Innovating Joint DLR/NASA Flying Observatory Using SOLIDWORKS Research Edition
Customer Company Size
Large Corporate
Region
- America
- Europe
Country
- Germany
- United States
Product
- SOLIDWORKS Research Edition
Tech Stack
- SOLIDWORKS Simulation
- SOLIDWORKS Modeling
Implementation Scale
- Enterprise-wide Deployment
Impact Metrics
- Innovation Output
- Productivity Improvements
- Customer Satisfaction
Technology Category
- Functional Applications - Remote Monitoring & Control Systems
- Analytics & Modeling - Predictive Analytics
Applicable Industries
- Aerospace
- Education
Applicable Functions
- Product Research & Development
- Quality Assurance
Use Cases
- Predictive Maintenance
- Digital Twin
- Remote Asset Management
Services
- Software Design & Engineering Services
- System Integration
About The Customer
The Stratospheric Observatory for Infrared Astronomy (SOFIA) is a unique flying observatory developed through a partnership between the German Aerospace Centre (DLR) and NASA. It is a refurbished Boeing 747 SP aircraft equipped with a 2.7-meter infrared telescope, allowing scientists to observe the infrared spectrum of light from the stratosphere. The German SOFIA Institute (DSI) at the University of Stuttgart and the Universities Space Research Association (USRA) in the United States coordinate its scientific operations. The project involves a consortium of German industry for the telescope's design and manufacturing, while NASA handles aircraft modifications, telescope installation, and operations. SOFIA's key advantage is its ability to position itself at precise locations to observe rare celestial events, providing a unique platform for astronomical research.
The Challenge
Develop and optimize telescope stabilization, a tracking camera, and interface systems for the Stratospheric Observatory for Infrared Astronomy (SOFIA), a flying observatory. The challenge was to create a system that could operate effectively in the stratosphere, where conditions are harsh and the need for precise stabilization is critical. The team needed to standardize on a common 3D design platform to facilitate collaboration and development, especially given the involvement of multiple disciplines and international partners.
The Solution
The SOFIA development team utilized SOLIDWORKS Research Edition software as the primary platform for designing and optimizing the telescope stabilization, tracking camera, and interface systems. The software's ease of use and integrated simulation tools made it an ideal choice for the project. The team used SOLIDWORKS modeling software to design various assemblies and components required to stabilize the telescope and tracking cameras during flight. They also leveraged SOLIDWORKS Simulation tools to validate and optimize design performance in the challenging operating environment of a moving aircraft in the stratosphere. The advanced design visualization capabilities in SOLIDWORKS facilitated communication across different disciplines involved in the project, including electronics, software, and optics development.
Operational Impact
Quantitative Benefit
Case Study missing?
Start adding your own!
Register with your work email and create a new case study profile for your business.
Related Case Studies.
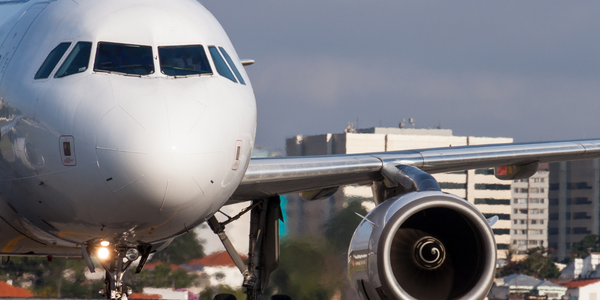
Case Study
Airbus Soars with Wearable Technology
Building an Airbus aircraft involves complex manufacturing processes consisting of thousands of moving parts. Speed and accuracy are critical to business and competitive advantage. Improvements in both would have high impact on Airbus’ bottom line. Airbus wanted to help operators reduce the complexity of assembling cabin seats and decrease the time required to complete this task.
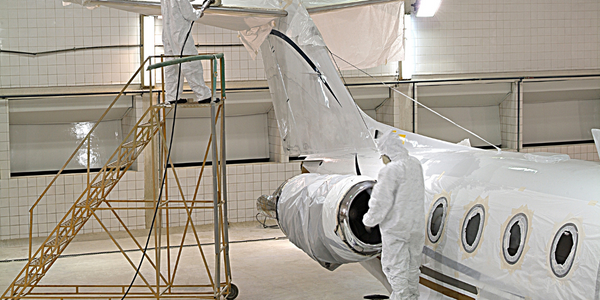
Case Study
Aircraft Predictive Maintenance and Workflow Optimization
First, aircraft manufacturer have trouble monitoring the health of aircraft systems with health prognostics and deliver predictive maintenance insights. Second, aircraft manufacturer wants a solution that can provide an in-context advisory and align job assignments to match technician experience and expertise.
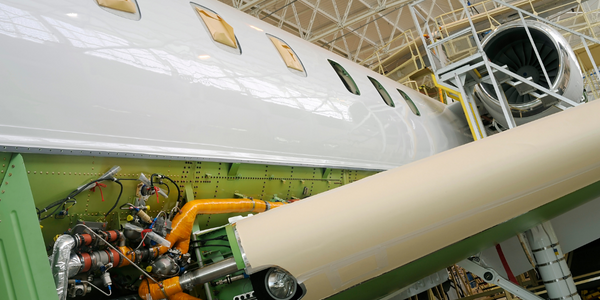
Case Study
Aerospace & Defense Case Study Airbus
For the development of its new wide-body aircraft, Airbus needed to ensure quality and consistency across all internal and external stakeholders. Airbus had many challenges including a very aggressive development schedule and the need to ramp up production quickly to satisfy their delivery commitments. The lack of communication extended design time and introduced errors that drove up costs.
