IQMS Helps Plastic Components, Inc. Set the Leading Edge of Automated Manufacturing
Customer Company Size
Mid-size Company
Region
- America
Country
- United States
Product
- IQMS Manufacturing ERP
- RealTime Production Monitoring
- EnterpriseIQ ERP software system
Tech Stack
- Oracle database
- Windows-based PCs
Implementation Scale
- Enterprise-wide Deployment
Impact Metrics
- Productivity Improvements
- Cost Savings
- Revenue Growth
Technology Category
- Functional Applications - Enterprise Resource Planning Systems (ERP)
- Functional Applications - Manufacturing Execution Systems (MES)
Applicable Industries
- Electronics
- Equipment & Machinery
Applicable Functions
- Discrete Manufacturing
- Quality Assurance
Use Cases
- Manufacturing System Automation
- Predictive Maintenance
- Real-Time Location System (RTLS)
Services
- System Integration
- Software Design & Engineering Services
About The Customer
Based in Germantown, Wisconsin, Plastic Components, Inc. (PCI) is a globally competitive, low-cost producer of critical injection molded thermoplastic parts for original equipment manufacturers. Since 1989, the Wisconsin based company has relied on complete process automation to provide the highest quality parts at the lowest possible cost. With 40 dedicated manufacturing cells (presses, robots, parts conveyors and automated material handling systems) producing parts on a fully automated basis 24 hours a day, five days a week, PCI has shipped over one billion molded parts to customers throughout North America since its inception in 1989.
The Challenge
Plastic Components, Inc. (PCI) is a world-class injection molder of plastic parts. The company has established a reputation as a visionary manufacturer because it runs fully automated facilities: no direct labor is involved in their manufacturing process. However, at a little over a decade into their development, PCI’s information system was a potpourri of Excel spreadsheets, Access databases, and legal pads with pencils. They didn’t have a good handle on production scheduling, inventory, and true manufacturing costs. To address this situation, PCI conducted an assessment of a number of ERP systems, including IQMS. PCI committed to IQMS’ Manufacturing ERP, and spent nine months getting ready for implementation.
The Solution
IQMS’ Manufacturing ERP was implemented as the cornerstone of PCI's operation. The system supports the sophisticated automation the company instituted, allowing them to set up the process and the job, then run for prolonged periods of time. The system builds the buckets and work orders for every job they have, and determines when raw material is needed based on run times and must start dates from the customers. All the functions are scheduled on the floor. It defines exactly how many hours a sales order will need, and allows them to queue up the job that will follow. The system also provides PCI the functionality and planning to manage the complexity and direct operations, and does so with very limited input from PCI personnel.
Operational Impact
Quantitative Benefit
Case Study missing?
Start adding your own!
Register with your work email and create a new case study profile for your business.
Related Case Studies.

Case Study
Smart Water Filtration Systems
Before working with Ayla Networks, Ozner was already using cloud connectivity to identify and solve water-filtration system malfunctions as well as to monitor filter cartridges for replacements.But, in June 2015, Ozner executives talked with Ayla about how the company might further improve its water systems with IoT technology. They liked what they heard from Ayla, but the executives needed to be sure that Ayla’s Agile IoT Platform provided the security and reliability Ozner required.

Case Study
IoT enabled Fleet Management with MindSphere
In view of growing competition, Gämmerler had a strong need to remain competitive via process optimization, reliability and gentle handling of printed products, even at highest press speeds. In addition, a digitalization initiative also included developing a key differentiation via data-driven services offers.

Case Study
Remote Temperature Monitoring of Perishable Goods Saves Money
RMONI was facing temperature monitoring challenges in a cold chain business. A cold chain must be established and maintained to ensure goods have been properly refrigerated during every step of the process, making temperature monitoring a critical business function. Manual registration practice can be very costly, labor intensive and prone to mistakes.
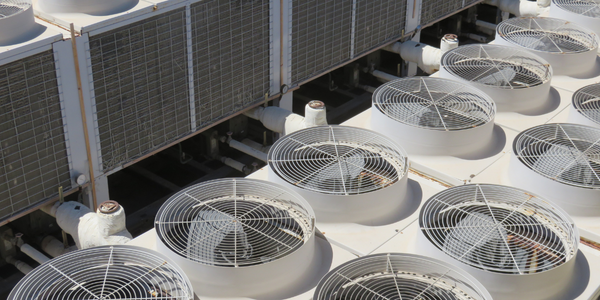
Case Study
Predictive Maintenance for Industrial Chillers
For global leaders in the industrial chiller manufacturing, reliability of the entire production process is of the utmost importance. Chillers are refrigeration systems that produce ice water to provide cooling for a process or industrial application. One of those leaders sought a way to respond to asset performance issues, even before they occur. The intelligence to guarantee maximum reliability of cooling devices is embedded (pre-alarming). A pre-alarming phase means that the cooling device still works, but symptoms may appear, telling manufacturers that a failure is likely to occur in the near future. Chillers who are not internet connected at that moment, provide little insight in this pre-alarming phase.

Case Study
Premium Appliance Producer Innovates with Internet of Everything
Sub-Zero faced the largest product launch in the company’s history:It wanted to launch 60 new products as scheduled while simultaneously opening a new “greenfield” production facility, yet still adhering to stringent quality requirements and manage issues from new supply-chain partners. A the same time, it wanted to increase staff productivity time and collaboration while reducing travel and costs.