Innovating advanced astrophysical research systems with SolidWorks solutions
Customer Company Size
Large Corporate
Region
- America
Country
- United States
Product
- SolidWorks
- SolidWorks Premium
- SolidWorks Simulation Premium
- SolidWorks Enterprise PDM
- MasterCAM
Tech Stack
- 3D Development Platform
- CAD Tools
- Nonlinear Simulation
- Integrated Analysis Tools
Implementation Scale
- Enterprise-wide Deployment
Impact Metrics
- Cost Savings
- Productivity Improvements
- Innovation Output
Technology Category
- Functional Applications - Product Lifecycle Management Systems (PLM)
- Analytics & Modeling - Predictive Analytics
- Application Infrastructure & Middleware - Data Visualization
Applicable Industries
- Aerospace
Applicable Functions
- Product Research & Development
- Quality Assurance
Use Cases
- Predictive Maintenance
- Digital Twin
- Remote Asset Management
Services
- Software Design & Engineering Services
- System Integration
About The Customer
The Harvard-Smithsonian Center for Astrophysics (CFA) combines the resources and research facilities of the Harvard College Observatory and the Smithsonian Astrophysical Observatory (SAO) under a single director to pursue studies of the physical processes that determine the nature and evolution of the universe. Some 300 Smithsonian and Harvard scientists cooperate in broad programs of astrophysical research. SAO’s Engineering Group collaborates with astrophysicists and scientists on the development of cutting-edge research instruments and systems.
The Challenge
Accelerate scientific research system development and enhance design visualization to improve collaboration with astrophysical scientists and researchers.
The Solution
Implement SolidWorks and SolidWorks Premium design software, SolidWorks Simulation Premium analysis software, and SolidWorks Enterprise PDM product data management software solutions. These tools allow SAO engineers to model and visualize designs, conduct nonlinear buckling, vibration, thermal, and frequency analyses, and optimize project designs. The integration with MasterCAM machining software further streamlines the process, enabling efficient and cost-effective development of research systems.
Operational Impact
Quantitative Benefit
Case Study missing?
Start adding your own!
Register with your work email and create a new case study profile for your business.
Related Case Studies.
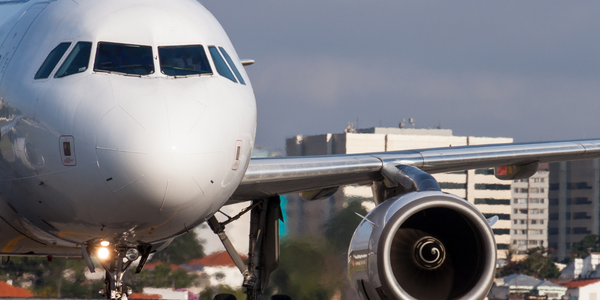
Case Study
Airbus Soars with Wearable Technology
Building an Airbus aircraft involves complex manufacturing processes consisting of thousands of moving parts. Speed and accuracy are critical to business and competitive advantage. Improvements in both would have high impact on Airbus’ bottom line. Airbus wanted to help operators reduce the complexity of assembling cabin seats and decrease the time required to complete this task.
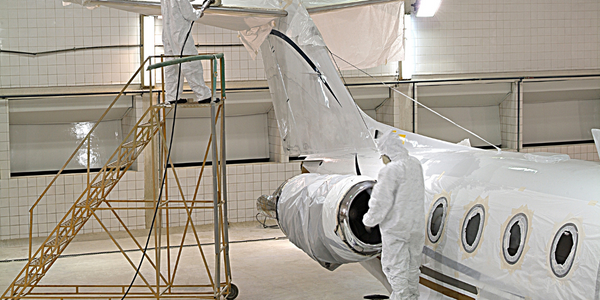
Case Study
Aircraft Predictive Maintenance and Workflow Optimization
First, aircraft manufacturer have trouble monitoring the health of aircraft systems with health prognostics and deliver predictive maintenance insights. Second, aircraft manufacturer wants a solution that can provide an in-context advisory and align job assignments to match technician experience and expertise.
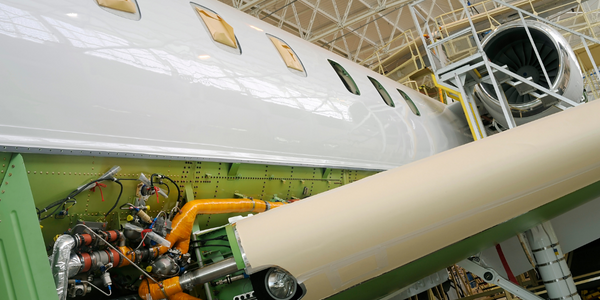
Case Study
Aerospace & Defense Case Study Airbus
For the development of its new wide-body aircraft, Airbus needed to ensure quality and consistency across all internal and external stakeholders. Airbus had many challenges including a very aggressive development schedule and the need to ramp up production quickly to satisfy their delivery commitments. The lack of communication extended design time and introduced errors that drove up costs.