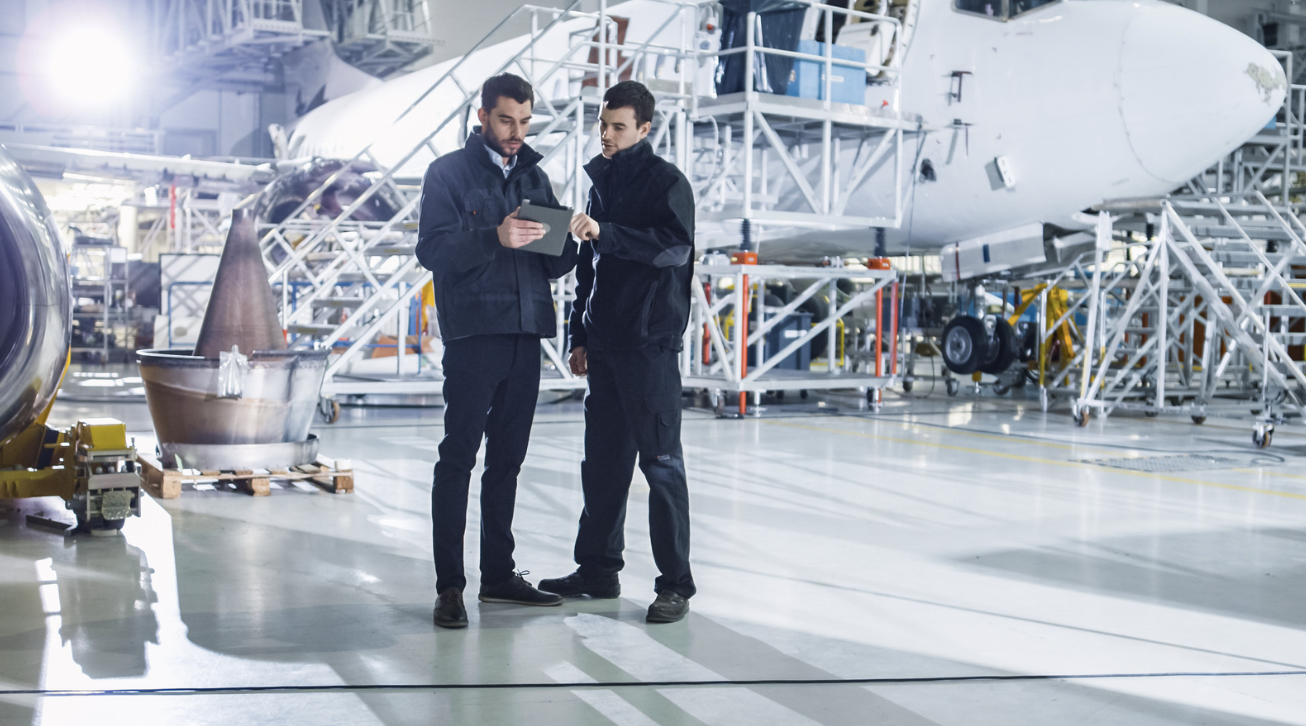
Case Study
Developing Smart Tools for the Airbus Factory
Manufacturing and assembly of aircraft, which involves tens of thousands of steps that must be followed by the operators, and a single mistake in the process could cost hundreds of thousands of dollars to fix, makes the room for error very small.
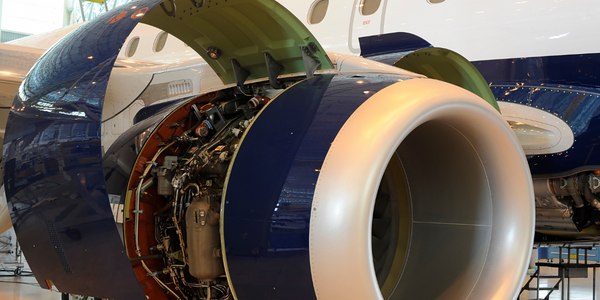
Case Study
Accelerate Production for Spirit AeroSystems
The manufacture and assembly of massive fuselage assemblies and other large structures generates a river of data. In fact, the bill of materials for a single fuselage alone can be millions of rows of data. In-house production processes and testing, as well as other manufacturers and customers created data flows that overwhelmed previous processes and information systems. Spirit’s customer base had grown substantially since their 2005 divestiture from Boeing, resulting in a $41 billion backlog of orders to fill. To address this backlog, meet increased customer demands and minimize additional capital investment, the company needed a way to improve throughput in the existing operational footprint. Spirit had a requirement from customers to increase fuselage production by 30%. To accomplish this goal, Spirit needed real-time information on its value chain and workflow. However, the two terabytes of data being pulled from their SAP ECC was unmanageable and overloaded their business warehouse. It had become time-consuming and difficult to pull aggregate data, disaggregate it for the needed information and then reassemble to create a report. During the 6-8 hours it took to build a report, another work shift (they run three per day) would have already taken place, thus the report content was out-of-date before it was ever delivered. As a result, supervisors often had to rely on manual efforts to provide charts, reports and analysis.