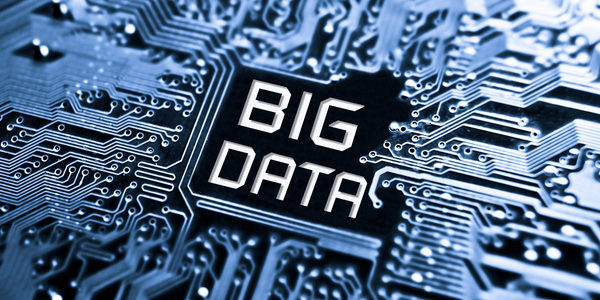
Case Study
Embracing Business Success in Real Time
· Increase control over growing Big Data to improve business decisions · Manage data for 28,000 biotechnology stockkeeping units in the fields of microbiology, molecular biology, animal cell cultures, plant tissue cultures, and lab ware for laboratory chemicals · Accelerate report generation and analysis with real-time data