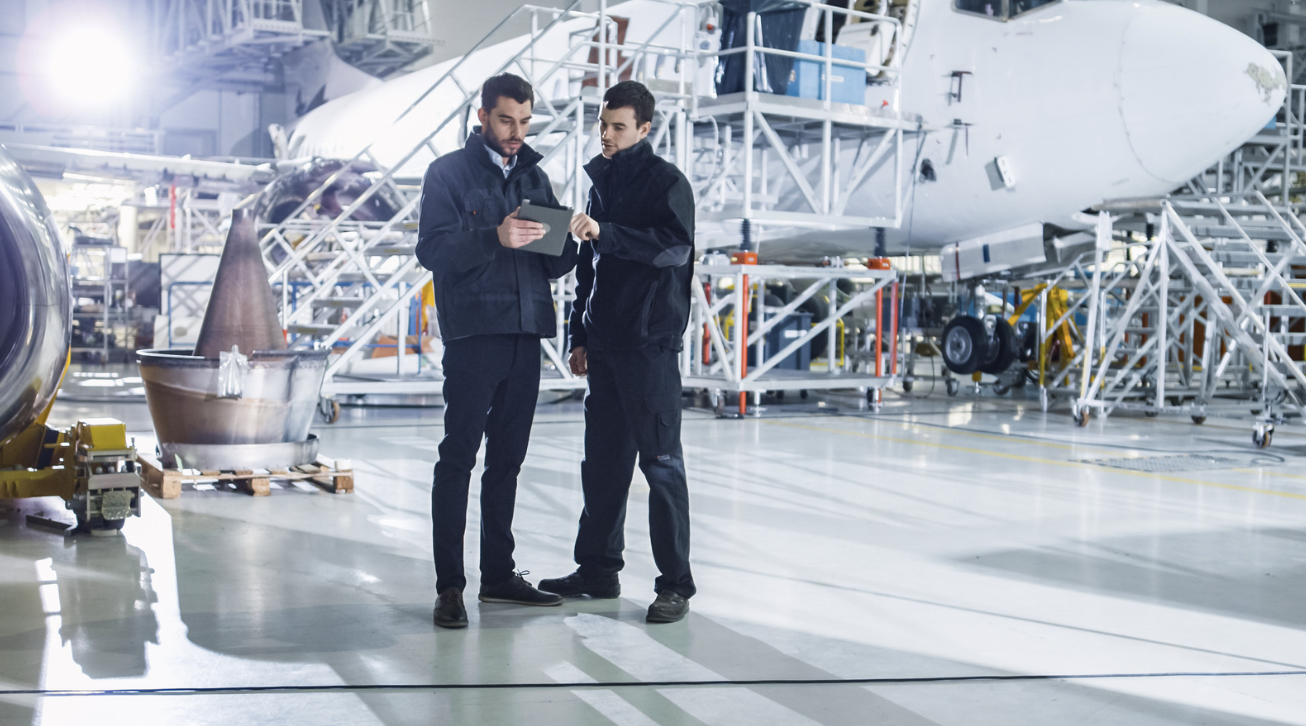
Case Study
Developing Smart Tools for the Airbus Factory
Manufacturing and assembly of aircraft, which involves tens of thousands of steps that must be followed by the operators, and a single mistake in the process could cost hundreds of thousands of dollars to fix, makes the room for error very small.
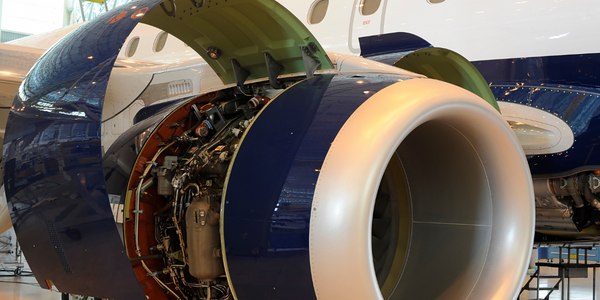
Case Study
Accelerate Production for Spirit AeroSystems
The manufacture and assembly of massive fuselage assemblies and other large structures generates a river of data. In fact, the bill of materials for a single fuselage alone can be millions of rows of data. In-house production processes and testing, as well as other manufacturers and customers created data flows that overwhelmed previous processes and information systems. Spirit’s customer base had grown substantially since their 2005 divestiture from Boeing, resulting in a $41 billion backlog of orders to fill. To address this backlog, meet increased customer demands and minimize additional capital investment, the company needed a way to improve throughput in the existing operational footprint. Spirit had a requirement from customers to increase fuselage production by 30%. To accomplish this goal, Spirit needed real-time information on its value chain and workflow. However, the two terabytes of data being pulled from their SAP ECC was unmanageable and overloaded their business warehouse. It had become time-consuming and difficult to pull aggregate data, disaggregate it for the needed information and then reassemble to create a report. During the 6-8 hours it took to build a report, another work shift (they run three per day) would have already taken place, thus the report content was out-of-date before it was ever delivered. As a result, supervisors often had to rely on manual efforts to provide charts, reports and analysis.